自動切管機結構設計
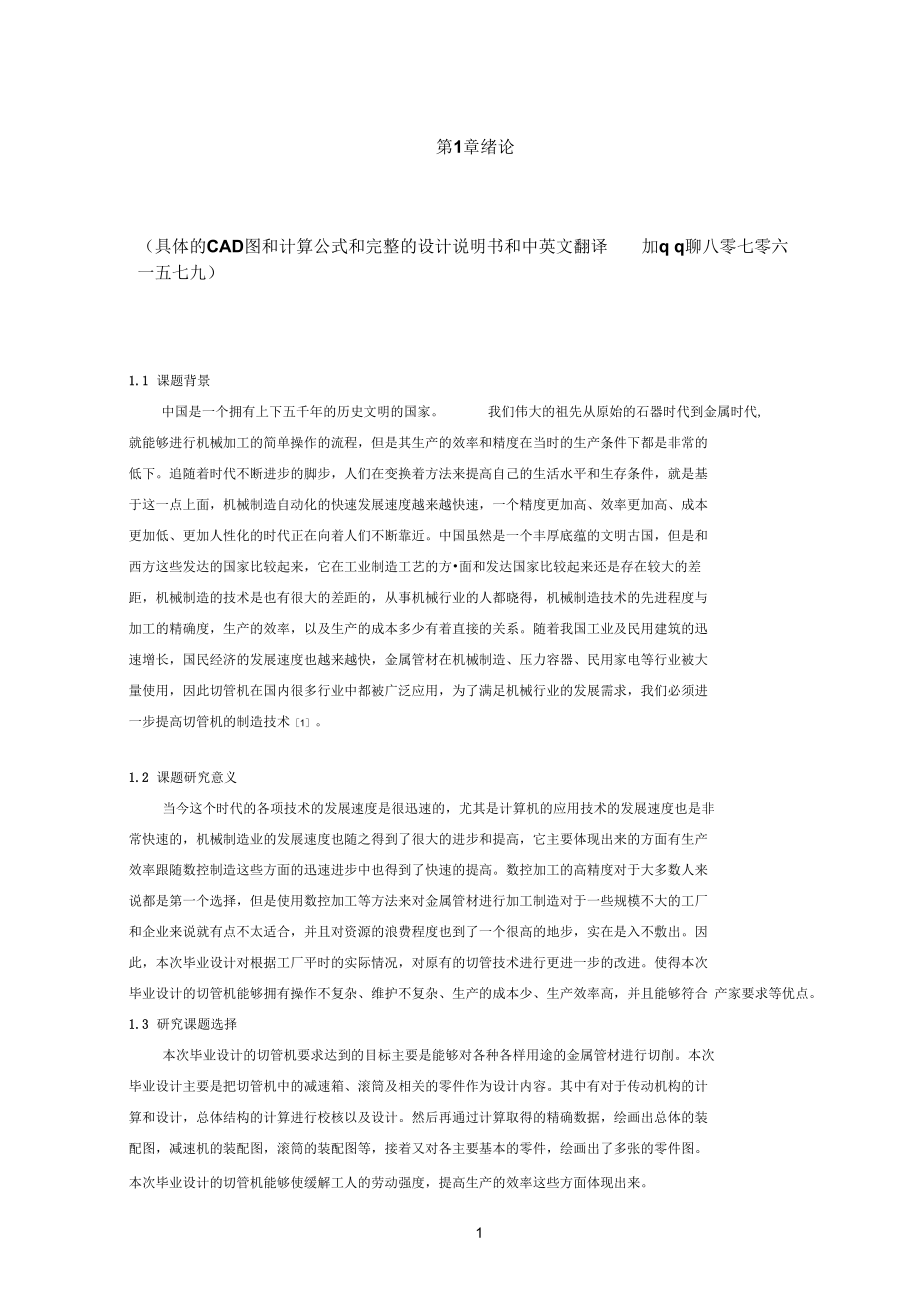


《自動切管機結構設計》由會員分享,可在線閱讀,更多相關《自動切管機結構設計(31頁珍藏版)》請在裝配圖網(wǎng)上搜索。
1、第1章緒論 (具體的CAD圖和計算公式和完整的設計說明書和中英文翻譯 加q q聊八零七零六 一五七九) 1.1 課題背景 中國是一個擁有上下五千年的歷史文明的國家。 我們偉大的祖先從原始的石器時代到金屬時代, 就能夠進行機械加工的簡單操作的流程,但是其生產(chǎn)的效率和精度在當時的生產(chǎn)條件下都是非常的 低下。追隨著時代不斷進步的腳步,人們在變換著方法來提高自己的生活水平和生存條件,就是基 于這一點上面,機械制造自動化的快速發(fā)展速度越來越快速,一個精度更加高、效率更加高、成本 更加低、更加人性化的時代正在向著人們不斷靠近。中國雖然是一個豐厚底蘊的文明古國,但是和 西方這些發(fā)達的國家比較起來,
2、它在工業(yè)制造工藝的方?面和發(fā)達國家比較起來還是存在較大的差 距,機械制造的技術是也有很大的差距的,從事機械行業(yè)的人都曉得,機械制造技術的先進程度與 加工的精確度,生產(chǎn)的效率,以及生產(chǎn)的成本多少有著直接的關系。隨著我國工業(yè)及民用建筑的迅 速增長,國民經(jīng)濟的發(fā)展速度也越來越快,金屬管材在機械制造、壓力容器、民用家電等行業(yè)被大 量使用,因此切管機在國內(nèi)很多行業(yè)中都被廣泛應用,為了滿足機械行業(yè)的發(fā)展需求,我們必須進 一步提高切管機的制造技術[1]。 1.2 課題研究意義 當今這個時代的各項技術的發(fā)展速度是很迅速的,尤其是計算機的應用技術的發(fā)展速度也是非 ??焖俚模瑱C械制造業(yè)的發(fā)展速度也隨之得到了很
3、大的進步和提高,它主要體現(xiàn)出來的方面有生產(chǎn) 效率跟隨數(shù)控制造這些方面的迅速進步中也得到了快速的提高。數(shù)控加工的高精度對于大多數(shù)人來 說都是第一個選擇,但是使用數(shù)控加工等方法來對金屬管材進行加工制造對于一些規(guī)模不大的工廠 和企業(yè)來說就有點不太適合,并且對資源的浪費程度也到了一個很高的地步,實在是入不敷出。因 此,本次畢業(yè)設計對根據(jù)工廠平時的實際情況,對原有的切管技術進行更進一步的改進。使得本次 畢業(yè)設計的切管機能夠擁有操作不復雜、維護不復雜、生產(chǎn)的成本少、生產(chǎn)效率高,并且能夠符合 產(chǎn)家要求等優(yōu)點。 1.3 研究課題選擇 本次畢業(yè)設計的切管機要求達到的目標主要是能夠對各種各樣用途的金屬管材進行
4、切削。本次 畢業(yè)設計主要是把切管機中的減速箱、滾筒及相關的零件作為設計內(nèi)容。其中有對于傳動機構的計 算和設計,總體結構的計算進行校核以及設計。然后再通過計算取得的精確數(shù)據(jù),繪畫出總體的裝 配圖,減速機的裝配圖,滾筒的裝配圖等,接著又對各主要基本的零件,繪畫出了多張的零件圖。 本次畢業(yè)設計的切管機能夠使緩解工人的勞動強度,提高生產(chǎn)的效率這些方面體現(xiàn)出來。 1.4 現(xiàn)狀以及發(fā)展的道路 世界不是一層不變的,它總是在無時無刻的變化著,每天都擁有新的景象。切管機這個行業(yè)在 國內(nèi)業(yè)也不會排除,很多需要切管機的廠商們都對這個行業(yè)的發(fā)展趨勢產(chǎn)生普遍的關注。 現(xiàn)如今,日本能夠在這個領域靠切管機技術獲取了
5、大量的利潤,就是因為卷筒紙分切機、紙管 機設備、切管機的更新發(fā)展速度能夠遙遙領先,追隨者日本的腳步,東南亞四小龍也迅速發(fā)展了起 來,在生產(chǎn)線的制造和包裝機械設備的方面有能夠有符合社會需求的新技術,在歐共體中,意大利 的生產(chǎn)線更新?lián)Q代和包裝機械設備的步伐遠遠比其它的國家來得快速。從上面的種種現(xiàn)象看出來更 新就是關鍵! 更新?lián)Q代的方式是采取更換局部零部件或關鍵性部件和關鍵性技術,從而達到更換一臺機組設 備的目標,那么更新原包裝機械裝備或生產(chǎn)線的生產(chǎn)能力也能也能迅速提高。這樣的做法就能夠使 得大部分零部件、機組的零件獲得循環(huán)的使用,既能夠把設備的原有價值大幅度提高,而且又大幅 度減少了成本的需求,
