端蓋落料拉深沖孔復合模設計畢業(yè)設計論文
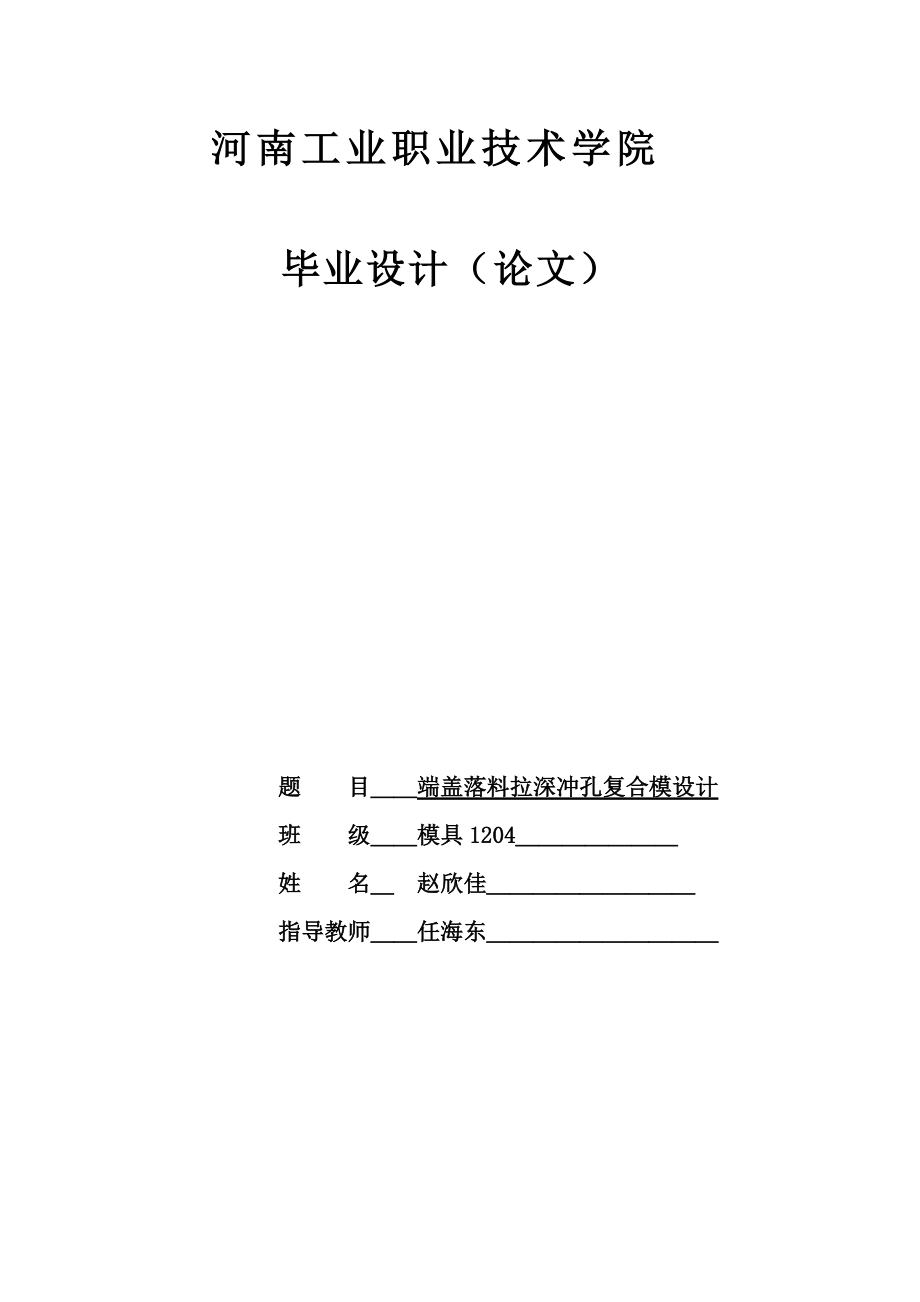


《端蓋落料拉深沖孔復合模設計畢業(yè)設計論文》由會員分享,可在線閱讀,更多相關《端蓋落料拉深沖孔復合模設計畢業(yè)設計論文(38頁珍藏版)》請在裝配圖網(wǎng)上搜索。
1、 河南工業(yè)職業(yè)技術學院 畢業(yè)設計(論文) 題 目__端蓋落料拉深沖孔復合模設計 班 級__模具1204_______ 姓 名_ 趙欣佳_________ 指導教師__任海東__________ 姓名:趙欣佳 專業(yè):模具設計與制造 班級: 模具1204班 學號: 0102120412 設計題目: 端蓋落料拉深沖孔復合膜 工件簡圖:
2、 名稱:端蓋 材料:20號鋼 數(shù)量:大批量生產(chǎn) 要求:工件拉深精度應在IT13級以下,不宜高于IT11級。除中心孔和兩中心孔的距離尺寸接近IT11級外,其余尺寸均為自由尺寸且無其他特殊要求。 II 摘 要 隨著中國工業(yè)不斷地發(fā)展,模具行業(yè)也顯得越來越重要。本文針對端蓋的沖裁工藝性和拉深工藝性,分析比較了成形過程的三種不同沖壓工藝(單工序、復合工序和連續(xù)工序),確定用一幅復合模完成落料、拉深和沖孔的工序過程。介紹了端蓋冷沖壓成形過程,經(jīng)過對端蓋的批量生產(chǎn)、零件質(zhì)量、零件結構以及使用要求的分析、研究,按照不降低使用性能為
3、前提,將其確定為沖壓件,用沖壓方法完成零件的加工,且簡要分析了坯料形狀、尺寸,排樣、裁板方案,拉深次數(shù),沖壓工序性質(zhì)、數(shù)目和順序的確定。進行了工藝力、壓力中心、模具工作部分尺寸及公差的計算,并設計出模具。還具體分析了模具的主要零部件(如凸凹模、卸料裝置、拉深凸模、墊板、凸模固定板等)的設計與制造,沖壓設備的選用,凸凹模間隙調(diào)整和編制一個重要零件的加工工藝過程。列出了模具所需零件的詳細清單,并給出了合理的裝配圖。通過充分利用現(xiàn)代模具制造技術對傳統(tǒng)機械零件進行結構改進、優(yōu)化設計、優(yōu)化工藝方法能大幅度提高生產(chǎn)效率,這種方法對類似產(chǎn)品具有一定的借鑒作用。 關鍵詞:端蓋;模具設計;復合模;拉深沖孔
4、 主要符號表 目 錄 1 分析零件的工藝性 1 2 確定工藝方案 2 2.1 計算毛坯尺寸 2 2.2 確定是否要壓邊圈 3 2.3 計算拉深次數(shù) 3 2.4 確定工藝方案 4 3 主要工藝參數(shù)的計算 5 3.1 確定排樣、裁板方案 5 3.2 計算工藝力、初選設備 6 3.2.1 計算工藝力 6 (1)落料力 6 (2)沖孔力 7 (3)推件力 7 (4)拉深力 7 (5)壓邊力 8 3.2.2 拉深功的計算 9 3.2.3 初選壓力機 9 3.2.4
5、 計算壓力中心 10 3.2.5 計算凸、凹模刃口尺寸及公差 10 4 模具的結構設計 12 4.1 模具結構形式的選擇 12 4.1.1 模架的選用 12 4.1.2 模具的閉合高度 13 4.2 模具工作部分尺寸計算 14 4.2.1 落料凹模 15 4.2.2 拉深凸模 16 4.2.3 凸凹模 17 4.2.4 彈壓御料板 18 4.2.5 上墊板 18 4.2.6 壓邊圈 19 5 模具的整體安裝 20 5.1 模具的總裝配 20 5.2 模具零件 21 6 選定沖壓設備 22 7 模具的裝配 22 7.1 復合
6、模的裝配 22 7.2 凸、凹模間隙的調(diào)整 22 8 重要零件的加工工藝過程編制 23 結論 26 參考文獻 27 致謝 28 附錄 30 實習報告 37 1 分析零件的工藝性 沖壓件工藝性是指沖壓零件在沖壓加工過程中加工的難易程度。雖然沖壓加工工藝過程包括備料—沖壓加工工序—必要的輔助工序—質(zhì)量檢驗—組合、包裝的全過程,但分析工藝性的重點要在沖壓加工工序這一過程里。而沖壓加工工序很多,各種工
7、序中的工藝性又不盡相同。即使同一個零件,由于生產(chǎn)單位的生產(chǎn)條件、工藝裝備情況及生產(chǎn)的傳統(tǒng)習慣等不同,其工藝性的涵義也不完全一樣。這里我們重點分析零件的結構工藝性。 該零件是端蓋,如圖1.1,該零件可看成帶凸緣的筒形件,料厚t=2mm,拉深后厚度不變;零件底部圓角半徑r=1.5mm凸緣處的圓角半徑也為R=1.5mm;尺寸公差都為自由公差,滿足拉深工藝對精度等級的要求。 圖1.1 工件圖 工藝性對精度的要求是一般情況下,拉深件的尺寸
