外文翻譯原文-高架起重機(jī)橋架的建模與有限元分析
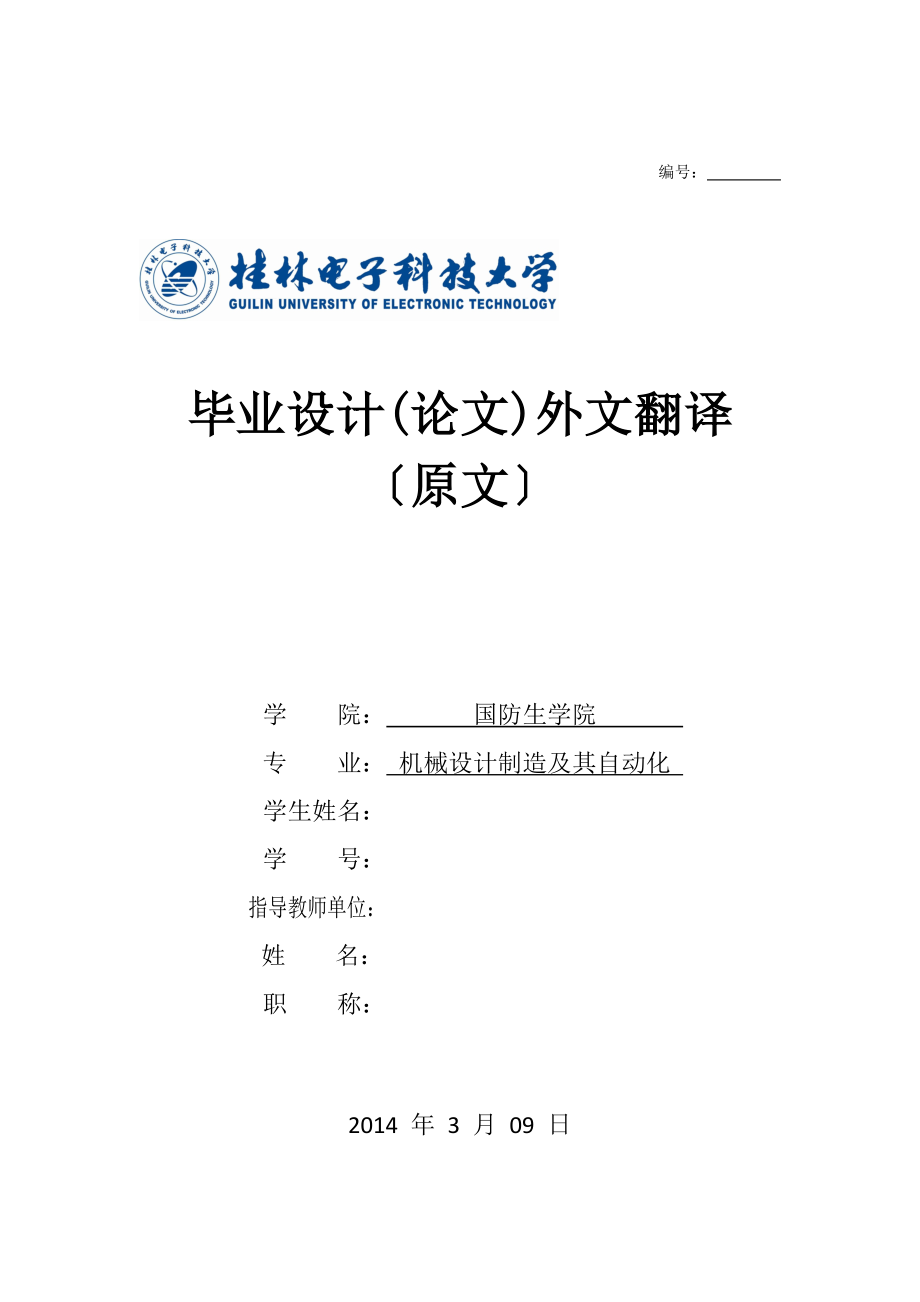


《外文翻譯原文-高架起重機(jī)橋架的建模與有限元分析》由會(huì)員分享,可在線閱讀,更多相關(guān)《外文翻譯原文-高架起重機(jī)橋架的建模與有限元分析(26頁(yè)珍藏版)》請(qǐng)?jiān)谘b配圖網(wǎng)上搜索。
1、 編號(hào): 畢業(yè)設(shè)計(jì)(論文)外文翻譯 〔原文〕 學(xué) 院: 國(guó)防生學(xué)院 專 業(yè): 機(jī)械設(shè)計(jì)制造及其自動(dòng)化 學(xué)生姓名: 學(xué) 號(hào): 指導(dǎo)教師單位: 姓 名: 職 稱: 2014 年 3 月 09 日 Solid Modeling and Finite Element Analysis of an Overhead Crane Bridge
2、 C. Alkin, C. E. Imrak, H. Kocabas Abstract The design of an overhead crane bridge with a double box girder has been investigated and a case study of a crane with 35 ton capacity and 13 m span length has been conducted. In the initial phase of the case study, conventional design calculations
3、proposed by F. E.M Rules and DIN standards were performed to verify the stress and deflection levels. The crane design was modeled using both solids and surfaces. Finite element meshes with 4-node tetrahedral and 4-node quadrilateral shell elements were generated from the solid and shell models, res
4、pectively. After a comparison of the finite element analyses, the conventional calculations and performance of the existing crane, the analysis with quadratic shell elements was found to give the most realistic results. As a result of this study, a design optimization method for an overhead crane is
5、 proposed. Keywords: overhead crane, finite element method, solid modeling, box girder. Notation b distance between two side plates bk width of lower plate FAA static load due to the trolley FY load due to the working load h0 height of the girder end h2 height of the side plat
6、es LA distance between trolley wheels LK span of crane girder LP distance between two adjacent supports q weight of one meter platform qK weight of one meter maintenance platform qP uniformly distributed mass units of bridge t1 thickness of the upper and lower plates t2 thic
7、kness of the side plates x2 distance between center of gravity and the midpoint of the left side plate x4 distance between center of gravity and the midpoint of the rail y1 distance between neutral axis and the midpoint of the rail y3 distance between center of gravity and the midpoint o
8、f the top plate y5 distance between neutral axis and the midpoint of the top plate WX1 moment of resistance on x-axis WY1 moment of resistance on y-axis amplifying coefficient dynamic coefficient 1 Introduction Cranes are the best way of providing a heavy lifting facility covering