6、使得原材料和所需要的勞動力達到了節(jié)省這個目標。 這種發(fā)展的勁頭能夠體現(xiàn)出切管機設備越來越向標準化、組裝化、系列化、聯(lián)機化、綜合化的 標準進步。整個包裝機械設備的領域也慢慢地融入了民用、軍用的高技術。切管機設備也能夠在越 來越激烈的市場競爭中加快更新?lián)Q代和技術改進的步伐 [2]。 1.5 本章小結 隨著我國工業(yè)及民用建筑迅速增長,國民經(jīng)濟的發(fā)展速度日益增快,管材在機械制造、壓力容 器、民用家電等行業(yè)被大量使用,因此切管機在國內(nèi)很多行業(yè)中都被廣泛得應用,為了滿足機械行 業(yè)元越來越快的發(fā)展需求,我們必須要進一步提高切管機的制造技術,積極創(chuàng)新,跟上時代發(fā)展的 腳步。本章重點闡述了關于我國現(xiàn)有切管
7、機的真實情況以及本次畢業(yè)設計的研究方向和設計意義, 而且從多種的相同角度說明了本次畢業(yè)設計的新穎獨到之處,從目前實際生產(chǎn)運用的情況中可以看 到,切管機良莠不齊,而且都存在著不少問題,比如: 1..結構比較復雜;2.可以切割管材直徑范圍 比較??;3.振動比較大、定位不準確、精度比較低;4.刀具耐用度低、自動化程度低;5價格比較高。 本次畢業(yè)設計的切管機主要是能夠對各種各樣的用途的金屬管材進行切割。本次畢業(yè)設計的內(nèi)容主 要是對切管機中的減速箱、滾筒及相關的零件進行的設計。其中有對于傳動機構的計算和設計,總 體結構的計算進行校核以及設計。然后再通過計算過取得的精確數(shù)據(jù),繪畫出總體的裝配圖,減速 機
8、的裝配圖,滾筒的裝配圖等,接著又對各主要基本的零件,繪畫出了多張的零件圖。使得本次畢 業(yè)設計的切管機能夠擁有操作不復雜、維護不復雜、生產(chǎn)的成本少、生產(chǎn)效率和能夠符合產(chǎn)家要求 等優(yōu)點。 第2章確定設計方案 2.1 設計要求 設計過程中的要求: 1、切管機結構要符合實際; 2、載荷變動小 3、操作時要確保安全; 4、優(yōu)化設計要用合理的方法。 2.2 切管機的工作參數(shù) 滾子轉速:n=70r/min 圓盤刀片直徑:a=80mm 加工管件的直徑為:3/8 -4" 電機額定功率:i為P=1.5Kw 滿載的轉速為: N=1410r/min 每天工作:10小時 2.3 切管機的設
9、計方案的確定 本次畢業(yè)設計的任務是設計一款操作簡單以及生產(chǎn)高效的切管機,因此針對以下的幾種提出的 設計方案進行比較: 萬案一: 鋸弓鋸斷金屬管:鋸弓往復的切削運動和滑枕的擺動進給與讓刀的運動來進行實現(xiàn)。機器的構 造會比較復雜和鋸切運動不是連續(xù)不斷是缺點。如果在加工過程中金屬管的直徑有較大的相差時, 還得更換鋸片,由此可見生產(chǎn)效率不是很高。 萬案一: 切斷刀切割金屬管:比如在車床上對管子進行切割,但是車床主軸一般不超過幾十毫米,直徑 較大的金屬管通不過去,并且一臺普通機床對費用有點耗費。要是使用專門的切管機;它的工作原 理是夾緊工件不動,安裝在轉換的刀架上的兩把切割刀,既有進給運動,
10、又有主切割的旋轉運動, 工作效率高,但是機床的構造會比較繁雜。 方案二: 砂輪切割金屬管:砂輪旋轉的切削運動和搖臂向下的進給運動來實現(xiàn)切割金屬管。這種機構的 構造不復雜,生產(chǎn)效率高,可是砂輪的磨損對費用要求有點高。 方案四: 碾壓的方法切割金屬管:金屬管旋轉的切削運動和圓盤向下的進給運動來進行實現(xiàn)。這種方法 實現(xiàn)了連續(xù)切割,生產(chǎn)效率高,機器的構造也不是很復雜。可是切割時會使管子的切口內(nèi)徑縮短, 一般使用的場合是用于管子要求不高的。 根據(jù)工作參數(shù)和結合生產(chǎn)實際,最終確定在本次設計中選用方案四。 本次確定的方案的工作原理:切管機有相應的一個柜式工作臺,臺面下柜內(nèi)吊裝電動機和減速 箱,臺
11、面上安裝一對滾筒。按下開關后,動力的傳動是由電動機-帶輪-蝸桿-蝸輪-直齒輪-中 間惰輪-滾子軸上小齒輪。由于滾子的旋轉運動,動力傳給滾筒,使二滾筒同向旋轉,從而帶動鋼 管的旋轉,實現(xiàn)切削時的主運動。單臂式的支架裝在滾筒的背后,有一組活動的螺桿套筒(即螺旋 傳動機構)裝在支架上,切割用的圓盤刀片就裝在套筒的下方。當轉動手輪,螺母就會把刀片和套 筒往下壓,直到切斷鋼管。 1 -機柜2-開關3-減速箱4-電動機5-帶輪6-蝸桿7-渦輪 8-滾子軸9-滾筒10-管子11-刀片12-刀架13-手輪 圖2-1切管機機構示意圖 31 第3章傳動機構的設計與計算 3.1 電動機的選擇 對電