8、精度應在IT13級以下,不宜高于IT11級;對于精度要求高的拉深件,應在拉深后增加整形工序,以提高其精度,由于材料各向異性的影響,拉深件的口部或凸緣外緣一般是不整齊的,出現(xiàn)“突耳”現(xiàn)象,需要增加切邊工序。 影響拉深件工藝性的因素主要有拉深件的結構與尺寸、精度和材料。拉深工藝性對結構與尺寸的要求是拉深件因盡量簡單、對稱,并能一次拉深成形;拉深件的壁厚公差或變薄量一般不應超出拉深工藝壁厚變化規(guī)律;當零件一次拉深的變形程度過大時,為避免拉裂,需采用多次拉深,這時在保證必要的表面質(zhì)量前提下,應允許內(nèi)、外表面存在拉深過程中可能產(chǎn)生的痕跡;在保證裝配要求下,應允許拉深件側(cè)壁有一定的斜度;拉深件的徑向尺寸
9、應只標注外形尺寸或內(nèi)形尺寸,而不能同時標注內(nèi)、外形尺寸。 工藝性要求材料具有良好的塑性,屈強比值越小,一次拉深允許的極限變形程度越大,拉深的性能越好;板厚方向性系數(shù)r和板平面方向性系數(shù)反映了材料的各向異性性能,當r較大或較小時,材料寬度的變形比厚度方向的變形容易,板平面方向性能差異較小,拉深過程中材料不易變薄或拉裂,因而有利于拉深成形。 該零件結構較簡單、形狀對稱,完全由圓弧和直線組成,沒有長的懸臂和狹槽。零件尺寸除中心孔和兩中心孔的距離尺寸接近IT11級外,其余尺寸均為自由尺寸且無其他特殊要求,利用普通沖裁方法可以達到零件圖樣要求。零件材料為20號鋼,退火抗拉強度為400Mpa,屈服強度
10、為206Mpa.此材料具有良好的結構強度和塑性,其沖裁加工性較好。該零件的沖裁性較好,可以沖裁加工,適于大批大量。 2 確定工藝方案 2.1 計算毛坯尺寸 由于板料在扎壓或退火時所產(chǎn)生的聚合組織而使材料引起殘存的方向性,反映到拉深過程中,就使桶形拉深件的口部形成明顯的突耳。此外,如果板料本身的金屬結構組織不均勻、模具間隙不均勻、潤滑的不均勻等等,也都會引起沖件口高低不齊的現(xiàn)象,因此就必需在拉深厚的零件口部和外緣進行修邊處理。這樣在計算毛坯尺寸的時候就必需加上修邊余量然后再進行毛坯的展開尺寸計算。
11、 根據(jù)零件的尺寸取修邊余量的值為3.6mm。 在拉深時,雖然拉深件的各部分厚度要求發(fā)生一些變化,但如果采用適當?shù)墓に嚧胧瑒t其厚度的變化量還是并不太大。在設計工藝過程時,可以不考慮毛坯厚度的變化。同時由于金屬在塑性變形過程中保持體積不變,因而,在計算拉深件的的毛坯展開尺寸時,可以認為在變形前后的毛坯和拉深間的表面積相等。 對于該零件,可看成帶凸緣拉深件。 其相對凸緣最大直徑,3.6mm,故切邊前的凸緣直徑為: =116+23.6=123mm…………………………2.1 因 毛坯直徑: =……………………………
12、……………2.2 ==160mm 毛坯形狀如圖2.1 圖2.1 毛坯圖 2.2 確定是否需要壓邊圈 坯料相對厚度 …………………………………………2.3 所以需要壓邊圈。 2.3 計算拉深次數(shù) 在考慮拉深的變形程度時,必需保證使毛坯在變形過程中的應力既不超過材料的變形極限,同時還能充分利用材料的塑性。也就是說,對于每道拉深工序,應在毛坯側(cè)壁強度允許的條件下,采用最大的變形程度,即極限變形程度。 極限拉深系數(shù)值可以用理論計算的方法確定。即使得在傳力區(qū)的最
13、大拉應力與在危險斷面上的抗拉強度相等,便可求出最小拉深系數(shù)的理論值,此值即為極限拉深系數(shù)。但在實際生產(chǎn)過程中,極限拉深系數(shù)值一般是在一定的拉深條件下用實驗的方法得出的,我們可以通過查表來取值。 零件的總拉深系數(shù)為,其相對凸緣直徑,屬于帶大凸緣拉深的拉深件。根據(jù),,由教材<<沖壓工藝與模具設計>>上表4-16、4-18查得一次允許的拉深系數(shù),第一次拉深的最大相對高度。 因材料為20號鋼,具有良好的強度和塑性,其加工工藝性較好,可減小帶凸緣筒形件的首次拉深系數(shù)及增大最大相對高度。 使得,所以零件只需要一次拉深。 2.4 確定工藝方案 根據(jù)以上分析和計算,可以進一步明確該零件的沖壓加工需
14、要包括以下基本工序:落料、拉深、沖孔和修邊。 根據(jù)這些基本工序,可以擬出如下幾種工藝方案: 方案一 先進行落料,再拉深,修邊,最后沖孔,以上工序過程都采用單工序模加工。用此方案,模具的結構都比較簡單,制造很容易,成本低廉,但由于結構簡單定位誤差很大,而且單工序模一般無導向裝置,安裝和調(diào)整不方便,費時間,生產(chǎn)效率低。 方案二 落料與拉深、修邊在復合模中加工成半成品,再在單工序模上進行沖孔。采用了落料與拉深、修邊的復合模,提高了生產(chǎn)率。對落料以及拉深的精度也有很