9、virtually the whole area of a building. An overhead crane is the most important materials handling system for heavy goods. The primary task of the overhead crane is to handle and transfer heavy payloads from one position to another. Thus they are used in areas such as automobile plants and shipyards
10、 [1, 2]. Their design features vary widely according to their major operational specifications, such as: type of motion of the crane structure, weight and type of the load, location of the crane, geometric features and environmental conditions. Since the crane design procedures are highly standardiz
11、ed with these components, most effort and time are spent on interpreting and implementing the available design standards [3]. There are many published studies on structural and component stresses, safety under static loading and dynamic behavior of cranes [5–16]. Solid modeling of bridge structure
12、s and finite element analysis to find the displacements and stress values has been investigated by Demirsoy [17].Solid modeling techniques applied for road bridge structures, and an analysis of these structures using the finite element method are provided in [18]. In this study, stress and displacem
13、ents were found using FEM90 software. Solid modeling of a crane bridge, the loading at different points on the bridge and then application of the finite element method have been studied by Celiktas [19]. She presented the results of finite element methods for an overhead crane. DIN-Taschenbuch and
14、 F. E. M. (Federation Européenne de la Manutention) Rules offer design methods and empirical approaches and equations that are based on previous design experience and widely accepted design procedures. DIN--Taschenbuch 44 and 185 are a collection of standards related to crane design. DIN norms gener
15、ally state standard values of design parameters. F. E. M Rules are mainly an accepted collection of rules to guide crane designers. It includes criteria for deciding on the external loads to select crane components [3, 20]. In this study, the calculations apply the F. E. M. rules and DIN standards,
16、 which are used for box girder crane bridges. The calculation of the box girder uses the CESAN Inc. standard bridge tables. Then a solid model of the crane bridge is generated with the same dimensions as in the calculation results. Then static analysis is performed, using the Finite Element Method.