12、動機了解清楚才能選擇電動機。出廠的電動機上面都會有銘牌,電動機的主要技術參數(shù)都 在銘牌上。所以,選擇電動機需要比較電動機的這些特性,在這次的畢業(yè)設計中必須要選擇好電動 機的類型,轉速和功率 。 3.1.1 選擇類型 選用結構簡單,工作可靠,價格便宜,維護方便等優(yōu)點的三相交流異步電動機是工業(yè)上普遍的 選擇。靜載荷或慣性載荷的大在電動機的類型的選擇時是主要考慮的方面, 切管機不論是連續(xù)工作, 還是重復短時的工作,工作所在的環(huán)境都會有很多灰塵等方面。因此在本次畢業(yè)設計中選用籠式三 相交流異步電機。 3.1.2 選擇轉速 異步電機的轉速主要有 3000r/min、1500r/min、10
13、00r/min、750r/min幾種。選擇同步轉速為 3000r/min的電機比較適合工作時的轉速較高的場合。 當工作機械的轉速太低 (即傳動結構的總傳動 比較大)會導致傳動裝置的機構比較復雜,價格偏高。在本次畢業(yè)設計的切管機可選擇 1500r/min 和750r/min這兩種轉速。在一般工業(yè)中這兩種轉速的電動機的適應性比較大,應用性比較普遍 [3]。 3.1.3 選擇功率 合理確定電動機的額定功率必須要選擇電動機的容量,電動機功率的選擇與電動機的本身發(fā)熱 量、工作時間長短、載荷大小等因素有關,可是一般情況下運行發(fā)熱條件決定電動機的容量。所以 根據(jù)電動機的額定功率要大于所需要的功
14、率 10%來選用電動機。 本次畢業(yè)設計的切管機的電動機的額定功率為 P= 1.5Kw ,滿載轉速為N= 1410r/min,每天工作的 時間為10小時,載荷變動小適合用在灰塵多的環(huán)境。所以選用 Y90L-4型的電動機,它的額定功率 p電=1.5kw ,同步轉速1500r/min (4極),滿載轉速 n電=1400r/min ,最大轉矩是 2.3N m。 計算切管機的傳動比為: 1400 70 3.2 確定傳動方案 傳動方案的確定,通常是指傳動機構的選擇及其布置。這是緊密關聯(lián)的兩個方面。它的運動方 式基本可以分為; 1 .回轉運動的傳遞的方式有:帶傳動,鏈傳動,齒輪傳動,蝸輪傳
15、動等; 2 .實現(xiàn)擺動或直線往復運動的有:齒輪齒條傳動,螺旋傳動,曲柄滑塊機構,凸輪機構等; 3 .實現(xiàn)間歇運動的有:槽輪機構和棘輪機構等; 4 .實現(xiàn)特定運動規(guī)律的有:凸輪機構和平面連桿機構等。 根據(jù)設備工作機構所需要的運動形式,載荷的性質(zhì)以及設備的工作重復進行來選用傳動機構。 確定一種較好的傳動方案是要在進行全方面分析和對比各種傳動機構特性的基礎上。 原動機、傳動機構和工作機等三部分組成了設備的傳動系統(tǒng)。傳動機構位于工作機和原動機之 間,用來傳遞動力和運動的,也可以變換轉速、轉矩的大小或變換運動的方式,從而適應工作機所 需功能要達到的要求。整各設備的性能、尺寸、重量和成本都會受
16、到傳動機構的設計的影響,所以 擬定合理的傳動方案是很需要的。在本次的畢業(yè)設計中,已算出切管機的 i總=20,如果用蝸桿,只 需要一次降速就可以達到,其方案如圖 3-1。但是由于加工的管子最大的直徑為 4〃,如圖2-1,所以 兩個滾筒的中心距離不能夠小于 108mm ,因此帶動兩個滾筒的齒輪外徑不能大于滾筒的直徑 (? 100mm)。如果取蝸桿 Zi=2,蝸輪Z2=40, m=4,則蝸輪分度圓直徑 d2=160mm,比同一軸上的 齒輪大,按照圖 3-1的裝配,蝸輪將會和滾筒相撞,因此加大兩軸之間的中心距是很需要的。這樣 就需要加上一個惰輪,才能夠解決這個問題,如圖 3-2。在本次畢業(yè)設計
17、中,取蝸輪齒數(shù)為 Z2=50, 模數(shù)m=4o由于帶傳動具有緩沖和過載打滑的特性,所以可以將其作為在電機之后的第一級傳動, 由于在這種條件下齒輪工作容易產(chǎn)生沖擊和噪音,所以開式齒輪傳動不宜放在高速級,故低速級是 齒輪傳動的選擇。滿足設備的功能需求和尺寸緊湊、工作可靠、結構簡單、成本低廉以及使用維護 方便這些方面才能使傳動方案能夠達到要求。經(jīng)過比較想到的傳動方案,在本次畢業(yè)設計中確定采 用帶傳動、蝸桿傳動、齒輪傳動等機構組成的傳動方案。 圖3-1蝸輪蝸桿傳動方案圖 蝸桿傳動 主要的優(yōu)點 傳動平穩(wěn),結構簡單,中 心距變化范圍較大,能緩 沖并起過載安全保護作 用 外廓尺寸小,傳動比
18、準 確,效率高,壽命長,適 用的功率和速度范圍大 單級傳動比,i 開口平型帶:2?4,最大值 06,三角帶型:2?4,最 大值0 7有張緊輪平型 帶:3?5最值0 8 外廓尺寸 成本 n 效率 低 平型帶0.92?0.98 三角帶0.9?0.96 外廓尺寸小,傳動比大而 準確,工作平穩(wěn),可制成 自鎖的傳動 開式圓柱齒輪:4?6,最 日古一 閉式:10?40,最大值0 大值0 15.開式圓柱正 100 齒輪:3?4,最大值0 10. 開式:15?60,最大值0 閉式圓柱齒輪:2?3,最 100 大值< 6 中,小 開式力口工齒0.92?0.