15、大的提高。由于最后一道沖孔工序是在單工序模中完成,使得最后一步?jīng)_孔工序的精度降低,影響了整個零件的精度,而且中間過程序要取件,生產(chǎn)效率不高。 方案三 落料、拉深、沖孔和修邊全都在同一個復合模中一次加工成型。此方案把三個工序集中在一副復合模中完成,使得生產(chǎn)率有了很大的提升。沒有中間的取放件過程,一次沖壓成型,而且精度也比較高,能保證加工要求,在沖裁時材料處于受壓狀態(tài),零件表面平整。模具的結構也非常的緊湊,外廓尺寸比較小,但模具的結構和裝配復雜。 方案四 采用帶料級進多工位自動壓力機沖壓,可以獲得較高的生產(chǎn)效率,而且操作安全,但這一方案需要專用的壓力機或自動的
16、送料裝置。模具的結構比較復雜,制造周期長,生產(chǎn)成本高。 根據(jù)設計需要和生產(chǎn)批量,綜合考慮以上方案,方案三最適合。即落料、拉深、沖孔和修邊在同一復合模中完成,這樣既能保證大批量生產(chǎn)的高效率又能保證加工精度,而且成本不高,經(jīng)濟合理。 3 主要工藝參數(shù)的計算 3.1 確定排樣、裁板方案 加工此零件為大批大量生產(chǎn),沖壓件的材料費用約占總成本的60%~80%之多。因此,材料利用率每提高1%,則可以使沖
17、件的成本降低0.4%~0.5%。在沖壓工作中,節(jié)約金屬和減少廢料具有非常重要的意義,特別是在大批量的生產(chǎn)中,較好的確定沖件的形狀尺寸和合理的排樣的降低成本的有效措施之一。 由于材料的經(jīng)濟利用直接決定于沖壓件的制造方法和排樣方式,所以在沖壓生產(chǎn)中,可以按工件在板料上排樣的合理程度即沖制某一工件的有用面積與所用板料的總面積的百分比來作為衡量排樣合理性的指標。 同時屬于工藝廢料的搭邊對沖壓工藝也有很大的作用。通常,搭邊的作用是為了補充送料是的定位誤差,防止由于條料的寬度誤差、送料時的步距誤差以及送料歪斜誤
18、差等原因而沖出殘缺的廢品,從而確保沖件的切口表面質(zhì)量,沖制出合格的工件。同時,搭邊還使條料保持有一定的剛度,保證條料的順利行進,提高了生產(chǎn)率。搭邊值得大小要合理選取。根據(jù)此零件的尺寸通過查表取: 搭邊值為 進距方向 從視測方面來講,該零件的排樣應該采用斜排最合理。 從圖2上可知:進 距 S=128+1.5=129.5mm……………………3.1 條料寬度 b=110.3+2*2=114.3mm……………………3.2 板料規(guī)格擬用2mm1400mm4000mm熱軋鋼板。查《沖壓模具
19、設計》GB708-88,為了操作方便采用橫裁。 裁板條數(shù) 35條………………………………3.3 每條個數(shù) 11個……………………3.4 每板總個數(shù) 材料利用率 …………………………………3.5 3.2 計算工藝力、初選設備 3.2.1 計算工藝力 (1)落料力 平刃凸模落料力的計算公式為 ………………………
20、…………………3.6 式中 P— 沖裁力(N) L— 沖件的周邊長度(mm) t— 板料厚度(mm) —材料的抗沖剪強度(MPa) K— 修正系數(shù)。它與沖裁間隙、沖件形狀、沖裁速度、板料厚度、潤滑情況等多種因素有關。其影響范圍的最小值和最大值在(1.0~1.3)P的范圍內(nèi),一般k取為1.25~1.3。 在實際應用中,抗沖剪強度的值一般取材料抗拉強度的0.7~0.85。為便于估算,通常取抗沖剪強度等于該材料抗拉強度的80%。即 ……………………………
21、………………3.7 因此,該沖件的落料力的計算公式為 …………………………………………3.8 =1.3 =321984N (2)沖孔力 沖孔力可按下式計算: ……………………………………3.9 式中 —沖孔力(N) L—沖件的內(nèi)輪廓長度(mm) t—
22、板料厚度(mm) —材料的抗拉強度(MPa) 因此,該零件的沖孔力為: =0.8 =15675N (2)卸料力 一般情況下,沖裁件從板料切下以后受彈性變形及收縮影響。會使落料件梗塞在凹模內(nèi),而沖裁后剩下的板料則箍緊在凸模上。從凸模上將沖件或廢料卸下來所需的力稱卸料力。影響這個力的因素較多,主要有材料力學性能、模具間隙、材料厚度、零件形狀尺寸以及潤滑情況等。所以要精確地計算這些力是困難的,一般用下列經(jīng)驗公式計算: 卸料力