17、Before starting the solution, the boundary conditions are applied as in practice. 2 Overhead cranes with a double box girder Overhead travelling cranes with a double box girder not only hoist loads but also carry them horizontally. A double beam overhead crane is built of a trolley travelling on b
18、ridges, and bridges travelling on rails. The trolley hoists or lowers the loads and carries them on the bridge structure. The bridges carry the loads on a rail. As a result, three perpendicular movements are performed. The system is depicted in Fig. 1, where the payload of the mass is attached to th
19、e bridge with wire ropes [21, 22]. The double box girders are subjected to vertical and horizontal loads by the weight of the crane, the working (hook) load and the dynamic loads. With a double box girder construction, the trolley runs above or between the girders. The acceptable construction requ
20、irements and values for a box girder bridge structure are shown in Fig.2. Fig. 1: Overall view of an overhead crane Fig. 2: Construction requirements for a box girder bridge 3 Application of FEM to an overhead crane Among numerical techniques, the finite element method is widel
21、y used due to the availability of many user-friendly commercial softwares. The finite element method can analyse any geometry, and solves both stresses and displacements [23]. FEM approximates the solution of the entire domain under study as an assemblage of discrete finite elements interconnected a
22、t nodal points on the element boundaries. The approximate solution is formulated over each element matrix and thereafter assembled to obtain the stiffness matrix, and displacement and force vectors of the entire domain. In this study finite element modeling is carried out by means of the Cosmos Work
23、s and MSC commercial package. Patran and 4-node tetrahedral elements and 4-node quadrilateral shell elements have been used for modeling the overhead crane bridge. The four-node tetrahedral element is the simplest three--dimensional element used in the analysis of solid mechanics problems such as b
24、racket stress analysis. This element has four nodes, with each node having three translational and three rotational degrees of freedom on the x, y, and z-axes. A shell element may be defined, which allows in the plane or curved surface of the element and posses both length. It width and may only be
25、 used in 3-D simulations. The four--node shell element is obtained by assembling the bending element to the appropriate degrees of freedom. This is sufficient as long as the shell element deflection is within the predefined ratio of shell thickness, otherwise the system works as a large deflection.
26、 A typical four-node tetrahedral element and four-node quadratic shell element, and their coordinate systems are illustrated in Fig. 3 [24]. The four-node tetrahedral element chosen has six degrees of freedom at each node: translation in the nodal x, y, and z directions and rotations about the nodal
27、 x, y, and z directions. For the four-node quadratic shell element used to model the overhead crane girder, r and s denote the natural coordinates and δ is the thickness of the element. This system does not have any horizontal force. The axial displacements and rotations of the first and last faces
28、 are equal to zero. In addition, the transverse displacement is zero at the first and last face nodes. The external forces acting on the system are the mass of the main girder of the crane (distributed load) and the forces acting on the wheels of the trolley along the crane (active load). The force
29、s acting on the trolley wheels are caused by the mass of the trolley, an the lifting load which will be moved on the crane. 4-node tetrahedral element 4-node quadratic shell element Fig. 3: Elements used to model an overhead crane girder 4 Solid and finite element modeling of an overhead