19、96 閉式0.95?0.99 開式0.5?0.7閉式0.7? 0.94 自鎖 0.40 ?0.45 圖3-2蝸輪蝸桿加中間惰輪傳動方案圖 在確定傳動方案后,根據(jù)^=i1,i2……的關系進行傳動比的分配。下面對這個機構的主要特性進 行比較,如表3-1: 表3-1主要的幾種傳動機構的特性比較 帶傳動 齒輪傳動 1 4.5 1 i"… 二20 傳動裝置的結構,尺寸,重量,工作條件和制造安裝等因素是傳動比進行合理的分配 .的時候必須考慮到 的方面。根據(jù)公式 T=9550~pN m (3-1) n 可知,當傳動的功率 P一定時,轉速n越高,轉矩T就越小
20、.因此,對傳動比的分配要謹遵”降速要先 少后多”V帶傳動的傳動比不能過大,不然大帶輪半徑超過減速器的中心會過高,造成尺寸不一 致,還給機座的設計和安裝帶來問題,又由于齒輪在降速傳動的過程中,如果降速比過大,就會使 被動齒輪直徑過大,而增大徑向的尺寸, 還會由于小齒輪的齒數(shù)太少而產(chǎn)生根切的情況, 然而其在升 速傳動的過程中,如果提速比較過大,就會容易引發(fā)劇烈的噪音和震動,造成傳動不穩(wěn)定從而 ,影響 設備的工作性能,因此,各個機構的傳動比分配情況如下 i1 =1.2 i2 =50 i3 =1.5 i4 注:傳動系統(tǒng)中的大齒輪是個惰輪 ,它不改變傳動比只起加大中心距 ,改變滾筒旋轉方向的作
21、用. 3.3 各軸轉速、功率和轉矩的計算 查表得:取“帶=096 , “渦=0.72 ,嚙=0.94 ,“滾=0" (一"對滾動軸承的效率),根據(jù)公式: (3-2) 可知各軸的轉速為: 各軸的功率為: 各軸傳遞的轉矩為: 第三軸,由于過渡齒輪(惰輪)的關系此軸不承受轉矩,只受彎矩,而且它是一根心軸。 將以上各數(shù)據(jù)制成如表 3-2所示的表格: 表3-2各軸的計算結果 軸號 電機軸 I n m IV 傳動比i 1.2 50 1.5 1/4.5 轉速 n(r/min) 1410 116.7 23.3 15.5 70 功率P(Kw) 1.5
22、 1.44 1.03 0.96 0.89 轉矩T (N ? m) 10.23 11.78 420.02 122.3 當帶輪直徑和齒輪模數(shù)確定下來后,兩帶輪直徑之比就等于實際的傳動比也可以是兩齒輪齒數(shù) 之比,計算的結果可能與上述表格計算的數(shù)值出現(xiàn)不一致的狀況。 當i<5時,容許誤差不超過 2.5%; 當i >對,則不容許超過 4%。 3.4 進行傳動機構的設計與計算 3.4.1 設計帶傳動 帶傳動適用的場合[6]:中心距變化范圍較大,結構簡單,傳動平穩(wěn),能緩沖,可起過載安全保 險的作用。不足之軸上受力較大,處是外廓尺寸大,傳動比不能嚴格保證,壽命低(約 3000~
23、5000 小時)取帶的工作情況系數(shù)為 K1=1.1,則功率為:7 P計=K i .睢=1.1 1.5 = 1.65 Kw 由p十計和n〔 =1400r/min ,可查知,選用 A型三角帶。 初步選定小帶輪直徑 d1 =100mm,大帶輪直徑,d2 =i〔 d[ =1.2父100 = 120mm取其標準 直徑d2 =125mm驗算帶輪: 二 dE1 二 100 1400 v = = 7.36m/s 60 1000 60 1000 因為v小于25m/s,適合。 初定中心距aO,按結構要求和公式: (3-3) 選取 三角帶長度按下述公式計算: 取標準長度為L計=103
24、3 mm,其內(nèi)圓周長度 L內(nèi)= 1000 mm。所以實際中心距為: 驗算小帶輪上包角 ai,按下述公式計算: V 1 7 6 > 1 2;0 合適 計算三角帶輪根數(shù)。當帶輪速度 v=7.36m/s, A型,小帶輪直徑 d〔 =100 mm時,由表查得 No 之0.96 , K包角=0.99, K帶長=0.89 ,所以: 取z=2根。 3.4.2 蝸桿蝸輪傳動的設計與計算 蝸桿采用45鋼、表面硬度>45HRC[6]。 蝸輪的材料為 ZCuSn10P1,為砂型鑄造 (1)初選d1/a的值 當量摩擦系數(shù)設 由查表取最大值 (2)中心距的計算 蝸輪轉矩 使用系數(shù)查表得 轉速系
25、數(shù) 彈性系數(shù)根據(jù)蝸輪副材料查表可知 壽命系數(shù) 接觸系數(shù)由查表得 接觸疲勞極限由查表得 接觸疲勞最小安全系數(shù)查表得 中心距 (3)傳動基本尺寸 蝸桿頭數(shù)由查表得 蝸輪齒數(shù) 模數(shù) 蝸桿分度圓直徑 蝸輪分度圓直徑 tan z1 m/d 1 = 2 父 3/ 34 = 10 蝸桿導程角 蝸輪寬度 蝸桿圓周速度 相對滑動速度 當量摩擦系數(shù)經(jīng)查表得 (4)計算齒面接觸疲勞強度 許用接觸應力 最大接觸應力 105MPa173MPa.合格 (5)驗算齒輪彎曲疲勞強度 齒根彎曲疲勞強度極限由查表得 彎曲疲勞最小安全系數(shù)查表得 許用彎曲疲勞應力 齒輪最大彎曲應力
26、 ;二合格 (6)驗算蝸桿軸撓度 軸的慣性距 允許蝸桿撓度 蝸桿軸撓度 3.4.3 設計與計算齒輪傳動 1 .第一對齒輪 (1)齒輪材料選擇 小齒輪材料:40Gr、采用調(diào)制處理,硬度 241HB-086HB、取平均260HB 大齒輪材料:45鋼、采用調(diào)制處理,硬度 229HB-286HB、取平均240HB (2)計算齒面接觸疲勞強度 ①初步計算 轉矩T1 齒寬系數(shù)甲d由查表得 甲d =0.4 接觸疲勞極限