23、 ……………………………………3.10 式中 F—— 沖裁力(N) ——頂件力及卸料力系數(shù),其值可查教材表1-7。 這里取為0.04。 因此 (3)推件力 將卡在凹模中的材料逆著沖裁力方向頂出所需要的力稱為推件力。根據(jù)<<沖壓工藝與模具設計>>書上公式1-8,則推件力為: …………………………………………3.11 —推件力系數(shù),其值可查表1-7,取為0.05。 (4)拉深力 一般情況下拉深力隨凸模行程變化而改
24、變,其變化曲線如圖3.1。從圖中可以看出,在拉深開始時,由于凸緣變形區(qū)材料的變形不大,冷作硬化也小,所以雖然變形區(qū)面積較大,但材料變形抗力與變形區(qū)面積相乘所得的拉深力并不大;從初期到中期,材料冷作硬化的增長速度超過了變形區(qū)面積減少速度,拉深力逐漸增大,于前中期拉深力達到最高點位置;拉深到中期以后,變形區(qū)面積減少的速度超過了冷作硬化增加的速度,于是拉深力逐漸下降。零件拉深完以后,由于還要從凹模中推出,曲線出現(xiàn)延緩下降,這是摩擦力作用的結果,不是拉深變形力。 圖3.1 拉深力變化曲線 由于影響拉深力的因素比較復雜,按實際受力和變形情況來準確計算拉深力是筆尖困難的。所以,實際生
25、產(chǎn)中通常是以危險斷面的拉應力不超過其材料抗拉強度為依據(jù),采用經(jīng)驗公式進行計算。對于帶凸緣圓筒形零件的拉深力近似計算公式為: …………………………………………3.12 式中 —圓筒形零件的凸模直徑(mm) —系數(shù),這里取1 —材料的抗拉強度(MPa) —材料厚度 因此 (5)壓邊力 壓邊力的大小對拉深件的質(zhì)量是有一定影響的,如果過大,就要增加拉深力,因
26、而會使制件拉裂,而壓邊圈的壓力過小就會使工件的邊壁或凸緣起皺,所以壓邊圈的壓力必須適當。合適的壓邊力范圍一般應以沖件既不起皺、又使得沖件的側(cè)壁和口部不致產(chǎn)生顯著的變薄為原則。壓邊力的大小和很多因素有關,所以在實際生產(chǎn)中,可以根據(jù)近似的經(jīng)驗公式進行計算。 (N)…………………………………………3.13 式中 A—初始有效壓邊面積(mm); —單位壓邊力(MPa),這里經(jīng)查<<模具手冊>>得F=2.5 所以有 3.2.2
27、 拉深功的計算 拉深所需的功可按下式計算 …………………………………………3.14 式中 —最大拉深力(N) h —拉深深度(mm) W—拉深功(Nm) C—修正系數(shù),一般取為C=0.6~0.8。 所以 Nm…………………………3.15 3.2.3 初選壓力機 壓力機噸位的大小的選擇,首先要以沖壓工藝所需的變形力為前提。要求設備的名義壓力要大于所需的變形力,而且還要有一定的力量儲備,以防萬一。從提高設備的工作剛度、沖壓零件的精度及
28、延長設備的壽命的觀點出發(fā),要求設備容量有較大的剩余。 因,故總沖壓力 ………………………3.16 = = 應選的壓力機公稱壓力取為1.5,則公稱壓力為: ………………………………………3.17 因此初選閉式單點壓力機J31—630B。 3.2.4 計算壓力中心 本零件為對稱幾何體,其壓力中心就在它的圓心處,不必計算它的壓力中心。 3.2.5 計算凸、凹模刃口尺寸及公差 沖裁件的尺寸精度取決于凸、凹模刃口部分的尺寸。沖裁
29、間隙的合理也要靠凸、凹模刃口部分的尺寸來實現(xiàn)和保證。所以正確確定刃口部分的尺寸是相當重要的。在決定模具刃口尺寸及制造公差時,需考慮以下原則:①落料件的尺寸取決于凹模的磨損,沖裁件的尺寸取決于凸模尺寸。②考慮到?jīng)_裁時凸、凹模的磨損,在設計凸、凹模刃口尺寸時,對基準件刃口尺寸在磨損后變大的,其刃口公稱尺寸應取工件尺寸范圍內(nèi)較小的數(shù)值。對基準件刃口尺寸在磨損后減少的,其刃口公稱尺寸應取工件尺寸范圍內(nèi)較大的數(shù)值。這樣,在凸模磨損到一定程度的情況下,任能沖出合格的零件。③在確定模具刃口制造公差時,要既能保證工件的精度要求,又要保證合理的間隙數(shù)值。 采用凸凹模分別加工,凸凹模分別加工是指在凸模與凹模
30、分別按各自圖樣上標注的尺寸及公差進行加工,沖裁間隙由凸凹模刃口尺寸及公差保證,這樣就需要分別計算出凸模和凹模的刃口尺寸及公差,并標注在凸凹模設計圖樣上,這樣加工方法具有互換性,便于成批制造,主要用于簡單,規(guī)范形狀(圖形,方法或矩形)的沖件。 ①落料時,因為落料件表面尺寸與凹模刃口尺寸相等或基本一致,應該先確定凹模刃口尺寸,即以凹模刃口尺寸為基準,又因為落料件尺寸會隨凹模刃口的磨損而增大,為了保證凹模磨損到一定程度仍能沖出合格零件,故凹模基本尺寸應該取落料件尺寸公差范圍內(nèi)的較小尺寸,落料凸模的基本尺寸則是凹?;境叽缟蠝p去最小合理間隙。 ………………………………3.18