30、 crane bridge The finite element method is a numerical procedure that can be applied to obtain solutions to a variety of problems in engineering. Steady, transient, linear or nonlinear problems in stress analysis, heat transfer, fluid flow and electrome chanism problems may be analysed with finite
31、element methods. The basic steps in the finite element method are defined as follows: preprocessing phase, solution phase, and post processing phase. Real crane data was gathered from CESAN Inc., a Turkish company involved in mass production of overhead cranes. First, the crane bridge is modeled a
32、s a surface. Bridge geometry is suitable for this, and long and thin parts should also be modeled as a surface. Later, a mesh is created. In this study, a quadratic element type is used. Solid modeling is generated for the calculated crane bridge and the solid model is shown in Fig. 4 [20]. Solid
33、 model of a crane bridge Wireframe view of a crane bridge Fig. 4: Models of an overhead crane bridge 5 Numerical example of an overhead crane A 35-ton-capacity overhead crane of overall length 13 m and total weight 22.5 tons was selected as a study object. The configuration of the overh
34、ead crane is shown in Fig. 1.The overhead crane consists of two girders, two saddles to connect them, and a trolley moving in the longitudinal direction of the overhead crane and wheels. The driving unit is installed in one of the two girders. The overhead crane is supported by two rails and the run
35、way girders installed in building. In order to calculate the stress in the structure, the rules of F. E. M 1.001 are applied. The design values used in the bridge analysis from the F. E.M and DIN standards are given in Table 1. Table 1: Bridge property values Handling Capacity : =35 ton
36、 Trolley Weight : =3 ton Bridge Length : =13 m Distance between wheels of trolley : =2m Trolley Velocity : =20 m/min. Crane Velocity : =15 m/min. Hoisting Velocit : =2.7 m/min Total duration of use : U4 Load spectrum class : Q3 Appliance group : A5 Loading type : H (main load)
37、 Dynamic coefficient :ψ Amplifying coefficient First the maximum and minimum stresses and then the shear stress are calculated using the F. E. M. rules. Using the finite element method for the considered girder, we obtain the stress valnes. We obtain the s
38、tatic loads due to the dead weight, the loads due to the working load multiplied by the dynamic coefficient, and the two most unfavourable horizontal effects, excluding the buffer forces. The maximum stress consists of the stress on the bridge dead weights, the stress on the trolley dead weight, th
39、e stress from the hoisting load, stress from the inertia forces and the stress of the trolley contraction. The minimum stress includes the stress on the bridge dead weights and the stress on the trolley dead weight. The maximum and minimum stresses for the given values according to the F. E.M. rules
40、 [20] are written in standard form as and, , The value of the dynamic coefficient ψ is applied to the loading arising from the working load. The value of the amplifying coefficient depends the group classification of the application, and the weight of one meter maintenance platform is zero in
41、this work. [25]. It is assumed that the total load (372780 N) is effected on the midpoint of the rail and each girder shares this total load equally. This load is applied via the contact points of the two trolley wheels in this system. Therefore the value of the acting force on each point is 93195
42、N. Applying the total load in the system, the value of the maximum stress according to Eq. (1) is 143.90 N/mm2 to two decimal places, and the value of the minimum stress according to Eq. (2) is 47.33 N/mm2 to two decimal places. According to Fig. 5, the permissible stress in shear consists of the s
43、hear stresses of the wheel forces, and is defined as [20] The value of the maximum shear stress is 24.82 N/mm2 to two decimal places from Eq. (5). Substituting Eq. (1)–(3) the equivalent stress is given by. The value of the equivalent stress is 150.18 N/mm2 to two decimal places. Fig. 5: Inert