27、得 初步計算小齒輪直徑 d1 取 d1 =187.3mm 初步齒寬b 取 b = 75mm ②校核計算 圓周速度 精度等級由查表得選取八級精度 齒數(shù)z與模數(shù)m 初取齒數(shù) z1 = 54 zi =d〃m=187/3=62 取 M -3 使用系數(shù)Ka由查表得 動載系數(shù)K v由查表得 齒間載荷分配系數(shù) K H .. 先求 Zi =62 K A =1.5 KV =1.12 Z2 = 93 由此得 齒向載荷分布系數(shù) K H B由查表得 載荷系數(shù)K 彈系數(shù)由查表得 節(jié)點區(qū)域系數(shù)Z H由查表得 接觸最小安全系數(shù)SH min查表得 總工作時間 接觸壽命系數(shù)
28、Zn由查表得 許用接觸應力[二H1] 驗算 Sh min =1.05 二 h ; 690Mpa .合格 因此表明了接觸疲勞強度較為合適,齒輪尺寸不用調(diào)整。 (2)確定傳動主要尺寸 實際分度圓直徑d d1 = mz1 = 3 62 =186 d2 =mz2 =3 93=279 中心距a 齒寬b (3)驗算齒根彎曲疲勞強度 重合度系數(shù)Y
29、齒間載荷分配系數(shù) Kf .. 齒間載荷分布系數(shù) Kf 載荷系數(shù)K 齒形系數(shù)Yfq由查表得 應力修正系數(shù)工〃由查表得 彎曲疲勞極限cTFim由查表得 彎曲最小安全系數(shù)SFlim由查表得 應力循環(huán)次數(shù)Nl由查表得 彎曲壽命系數(shù)Yx由查表得 許用彎曲應力 彎曲壽命Yn由查表得 驗算 Kf 一 二1.47 Y . =1/0.68 Fh = 1.38 Yf-1 =2.5 Yf ..2 =2.2 二 Fliml =600 0 Flim2 =450 SF lim -1.3 Nl2=1.92 107 yx -1 Yni =0.95 Yn2 =0.97
30、 F 1 ::: [ --, F 1 ] F2 :: [ - F 2 ] 2 .計算第二對齒輪 齒輪2為惰輪,即此處的大齒輪。材料為 45鋼,調(diào)制處理,硬度為 229HB-286HB. 平均取240HB (主動)。 齒輪3是小齒輪,材料選擇 40Gr,調(diào)制處理,硬度值為 241HB ~286HB,平均取260HB. (1)計算齒面接觸疲勞強度 1.初步計算 轉矩T1 齒寬系數(shù)中d由查表得 中d =0.4 接觸疲勞極限仃Hlim由查表得 OHlim1 =710MPa 。h lim 2 = 580MPa 初步齒寬b 取 2 .校核計算 圓周速度 精度等級由查得選取八級精
31、度 齒數(shù)z與模數(shù)m 已知 使用系數(shù)Ka由查表得 動載系數(shù)K v由查表得 齒間載荷分配系數(shù) Kh-. 先求 由此得 齒向載荷分布系數(shù) K H P由查表得 載荷系數(shù)K 彈性系數(shù)Ze由查得 節(jié)點區(qū)域系數(shù)Zh由查表得 接觸最小安全系數(shù)SHmin由查表得 總工作時間 接觸壽命系數(shù)Zn由查表得 許用接觸應力[二H1] 驗算 以此表明了接觸疲勞強度較為合適, 3 .傳動主要尺寸的確定 實際分度圓直徑d b =112 mm m=3 Zi =93 i =1/7.5 z2 =iz1 =1/7.5 93 =12.4 Ka =1.5 Kv =1.2 K h ; ==1.3 Z
32、e =189.8、MPa Z h - 2 SH min = 1.05 Zni =1.7 Zn2 =1.6 h h < 884 Mpa 二合格 齒輪尺寸不用調(diào)整。 d1 = mz1 = 3 93 = 279 d2 = mz2 =3 12 = 36 中心距a 齒寬b 4.齒根彎曲疲勞強度驗算 重合度系數(shù)Y . 齒間載荷分配系數(shù) K fa
33、經(jīng)查表得 載荷系數(shù)K 齒形系數(shù)Yf^查表得 應力修正系數(shù)Ys 0t查表得 彎曲疲勞極限CTFlim由表得 彎曲最小安全系數(shù)SFlim查表得 彎曲壽命系數(shù)YX由查表得 許用彎曲應力 Kf:. =1 Kf:. =1.47 Yfj =2.0 Yf-.2 =2.5 Ys「=1.5 Ys:.2 =1.75 F lim 1 = 600 F lim 2 = 350 SFlim =1.3 Y x =1 彎曲壽命Yn由查表得 Yn1 =0.95 Yn2 =0.97 驗算 二 F 1 "二 F 1] 二 F 2 :二「二 F 2 ] 3.4.4 確定齒輪模
34、數(shù) [8] O y=0.298,許用彎曲應力 20%,實際許用彎曲應力 齒輪的材料,熱處理方式和受力的大小等因素決定齒輪模數(shù)的大小 本次確定齒輪模數(shù)可以采用公式法進行設計。查表可得:齒形系數(shù) [。彎]=19.6kg/mm2,但是考慮到開式齒輪傳動齒面磨損,許用彎曲應力降低 為: [仃彎]=19.6 80%=15.68kg/mm2 對于開式齒輪傳動,齒寬系數(shù)為 中m =8?15,現(xiàn)因齒輪制造精度較低,并且為懸臂支承,故選 較小的。值,取^m =10。 載荷系數(shù)K=1.3?1.5,因為有懸臂支承,取 K=1.3,根據(jù)公式: (3-4) 取標準值m = 3mm,強度稍小一些。齒
35、輪的模數(shù)在一個傳動系統(tǒng)中不會完全一樣, 轉速較高, 傳遞轉距較小,模數(shù)也會比較小。但是加工需要測量方便,齒輪模數(shù)的種類也要越少越好,因此本 次設計的切管機的齒輪模數(shù)都取 m = 3mm。 3.4.5 確定蝸輪蝸桿模數(shù) 蝸桿選用4 5號鋼,調(diào)質(zhì)處理,蝸輪采用無錫青銅 ZQA19-4。 根據(jù)公式: (3-5) 取標準模數(shù) m=4,q--11。 3.4.6 齒數(shù)的確定 齒數(shù)主要是根據(jù)傳動比的要求確定的,所以根據(jù)各個傳動比有: (1)蝸桿頭數(shù)和蝸輪齒數(shù)的確定: 動比的要求和效率、 制造和自鎖是在選擇時蝸桿頭數(shù)要考慮 道德因素,然而產(chǎn)生根切和蝸輪的直徑(也就是體積問題)是蝸輪齒數(shù)選用