31、 ……………………………3.19 式中 —落料凸模最大直徑(mm) —落料凹模最大直徑(mm) D —工件允許最大尺寸(mm) — 沖裁工件要求的公差 X —系數(shù),為避免多數(shù)沖裁件尺寸都偏向于極限尺寸,此處可取X=0.5。 對于未標注公差可按IT14級計算,根據(jù)教材上表1-3查得,沖裁模刃口雙面間隙: 、—凹、凸模制造偏差,這里可以按IT7來選取: 落料刃口最大尺寸計算 凸模制造公差按IT8級精度選取,得落料尺寸,查表
32、得 校核間隙:||+||條件,但相差不大,可作如下調(diào)整: = 則 = =159.5 =
33、 =159.88 ②拉深時,拉深模直徑尺寸的確定的原則,與沖裁模刃口尺寸的確定基本相同,只是具體內(nèi)容不同,這里不在復述。 拉深凸模和凹模的單邊間隙Z=1.1t=2.2mm計算凸凹模制造公差,按IT8級精度選取,由附錄表4查得,對于拉深尺寸,。 因拉深件注內(nèi)形尺寸,按凸模進行配作: …………………………………3.19 式中 d—拉深件內(nèi)形尺寸: d—凸模尺寸: —拉深件公差,這里按IT14級精度選取,查表附錄4
34、,可以 得=1: 即有 =68.5 拉深凹模則注凸模的基本尺寸,并要求按單面拉深間隙配作: ③沖孔時,對于沖孔孔,,按IT14級精度選取,查附表4得:校核間隙:||+||=,滿足條件,故可以采用凸模與凹模配合加工方法,因數(shù)由表2-21查得,,則為:
35、 4 模具的結構設計 4.1 模具結構形式的選擇 4.1.1 模架的選用 采用落料、拉深、沖孔復合模,首先要考慮落料凸模(兼拉深凹模)的壁厚是否過薄。本次設計中凸凹模的最小壁厚為,滿足鋼材最小壁厚的要求能夠保證足夠的強度,故采用復合模。 模具采用倒裝式。模座下的緩沖器兼作壓邊與頂件,另外還設有彈性卸料裝置的彈性頂件裝置。這種結構的優(yōu)點是操作方便,出件暢通無阻,生產(chǎn)效率高,缺點是彈性卸料板使模具的結構變復雜,要簡化可以采用剛性卸料板,其缺點是拉深件留在剛性卸料板中不易取出,帶來操作上的不便,結合本次設計綜合考慮,采用彈性卸料板。 從生產(chǎn)量和方
36、便操作以及具體規(guī)格方面考慮,選擇后則導柱模架,由凹模外形尺寸,(GB/T2851.5—1990)在按其標準選擇具體結構尺寸如下 上模板 HT250 下模板 ZG450 導 柱 20鋼 導 套 20鋼 凸緣模柄 Q235 模具閉合高度 MAX 245mm MIN 200mm 4.1.2 模具的閉合高度 所謂的模具的
37、閉合高度H是指模具在最低工作位置時,上下模座之間的距離,它應與壓力機的裝模高度相適應。 模具的實際閉合高度,一般為: ……………4.1 該副模具使用上墊板厚度為10mm,凹模固定板厚度為12mm。如果沖頭(凸凹模)的長度設計為110mm,凹模(落料凹模)設計為70mm,則閉合高度為: 4.2 模具工作部分尺寸計算 4.2.1 落料凹模 落料凹模采用矩形板結構和直接通過螺釘、銷釘與下模座固定的固定方式。因生產(chǎn)的批量大,考慮凹模的磨損和保證零件的質(zhì)量,凹模刃口采用直刃壁結構,刃壁高度,漏料部分沿刃口輪廓適當擴大(為便于加工,落料凹模漏料孔可設計成近似于刃
38、口輪廓的形狀,如凹模圖)。凹模輪廓尺寸計算如下: 凹模厚度 凹模壁厚 沿送料方向的凹模長度為 根據(jù)算得的凹模輪廓尺寸,選取與計算值相近的凹模板,其尺寸為。 凹模的材料選用,工作部分熱處理淬硬。 圖4.1 落料凹模 4.2.2 拉深凸模 拉深凸模刃口部分為非圓形,為便于凸模和固定板的加工,可設計成階梯形結構,并將安裝部分設計成便于加工的長圓形,通過螺釘緊固在固定板上,用銷釘定位。凸模的尺寸根據(jù)刃口尺寸、卸料裝置和安裝固定要求確定。凸模的材料選用T8A,工作部
39、分熱處理淬硬。 對于拉深凸模的工作深度,必須從幾何形狀上做的正確。為了使零件容易在拉深后被脫下,在凸模的工作深度可以作成一定錐度 為了防止拉深件被凹模內(nèi)壓縮空氣頂癟及拉深件與凸模之間發(fā)生真空現(xiàn)象而緊箍在凸模上,故在凸模上設計通氣孔,以使拉深后容易從凸模上取下。根據(jù)凸模尺寸取出氣孔直徑,數(shù)量為2個。如圖4.2 圖4.2 拉深凸模 4.2.3 凸凹模 該復合模中的凸凹模是主要工作零件,其外形作為落料凸模內(nèi)形又作為拉深凹模,并且內(nèi)、外形刃口部分都為非圓形,為便于凸凹模與凸模固定板的配合,凸凹模的安裝部分設計成便于加工的長圓形,通過螺釘緊固在凸模固定板上,并用銷釘定位。如圖4.