44、ia and moment of resistance in a box girder 6 Results from a girder model with a four-node tetrahedral element To model the overhead crane girder with a four-node tethrahedral element, Cosmosworks software was used for finite element analysis using the girder solid model generated by means of So
45、lidWorks 2003. Young’s Modulus (E) is 2.1×105 N/mm2 and the Poisson Ratio () is 0.3 for finite element analysis. The value of the maximum stress of the side plate is 12.07 N/mm2 to two decimal places and the value of the maximum stress of the bottom plate is 15.08N/mm2 to two decimal places from Fig
46、. 6 [20]. The displacement of the modelled overhead crane girder was obtained from CosmosWorks, and is illustrated in Fig. 7. The value of maximum displacement of the girder is about 2.2 mm. Fig. 6: Stress values of an overhead crane girder with a four-node tetrahedral element Fig. 7: Displ
47、acements of an overhead crane girder with a four-node tetrahedral element 7 Results from a girder model with a four-node quadratic shell element To model the overhead crane girder with a four-node quadratic shell element, MSC Patran software was used for the finite element analysis. Young’s Modulu
48、s (E) is 2.1×10 N/mm2 and the Poisson Ratio (_St) is 0.3 for finite element analysis. The value of the maximum stress of the side plate is 35.40 N/mm2 to two decimal places, and the value of the maximum stress of the bottom plate is 49.30 N/mm2 to two decimal places, from Fig. 8 [20]. The displacem
49、ent of the modelled overhead crane girder was obtained from MSC Patran, and is illustrated in Fig. 9.The value of maximum displacement of the girder is about 3.89 mm. The value of the maximum stress according to Eq. (1) is calculated as 143.90 N/mm2 to two decimal places. The safety factor should
50、be considered between 2 and 3 for overhead crane girder design. The maximum stress value of the side plate is between 24.14 and 36.21 N/mm2 to two decimal places, and the maximum stress value of the bottom plate is between 30.16 and 45.24 N/mm2 to two decimal places for a four-node tetrahedral eleme
51、nt, taking into account the safety factor. The maximum stress value of the side plate is between 70.8 and 106.2 N/mm2 to two decimal places and the maximum stress value of the bottom plate is between 98.6 and 147.9 N/mm2 to two decimal places for a four-node quadratic shell element, taking into acc
52、ount the safety factor. The permissible displacement of the girder is 13 mm according to F. E.M. rules. The maximum displacement obtained from the finite element model with a four-node tetrahedral element is between 4.40 and 6.60 mm, taking into account the safety factor. The maximum displacement
53、obtained from the finite element model with a four-node quadratic shell element is between 7.78 and 11.67 mm, taking into account the safety factor. Fig. 8: Stress values of an overhead crane girder with a quadratic shell element Fig. 9: Displacements of an overhead crane girder with a four-no
54、de quadratic shell element 8 Conclusion In this study, unlike the other studies carried out previously, shell elements in finite element modeling of an overhead box girder have been examined. In order to show the use of shell elements, one illustrative overhead crane bridge example is given. The m
55、aximum stress value is 143.90 N/mm2 and 45.24 N/mm2 for a four-node tetrahedral element and 147.9 N/mm2 for a four-node quadratic shell element using both calculations according to the F. E. M. Rules and finite element analysis. The value of the equivalent stress is 150.18 N/mm2 to two decimal place
56、s. Taking into account the safety factor, the stress value varies between 97–145.5N/mm2, which is obtained from MSC Patran. The ratio of length to thickness of the element used in modelling the overhead crane box girder is higher than 20. Therefore, in order to show the accuracy of the analysis of
57、the overhead crane bridges, a four-node quadratic shell element is used instead of the four-node tetrahedral element for finite element analysis. Acknowledgment It is pleasure to acknowledge much stimulating correspondence with Dr. Haydar Livatyali and gratefully to acknowledge the support of CESA