36、時主要考慮到的方面, 而且頭數(shù)越多,效率就越高??紤]到自鎖這個方面,應該要選擇單頭。從制造這個因素來看,頭數(shù) 越多,制造困難的程度就要高。所以要根據(jù)上述的綜合因素來確定蝸桿頭數(shù)。 一般來說,,當提高效 率在動力傳動中的過程中是主要問題的時候, 就采用多頭;在提高精度的時候(分度蝸桿),主要矛 盾是自鎖的性能優(yōu)越或要求降速比規(guī)定的大, 采用單頭。綜合上述原因,查閱[9]可知:蝸桿頭數(shù)z1 =1 , 蝸輪齒數(shù)Z2 =50。 (2).確定齒輪齒數(shù):在選擇齒輪齒數(shù)的時候, 應該將傳動比和最小的齒數(shù)的要求綜合考慮在內(nèi), 齒輪的加工方式和方法與最小齒數(shù)的限制息息相關,加工直齒輪準齒輪的時候如果用插
37、齒刀或齒輪 滾刀,為了使根切這種情況不發(fā)生,齒輪數(shù)的最低限制不得低于 17,所以在本次設計中初步選取最 小齒輪齒數(shù)為Z4=18。這個齒輪裝在切割機的滾筒上的軸上。 根據(jù)工作的相應條件計算的傳動比可 知: 將Z4 =18代入,則 并由此可以推得: 從而可知切管機齒輪的全部(蝸輪蝸桿)的齒數(shù) :z1 =1,z2 =50, z2 =54,z3 =81, z4 =18o 第4章結構設計 4.1各軸的最小直徑的初算 軸的各段直徑和長度的計算方法列于表 4-1 表4-1軸的各段直徑和長度 代號 名稱 推薦尺寸 說 明 舉例:切管機蝸桿軸 di 軸的最小直徑 根據(jù)扭矩或彎矩
38、強度條 件初步計算 若此段有鍵槽,應 將直徑增加5% d1=13 取為 20mm d2 安裝密封處的直 徑 d2> di+2r r一倒圓直 徑,查閱手冊中非配合處 的過度圓角半徑 用凸肩定位時按 此式計算, 用套筒定位時另 取 帶輪的定位靠套筒, 此處的d2是指套筒外 徑 d3 安裝滾動軸承處 的直徑 d3> d2 d3> di 無套筒的; 套筒的d3必須符 合軸承的標準 由于采用205型軸承, d3=25mm 裝在兩滾動軸承 d4> d3+2r d4 之間齒輪(蝸輪) r—倒圓角半徑,查閱手 如口軸 處的
39、直徑 冊確定 如口軸, d5 一般軸肩和軸環(huán) 的直徑 d5= d4+2a a一軸肩或 軸環(huán)的高度, a=(0.07?0.1) d4 d4=55mm, a=3.85?5.5mm,取 a=5mm,貝 U d 5=55+2*5=65mm 因此處d4相當于 da=25, a=0.1 d4 貝1J d5=25+2*2.5=30mm d6 滾動軸承定位軸 肩直徑 查閱手冊軸承部 分的D1值 L7 安裝旋轉零件的 軸頭長度 L7= (1.2?1.6) d d---軸頭直徑 一般要求L7要比 旋轉零件的輪轂 寬度要短一些 L 8k 1.
40、4a 或 L 8y 如 口 軸 L8 y L 8 軸環(huán)長度 (0.1~0.15) d 1.4*5=7mm 由于軸上彎曲應力的分布和軸的結構尚屬未知, 只知道軸所傳遞的轉矩(轉速),所以按照轉矩(轉 速)初算軸的直徑。 I軸:選取材料為 45鋼,調(diào)質(zhì)處理。根據(jù)公式 (4-1) 計算。 因為I軸為懸臂軸,查表可知: 取 A =14 pI =1.44KW n1=116.7r/mi n 則: 由于鍵槽的削弱等因素,取標準直徑為 20mm。 n軸:選取材料為 45鋼,調(diào)質(zhì)處理。取 A =12,已知Pn=1.03Kw , n2 =23.3r/min則: 標準直徑取45mm。 出軸:
41、此軸為傳動心軸,暫選材料為 45鋼,調(diào)質(zhì)處理,由于其受力情況未知,初選其最小軸徑 為50mm,待后進行檢驗。 W軸:選取材料為 45鋼,調(diào)質(zhì)處理。則: 取標準直徑為30mm。 將所得結果制成下表,供設計計算時應用: 表4-2各軸的最小直徑 軸 號 I 口 m iv 最小直徑(mm) 20 45 50 30 4.2 計算各主要傳動件的結構尺寸 4.2.1 三角帶輪 已知選用A型三角膠帶,小三角帶輪計算直徑為 d小=100mm ;查表可知: hg =3.5mm、B=6mm , H =12mm、e =150.3mm、f = 10 mm、% =34 二、b0 = 13.1mm。
42、輪寬 外徑 孔徑d等于電動機輸出軸直徑,查電動機 JO2得d軸=22 mm 其結構形式查表可知為實心輪 。 大三角帶輪計算直徑 d大=125mm h、8、H、e 、f、B等尺寸和小三角帶輪一樣。 0 =38 bo =13 4mm 外徑 孔徑d等于與其配合的軸I的軸徑,查表可知I軸的 d軸=20 mm 結構形式由查表可知為輻板式: 輪緣直徑 輪轂直徑 ,,取d轂=40 mm 輪轂寬度 一取L = 35 mm 輻板厚度查表得為 S=10mm; 輻板孔圓周定位尺寸: 因此,孔直徑為 4.2.2 蝸輪和蝸桿 已知 z1 =1、z2 =50 , m=4 , q =11 ,
43、查表得: 蝸桿分度圓直徑 蝸輪分度圓直徑 蝸桿齒頂圓直徑 蝸輪齒頂圓直徑 蝸桿齒根圓直徑 蝸輪齒根圓直徑 蝸桿分度圓圓柱上螺旋升角 ?」=arctan2,當z, =1、q=11時,查得 九=51140" q 蝸桿切制螺紋部分的長度 蝸輪外圓直徑 蝸輪寬度 1、 n軸中心距: 可知:輪緣厚度 f =1.7m =1.7 4 = 6.8mm 蝸輪的孔徑d取決于軸的結構設計,因蝸輪軸的最小直徑為 42mm,取孔徑d = 55mm 輪轂外徑 取 ~轂=90 mm 輪轂寬度 取 L = 70 mm 輻板厚度c1.5m=1.5x4=6 , 一般采用c=10mm蝸輪包角2