40、3 凸凹模的自由長度為:L=凸模固定板厚度+橡膠安裝高度+卸料板厚度+材料厚度+凸凹模工作高度=22+26+20+2+(42-2)=110mm?!?.2 圖4.3 凸凹模 4.2.4 彈壓御料板 彈性卸料板的尺寸可以根據(jù)彈性元件的數(shù)目以及外徑來計算。如圖4.4。 由于受到橡膠允許承受的載荷較大,安裝,調(diào)整,靈活,方便,因而是沖裁模中常用的彈性元件,沖裁模中用于卸料的橡膠有合成橡膠和聚氨脂橡膠,其中聚氨脂的性能比合成橡膠優(yōu)異,是常用的卸料彈性元件。 為了保證卸料正常工作,應該使橡膠的預緊的
41、預壓力: ……………………………………4.3 橡膠的壓力與壓縮量之間不是線形關系,橡膠的壓縮時產(chǎn)生的壓力按下式計算: ………………………………………4.4 式中 A——橡膠的橫截面積 P——橡膠與單位壓邊力,其值與橡膠的壓縮量,形狀及尺寸有關 計算橡膠的自由高度,由下式 ~4) ………………………………
42、…………4.5 計算橡膠的裝配高度,由下式 ………………………………………………4.6 ~ …………………………………… 4.7 按公式計算得:
43、 圖4.4 彈性卸料板 4.2.5 上墊板 墊板的作用是直接承受和擴散凸模傳遞的壓力,以降低模座所受的單位壓力,防止模座被壓出陷痕而損壞。在設計中我們把墊板的外形尺寸與凸凹模的外形尺寸相匹配,其厚度我們設計為10mm。在上墊板上設計了一個推桿孔,以便安裝推桿,還有四個螺釘孔以及兩個銷孔,這些都是為了與凸凹模和拉深凸模上的各種固定零件的安裝相匹配的。在圖中標注尺寸精度、形位公差及粗糙度。上墊板的零件圖如圖4.5所示。 圖4.5上墊板 4.2.6 壓邊圈 在這個設計中,壓邊圈
44、借助頂桿所施的頂件力,既起到壓邊的效果,又起來把拉深件頂出拉深凸模,設計高度為15mm,如圖4.6 圖4.6壓邊圈 5 模具的整體安裝 5.1 模具的總裝配 由以上的設計計算,并經(jīng)繪圖設計,該端蓋落料、拉深、沖孔復合模裝配圖如圖5.1所示。 圖5.1總體裝配圖 5.2 模具零件 該復合模的主要零部件在模具的結構設計中已經(jīng)進行了仔細的設計,其余的非標準的零件可以根據(jù)需要按國標選取使用。所有零件的明細表見表5.1。 表5.1 落料、拉深、沖孔復合模零件表 件號 名 稱 數(shù)量 材 料 規(guī) 格(㎜) 標 準 熱 處 理
45、 1 圓柱銷 2 12x60 GB/T119.1-2000 2 上墊板 1 45 250x200x10 43~48HRC 3 推 板 1 40 厚度10mm 40~45HRC 4 凸緣模柄 1 Q235 70x100 JB/T7646.3-1994 5 打 桿 1 40 15x135 43~48HRC 6 推 桿 3 40 6x85 43~48HRC 7 卸料螺釘 4 M12x105 GB2867.6-81 8 壓邊圈 1 45 厚度15mm 48~52HRC
46、9 螺 釘 4 M10x20 GB/T70.1-2000 10 導套 1 20 28x100x42 滲碳58~62HRC 11 導柱 1 20 28x195 滲碳58~62HRC 12 落料凹模 1 CrWMn 高70mm 58~62HRC 13 凹模固定板 1 45 250 x200x12 43
47、~48HRC 14 圓柱銷 2 12x100 GB/T119.1-2000 15 推件塊 1 45 10x69 48~52HRC 16 頂 桿 2 6x100 JB/T7650.3-1994 43~48HRC 16 沖孔凸模 2 Cr12 13x30 58~62HRC 17 螺 釘 5 M12x70 GB/T70.1-2000 18 凸凹模固定板 1 45 250x200x22 43~48HRC 19 擋料銷 3 45 16x13 JB/T7649.10-1994 43~48HRC
48、 6 選定沖壓設備 沖壓設備選擇是沖壓工藝過程設計的一項重要內(nèi)容,它直接關系到設備的安全和使用的合理,同時也關系到?jīng)_壓工藝過程的順利完成及產(chǎn)品質(zhì)量、零件精度、生產(chǎn)效率、模具壽命、板料的性能與規(guī)格、成本的高低等一系列重要問題。 在前面的設計中,我們已經(jīng)對沖壓設備的噸位以及閉合高度等參數(shù)進行了確定。這里根據(jù)前面所算出來的各項數(shù)據(jù)。查表選擇壓力機,確定選用閉式單點壓力機J31-630B,其主要具體參數(shù)如下: 公稱壓力 1000KN 滑塊行程 120mm 封閉高度調(diào)節(jié)量 110mm 工作臺尺寸
49、 600460mm 柄孔尺寸 6075mm 立柱間距離 420mm 工作臺板厚 110mm 7 模具的裝配 7.1 復合模的裝配 復合模一般以凸凹模作為裝配基件。其裝配順序為:①裝配模架,導套與上模座采用配合,導柱與下模座采用基軸制配合;②裝配凸凹模組件(凸凹模及其固定板)和凸模組件(凸模及其固定板);③將凸凹模組件用螺釘和銷釘安裝固定在指定模座(正裝式復合模為上模座,倒裝式復合模為下模座)的相應位置上;④以凸凹模為基準,將凸模組件及凹模初步固定在另一模座上,調(diào)整凸模組件及凹模的位置,使凸模刃口和凹模刃口分別與