58、N Inc., which provided the design data. Machine tool numerical control reforms 1 CNC systems and the development trend of history 1946 birth of the world's first electronic computer, which shows that human beings created to enhance and replace some of the mental work tools. It and human agri
59、culture, industrial society in the creation of those who merely increase compared to manual tools, from a qualitative leap for mankind's entry into the information society laid the foundation. Six years later, in 1952, computer technology applied to the machine in the United States was born first CN
60、C machine tools. Since then, the traditional machine produced a qualitative change. Nearly half a century since the CNC system has experienced two phases and six generations of development. 1.1 Numerical Control (NC) phase (1952 to 1970) Early computer's computational speed low and the prevailing
61、scientific computing and data processing is not affected, but can not meet the requirements of real-time control machine. People have to use digital logic circuit "tied" into a single machine as a dedicated computer numerical control system, known as the hardware connection NC (HARD-WIRED NC), calle
62、d the Numerical Control (NC). With the development of components of this phase after three generations, that is, in 1952 the first generation - tube; 1959 of the second generation - transistor; 1965 of the third generation - small-scale integrated circuits. 1.2 Computer Numerical Control (CNC) phas
63、e (1970 to present) To 1970, GM has been a small computer and mass-produced. So it transplant system as the core component of NC, have entered a Computer Numerical Control (CNC) stage(in front of the computer should be "universal" word omitted). To 1971, the United States INTEL company in the world
64、 will be the first time the two most core computer components - computing and controller, a large-scale integrated circuit technology integration in a chip, called the microprocessor (MICROPROCESSOR) , also known as the central processing unit (CPU). 1974 microprocessor to be used in CNC system. Th
65、is is because the function of the computer is too small to control a machine tool capacity affluent (the time has been used to control more than one machine, called Group Control), as a reasonable economic use of the microprocessor. Minicomputer reliability and then not ideal. Early microprocessor s
66、peed and functionality while still not high enough, but can be adopted to solve the multi-processor architecture. As microprocessor core is a general computer components, it is still known as the CNC. By 1990, PC machines (personal computers, domestic habits that computer) performance has been developed to a high stage, as a CNC system to meet the requirements of the core components. NC system based on PC has now entered the stage. In short, CNC has also experienced a stage three generations.
- 溫馨提示:
1: 本站所有資源如無(wú)特殊說(shuō)明,都需要本地電腦安裝OFFICE2007和PDF閱讀器。圖紙軟件為CAD,CAXA,PROE,UG,SolidWorks等.壓縮文件請(qǐng)下載最新的WinRAR軟件解壓。
2: 本站的文檔不包含任何第三方提供的附件圖紙等,如果需要附件,請(qǐng)聯(lián)系上傳者。文件的所有權(quán)益歸上傳用戶所有。
3.本站RAR壓縮包中若帶圖紙,網(wǎng)頁(yè)內(nèi)容里面會(huì)有圖紙預(yù)覽,若沒(méi)有圖紙預(yù)覽就沒(méi)有圖紙。
4. 未經(jīng)權(quán)益所有人同意不得將文件中的內(nèi)容挪作商業(yè)或盈利用途。
5. 裝配圖網(wǎng)僅提供信息存儲(chǔ)空間,僅對(duì)用戶上傳內(nèi)容的表現(xiàn)方式做保護(hù)處理,對(duì)用戶上傳分享的文檔內(nèi)容本身不做任何修改或編輯,并不能對(duì)任何下載內(nèi)容負(fù)責(zé)。
6. 下載文件中如有侵權(quán)或不適當(dāng)內(nèi)容,請(qǐng)與我們聯(lián)系,我們立即糾正。
7. 本站不保證下載資源的準(zhǔn)確性、安全性和完整性, 同時(shí)也不承擔(dān)用戶因使用這些下載資源對(duì)自己和他人造成任何形式的傷害或損失。
最新文檔
- 《筍芽?jī)骸氛n件
- 高速鐵路同相供電
- 二年級(jí)語(yǔ)文下冊(cè)-第4單元-13《激光的話》課件4-語(yǔ)文S版
- 《一枚金幣》課件
- 1441單項(xiàng)式乘以多項(xiàng)式(課件)PPT
- 12分式的乘法和除法
- 常見(jiàn)蔬菜分類
- 保險(xiǎn)客戶經(jīng)營(yíng)1361法則
- 現(xiàn)場(chǎng)目視管理與看板管理
- 高中政治-4.2文化在繼承中發(fā)展課件1-新人教版必修3PPT文檔
- 八年級(jí)生物上冊(cè) 181 微生物在生物圈中的作用(第2課時(shí))課件(2)(新版)北師大版
- 人生的夢(mèng)想
- 動(dòng)物生理學(xué)-第六章課件
- IE經(jīng)典管理基礎(chǔ)
- AfternoonandEvening課件