44、 =90?100,一般采用2尸=90 4.2.3 齒輪 (1)已知n軸上齒輪 z2=54, m = 3,貝U: 分度圓直徑 齒頂圓直徑 齒根圓直徑 因為齒輪制造的精度比較低,而且是懸臂布置,所以齒寬的系數(shù)宜選擇小值,取 Wm=10 齒寬 由于d頂2 >16cmm ,可選用輻板式結構的鍛造齒輪。 輪緣內(nèi)徑 輪轂外徑 d轂=1.6 d蟀一一齒輪的孔徑,查表可知 d軸2 =45mm 輻板厚度 輻板孔圓周的定位尺寸: 輻板孔直徑: 取 電=17mm 齒輪示意圖如圖4-1 圖4-1 口軸齒輪示意圖 (2)已知出軸上齒輪 z3=81, m=3,則: 分度圓直徑
45、齒頂圓直徑 齒根圓直徑 齒寬 B = 30 mm 因為d根3 A 160 mm ,可選用輻板式結構的鍛造齒輪。 輪緣內(nèi)徑 輪轂外徑d轂=16 d軸3 =1.6父50 =80mm (d燧 齒輪的孔徑,查表可知 d根3 = 50 mm ) 輻板厚度 輻板孔圓周定位尺寸: 輻板孔直徑: d孔=35 mm n、in軸的中心距: 圖4-2 W軸齒輪示意圖 (3)已知IV軸上的齒輪 Z4 =18, m =3則: 分度圓直徑 d4 = mz4 =3 18 = 54mm 齒頂圓直徑 d頂 4 =m(z4+2)=3(18 + 2) = 60mm 齒根圓直徑 ~根4 =m(4
46、 -2.5) =3(18—2.5) = 16.5mm 齒寬 B = 30 mm 因為~根3 <160mm , 所以必選用實心式結構鍛造齒輪。 出、IV軸的中心距: a限 iy=2m(z3 +z4)= ;m3(18+81) = 148.5mm 圖4- 31V軸齒輪示意圖 4.3 軸的裝配工藝設計 1 .初定軸承跨距、設計軸承組合的結構形式 有經(jīng)驗公式確定 L〔 =0.8a ,已知蝸桿傳動中心距 a =122mm ,則L〔 =08父122 = 97.6mm ,從而得 到軸承的跨距為150mm (蝸輪分度圓直徑)。 由于蝸桿傳動同時受到徑向力和軸向力,且此處的軸承跨距不大,
47、故采用單列向心推力球軸承 6000 型。 對于軸承尺寸的選擇,根據(jù)軸頸直徑選擇軸承的內(nèi)徑,再者考慮到負載荷能力和結構上的特點,此 處宜采用輕窄系列。 對于軸承組合的結構形式,此處的蝸桿軸較短,傳遞功率小和轉速中等,故采用正排列的向心推力 球軸承,因軸的直徑為 25mm,故選兩個6205型和兩端固定支座的結構形式,并用墊片調(diào)整軸承間 隙。 2 .固定軸向零件的周向和軸向 軸段三角帶輪的周向固定是采用普通平鍵和過渡配合 920 H8。根據(jù)軸的直徑di=20 k7 選用“鍵6 M 32GB1 096-79"。三角帶輪的軸向固定是靠套筒和軸端檔圈。套筒的直徑尺寸參照(軸 的各段直徑和長
48、度)軸端檔圈的選用根據(jù)[10],其中軸端直徑d=20mm選用“檔圈28GB892-76 螺 栓 M5 M 14GB30-76”,“銷 2n6 M 10GB119-76 ”,“墊圈 5GB93-76”。 軸上其它零件的尺寸和固定方式按照下表的經(jīng)驗公式確定。由于蝸桿蝸輪使用的是機油潤滑, 而軸承使用的是油脂,因此,選用檔油歡這種密封結構。為了軸向固定更加可靠,凡是與旋轉零件 (如帶輪、齒輪、蝸輪、軸承等)配合的軸頭長度在設計時都比旋轉零件的輪轂寬度要短一些。 4.4 各傳動軸尺寸的計算與校核 4.4.1 剛度的校對和申核的重要性 載荷的作用應用到軸上,平面上的形狀發(fā)生變化或形狀變形將會發(fā)
49、生。 若形狀大聲變化的量超 過最高限度,那么軸上的零件的正常運作將會受到影響, 甚至機器原有的工作質(zhì)量都會丟失。 比如, 齒輪軸在安裝的過程中,若扭轉的剛度(或彎曲的剛度)不夠而促使扭轉的角度(或撓的角度)過 于太大時,那么齒輪的正確的嚙合的程度將會受到影響,使齒輪在齒高和齒寬的位置接觸的面積不 完全,從而使載荷在齒的平面上分布不均勻的情況比較嚴重。又比如使用滑動的軸承上面的軸,如 果撓度過于太大而致使軸的頸部傾斜過于太大的時候,會使軸的頸與滑動的軸承發(fā)生邊緣的觸碰, 形成不平均的摩擦損壞和發(fā)熱的過度。所以,對于軸的剛度要求給出的時候,在設計的過程中,一 定要對剛度進行仔細的的校對和申核的
50、相關計算 [10]。 4.4.2 蝸桿軸的尺寸計算與校核 (1)估計軸的基本直徑。 材料選用45鋼、正火處理。 查表得:硬度(HBS) 17.~217 強度極限ab =600 MPa ,屈服極限。$ =300MPa , 彎曲疲勞極限o」=275MPa 查表取C =118 (2)初估直徑 因為最小處有鍵所以直徑增大 3% (3)軸的受力分析 1 .求軸傳遞的轉矩 2 .蝸桿上圓周力Ft1 蝸桿上徑向Fri 蝸桿上軸向力F 4 3 .計算支反力 水平面反力 垂直面支反力 4 .軸受轉矩 5 .許用應力 許用應力值 查表得 卜」b〕=60M P a 6 .當量彎矩
51、的計算 當量轉矩 當量彎矩蝸 輪中間截面處的當量彎矩蝸 右軸頸中間截面處的當量彎矩蝸 7 .4.3蝸輪軸的尺寸計算與校核 (1)估計軸的基本直徑。 材料選用45鋼、正火處理.o查表得:硬度 (HBS) 170-217 強度極限6 =600 MPa ,屈服極限5 =300 MPa , 彎曲疲勞極限cr」= 275MPa 查表取C =118 (2)初估直徑 d -38mm 應為最小處開有鍵所以直徑增大 3% d之39mm (3)軸的受力分析 1 .求軸傳遞的轉矩 2 .蝸桿上圓周力Ft1 蝸桿上徑向Fr1 蝸桿上軸向力F -1. 3 .計算支反力 水平面反力 垂