50、凸凹模的內(nèi)、外刃口配合,并保證配合間隙均勻后固緊凸模組件與凹模;⑤試沖檢查合格后,將凸模組件、凹模和相應模座一起鉆鉸銷孔;⑥卸開上、下模,安裝相應的定位、卸料、推件或頂出零件,再重新組裝上、下模,并用螺釘和定位銷緊固。 7.2 凸、凹模間隙的調(diào)整 沖模中凸、凹模之間的間隙大小及其均勻程度是直接影響沖件質(zhì)量和模具使用壽命的主要因素之一,因此,在制造沖模時,必須要保證凸、凹模間隙的大小及均勻一致性。通常,凸、凹模間隙的大小是根據(jù)設計要求在凸、凹模加工時保證,而凸、凹模之間間隙的均勻性則是在模具裝配時保證的。 沖模裝配時調(diào)整凸、凹模間隙的方法很多,需根據(jù)沖模的結構特點、間隙值的大小和裝配
51、條件來確定。這里用墊片法來調(diào)整。 墊片法是利用厚度與凸、凹模單面間隙相等的墊片來調(diào)整間隙,是簡便而常用的一種方法。其方法如下: ①按圖樣要求組裝上模與下模,其中一般上模只用螺釘稍微擰緊,下模用螺釘和銷釘緊固。 ②在凹模刃口四周墊入厚薄均勻、厚度等于凸、凹模單面間隙的墊片(金屬片或紙片),再將上、下模合模,使凸模進入響應的凹??變?nèi),并用等高墊鐵墊起。 ③觀察凸模能否順利進入凹模,并與墊片能否有良好的接觸。若在某方向上與墊片接觸的松緊程度相差較大,表明間隙不均勻,這時可用手錘輕輕敲打凸模固定板,使之調(diào)整到凸模在各方向與凹??變?nèi)碘片的松緊程度一致為止。 ④調(diào)整合適后,在將上模用螺釘緊固,并
52、配裝銷釘孔,打入定位銷。 8 重要零件的加工工藝過程編制 在機械制造中,采用各種機械加工方法將毛坯加工成零件,再將這些零件裝配成機器。為了使上述制造過程滿足“優(yōu)質(zhì)、高產(chǎn)、低成本”的要求,首先要指定零件的機械加工工藝規(guī)程和機器的裝配工藝規(guī)程,然后按照所制訂的工藝規(guī)程來進行機械加工和裝配。由于零件的工藝過程可以是多種多樣的,工藝人員的任務是從現(xiàn)有生產(chǎn)條件出發(fā),制訂出一個切合實際的最優(yōu)工藝過程,并將其有關內(nèi)容用文件的形式規(guī)定下來。規(guī)定零件機械加工工藝過程和操作方法等的工藝文件稱為機械加工工藝規(guī)程。 機械加工工藝規(guī)程是指導生產(chǎn)的主要技術文件。按照工藝規(guī)程進行生產(chǎn),才能保證達到產(chǎn)
53、品質(zhì)量、生產(chǎn)率和經(jīng)濟性的要求。合理的工藝規(guī)程在編制后應要滿足下述要求: 1.零件所需的工序數(shù)量要盡量少,并且要減少或不再采用其他加工方法加工。 2.零件各工序所采用的設備結構要簡單、壽命要長。 3.工序中所占用的設備要少,盡可能采用生產(chǎn)機械化與自動化。 4.生產(chǎn)準備周期要短,所需材料要少,成本要低廉。 5.零件的生產(chǎn)工藝流程要合理,做到安全生產(chǎn)。 6.制出的零件應符合技術要求,并且尺寸精度要高,表面質(zhì)量要好。 7.盡量采用技術等級不高的工人生產(chǎn),以降低成本。 制訂機械加工工藝規(guī)程的原則是:在一定的生產(chǎn)條件下,以最低的成本,按計劃規(guī)定的速度,可靠地加工出圖紙要求的零件。在編制工藝
54、規(guī)程時,應注意以下幾個問題: 1.技術上的先進性 在編制工藝規(guī)程時,應盡量采用新工藝、新技術、先進設備和新材料,以獲得較高的生產(chǎn)率,但不應加大操作工人的勞動強度,而應依靠設備的先進性來保證。 2.經(jīng)濟上的合理性 在一定的生產(chǎn)條件下,可能有幾種能保證零件技術要求的加工工藝方案,此時應全面考慮,應根據(jù)工序數(shù)量、機械加工難易程度、通過核算或分析選擇經(jīng)濟效益最佳的加工方案,以使零件減少工序及降低成本。同時,加工精度要求不高的零件,盡量不使用高精度的加工設備。 3.創(chuàng)造必要的良好工作條件 在編制工藝規(guī)程時,必須保證操作人員有良好而安全的工作條件,并保證所加工的零件的質(zhì)量合格及
55、減輕工人的勞動強度。 本模具選用導套來編制其加工工藝過程。導套在模具中起定位和導向作用,保證凸、凹模工作時具有正確的相對位置。為了保證良好的導向,導套在裝配后應保證模架的活動部分移動平穩(wěn)。所以,在加工過程中除了保證導套配合表面的尺寸和形狀精度外,還應保證導套各配合面之間的同軸度要求。為了提高導套的耐磨性并保持較好的韌性,導套一般選用低碳鋼(20鋼)進行滲碳、淬火處理, 導套的基本表面是旋轉(zhuǎn)體圓柱體,因此導套的主要加工方法是車削和磨削,對于配合精度要求高的部位,配合表面還要進行研磨。為了保證導套的形狀和位置精度,加工時,粗加工一般采用一次裝夾同時加工外圓和內(nèi)孔,精加工采用互為基準的方法來保證
56、內(nèi)孔和外圓的同軸要求。 導套的加工工藝過程見表8。 導套加工應達到的要求見圖8。 圖8 導套 表8 加工工藝過程表 工 序 號 工序名稱 工序內(nèi)容 設備 工序簡圖(示意圖) 1 下料 按尺寸切斷 鋸床 2 車外圓 及內(nèi)孔 車端面保持長度103mm 鉆的孔至 車的外圓至 倒角 切的槽至尺寸 鏜的孔至 鏜油槽 鏜的孔至尺寸 倒角 車床 3 車外圓 倒角 車的外圓至尺寸 車端面保持長度100mm 倒內(nèi)外
57、圓角 車床 4 檢驗 5 熱處理 按熱處理工藝進行,保證滲 碳層深度,硬度 6 磨內(nèi)外圓 磨外圓達圖樣要求 磨內(nèi)孔,留研磨量 萬能 外圓 磨床 7 研磨內(nèi)孔 研磨的孔達圖樣要求 研磨R2mm的內(nèi)圓孔 車床 8 檢驗 31 結 論 本次設計成功地設計出一副落料、拉深、沖孔復合模,在設計過程中對很多工藝力進行了詳細的計算,在壓力機的選擇上參照了現(xiàn)行選擇壓力機的通用法則。這次設計解決了采用雙動壓力機進行沖孔、拉深、落料的傳統(tǒng)模式,將落料、拉深及沖孔同時在一副裝在閉式單動壓力
58、機上的模具中完成,很大程度的提高了生產(chǎn)效率和制造精度。很適合中國現(xiàn)在模具高速自動化發(fā)展的趨勢。 參考文獻 [1]劉心冶. 冷沖壓工藝及模具設計[M]. 重慶:重慶大學出版社,1998 Liu Xinye.Cold stamping technique and Die design[M].Chongqing:Chongqing University Press,1998(in Chinese) [2]盧險峰. 沖壓工藝模具學[M]. 北京:機械工業(yè)出版社,2000
59、 Lu Xianfeng.Stamping technique and die learning[M].Beijing:Machine Industry Press,2000(in Chinese) [3]梁柄文. 實用板金沖壓工藝圖集[M]. 北京:機械工業(yè)出版社,1999 Liang Bingwen.Utility plate stamping technique album[M]. Beijing:Machine Industry Press,1999(in Chinese) [4]模具實用技術叢書編委會. 沖模設計應用實例[M]. 北京:機械工業(yè)出版社,2002
60、 Die utility technology series newsroom.Stamping die design apply example[M]. Beijing:Machine Industry Press,2002(in Chinese) [5]杜東福. 冷沖壓工藝及模具設計[M]. 長沙:湖南科學技術出版社,1990 Du Dongfu.Cold stamping technique and Die design[M].Changsha:Hunan Science Technology Press.1990(in Chinese) [6]成虹. 沖壓工藝與模具設計[M
61、]. 成都:電子科技大學出版社,2000 Cheng Hong.Stamping technique and Die disian [M].Chengdu:Electron Technology Uninersity Press, 2000(in Chinese) [7]馮柄堯. 模具設計與制造簡明手冊[M]. 上海:上??茖W技術出版社,1998 Feng Bingyao.Die design and produce simplicity handbook[M].Shanghai:Shanghai Science Technology Press,1998(in Chines
62、e) [8]王樹勛,高廣升. 冷沖壓模具結構圖冊大全[M]. 廣州:華南理工大學出版社,1988 Wang Shuxun,Gao Guangsheng.Cold stamping die fabric album overall[M].Guangzhou: Huanan Science University Press, 1988(in Chinese) [9]鄭家賢. 沖壓工藝模具設計實用技術[M]. 北京:機械工業(yè)出版社,1999 Zheng Jiaxian.Stamping technique die design utility technology[M]. Beijing:Machine Industry Press,1999(in Chinese)
- 溫馨提示:
1: 本站所有資源如無特殊說明,都需要本地電腦安裝OFFICE2007和PDF閱讀器。圖紙軟件為CAD,CAXA,PROE,UG,SolidWorks等.壓縮文件請下載最新的WinRAR軟件解壓。
2: 本站的文檔不包含任何第三方提供的附件圖紙等,如果需要附件,請聯(lián)系上傳者。文件的所有權益歸上傳用戶所有。
3.本站RAR壓縮包中若帶圖紙,網(wǎng)頁內(nèi)容里面會有圖紙預覽,若沒有圖紙預覽就沒有圖紙。
4. 未經(jīng)權益所有人同意不得將文件中的內(nèi)容挪作商業(yè)或盈利用途。
5. 裝配圖網(wǎng)僅提供信息存儲空間,僅對用戶上傳內(nèi)容的表現(xiàn)方式做保護處理,對用戶上傳分享的文檔內(nèi)容本身不做任何修改或編輯,并不能對任何下載內(nèi)容負責。
6. 下載文件中如有侵權或不適當內(nèi)容,請與我們聯(lián)系,我們立即糾正。
7. 本站不保證下載資源的準確性、安全性和完整性, 同時也不承擔用戶因使用這些下載資源對自己和他人造成任何形式的傷害或損失。