52、直面支反力 軸受轉矩 T =Ti T =341070N m 4 0b L 105 MPa 4 .許用應力 許用應力值查表得 Jb l-60MPa 當量轉矩 當量彎矩蝸輪中間截面處 5 .4.4惰輪軸的尺寸計算與校核 軸出上裝有的主要零件為:軸承、鍵、軸環(huán)、帶輪等。由表 4-2可知其最小直徑為 45mm 0已 知:z 2齒輪分度圓直徑 d 2=162mm,z3齒輪分度圓直徑 d3 = 243mm ,z4齒輪分度圓直徑 d4= 54mm , n、出軸中心距 如『202.5mm,出、IV軸中心距 沏X148.5mm ,兩滾筒中心距 108mm, n軸轉矩 Tpj = 42
53、0.2N M , N軸轉矩 Tn = 122.3 N M。 驗算過程: 由于運動是從齒輪 Z 2經(jīng)惰輪Z3傳給兩個Z4齒輪,在惰輪Z3的圓周上就同時作用著 R、P2、 P3三個切向力; ⑴根據(jù)滾筒中心距108mm和 如iv=148.5mm ,我們可以計算出 a角。因為在直角三 角形出、 IV、V 中 所以 :?=2 1 19 根據(jù)轉矩 T =P - 2 (2)利用力的平移和四邊形法則,求作用在出軸上的合力。用作圖法可量得 (3)出軸的最大彎矩都集中在 B支座,也就是惰輪 Z3的中面到滾動軸承中面的長度。取 l3=70mm的位置,則最大彎矩為 : 1 .當軸的材料為45號鋼時,
54、轉動心軸的 B=0.26,則: 現(xiàn)在設計軸頸的直徑為 55mm,所以合適。 2 .結構中所用潤滑為 L-CPE/P蝸輪蝸桿油,滾珠軸承脂 (SY1514--82 ), 7407號齒輪潤滑脂 (SY4036— 84)所用密封方式有氈圈式密封,迷宮式密封槽密封 圖4-4軸W的受力分析 4.4.5滾輪軸的尺寸計算與校核 (1)估計軸的基本直徑。 材料選用45鋼,正火處理查表得:硬度( HBS) 170-217 彎曲疲勞極限二-」二275 MPa 強度極限g =600 MPa ,屈服極限 工=300 MPa , d _ 15mm d - 35mm 查表取C =118 (2)
55、初估直徑 因為最小處有鍵所以直徑增大 3% (3)軸的受力分析 1 .求軸傳遞的轉矩 2 .蝸桿上圓周力Fti 蝸桿上徑向F r1 蝸桿上軸向力F :! 3 .計算支反力 水平面反力 垂直面支反力 4 .軸的彎矩 水平面彎矩 合成彎矩 5 .軸的轉矩 軸受轉矩 T =T1 T =70 72 N5m 6 .許用應力 許用應力值查表得 卜上】二60M P a 當量轉矩 當量彎矩 7 .5確定減速箱的尺寸 根據(jù)表4-2的數(shù)數(shù)據(jù)和尺寸,并根據(jù)切管機機構示意圖。確定箱殼外型尺寸為: 長: 寬度為165mm 高: 表4-2減速箱各零件間相互位置尺寸 代號
56、 名稱 推薦尺寸 說明 切管機減速箱取值 Bi 齒輪寬度 由結構 設計定 Bi=30 B 帶輪寬度 由結構 設計定 B=35 b 軸承寬度 根據(jù)軸頸直徑,按中或輕窄系列 決定 查手冊 待定,如蝸桿軸的軸承,暫選為 6205,則 b=15 S 箱殼壁厚 0 之0.04a+(2L 3)之8, a為蝸 輪傳動中心距 取S =8 旋轉零件頂圓 A 至箱殼內(nèi)壁的 △ =1.2 S M A =10 距離 蝸輪齒頂圓至 △i 軸承座邊緣的 △i=10 ?12 MA i
57、=10 徑向距離 Li 蝸桿中心至軸 承中心的距離 Li=0.8a, a為蝸桿傳動中心距 已知a=122 故 L1=97.6 L2 軸的支承間跨 距 由設計 — L3 箱外旋轉零件 的中面至支承 點的距離 b 6或B L3=2 L5 L6 2 L3 =竺 120 15 竺=60 2 2 L4 滾動軸承端面 至箱殼內(nèi)壁的 距離 當用箱殼內(nèi)的油潤滑軸承時,L4 *5 當用脂潤滑軸承時,并有擋油環(huán) 時,L4=10 ?15 取 L4=5 由端蓋 結構和 軸承端面至端 固緊軸 選L5=20 L5 蓋螺釘
58、頭頂面 承的方 的距離 法確定 箱外旋轉零件 端面至端蓋螺 L6 L6=15 ?20 取 L6=20 釘頭頂面的距 第5章總結 為期半年多的畢業(yè)設計在今天終于完成了。在這設計過程中了,大學四年所學專業(yè)知識的掌握 程度得到了很好地考驗,明白了哪些知識還要繼續(xù)學習掌握。 對于切管機的設計,在這四年中學到了各種機械方面的知識,從這一設計題目的綜合運用中, 更是把所學的這些知識有了一個大的融會與應用,從而所學的知識也不再是死的,有了一個比較全 面的復習。在設計與計算的過程中,也遇到了許多的困難與問題。通過查找資料,將這些問題解決 的這種獨立的解決問題和思考的方法,是在這次設計中我得到
59、的一個最大的收獲。當然,從中也大 致了解了一些產(chǎn)品設計的基本方法,這也將是一次寶貴的實踐經(jīng)驗。 本次設計的切管機主要是針對各種用途金屬管材進行加工。本次設計的任務主要是對切管機中 減速箱及有關零件進行的設計。其中包括傳動裝置的設計和計算。總體結構的設計以及對設計計算 進行校核。并且通過得到的數(shù)據(jù),繪制總體裝配圖,減速機裝配圖等。然后又針對各主要基本件, 繪制了多張零件圖。本次設計的切管機為減輕工人的勞動強度,提高生產(chǎn)效率有著積極的意義。 根據(jù)切管機的結構特點提出多個可行的設計方案,最后在根據(jù)實際各種情況選擇最合理的設計 方案。首先確定切管機幾個主要的零部件,如帶輪、蝸輪軸、套管、蝸桿軸、滾
60、輪軸承等。在繪制 圖紙時,首先繪制切管機的總裝配圖, 再到減速箱的裝配圖, 最后到各個零件圖。 在繪制完圖紙后, 就進行切管機的設計計算和校核,并且在確定切管機的相關制動參數(shù)后,對切管機在切割管子時的 工作質(zhì)量進行技術,最后對切管機的設計進行優(yōu)化。 本設計的主要設計思路及過程: (1)整個切管機制動過程方案的確定 通過查閱書本和各種文獻,了解現(xiàn)代切管機的工作原理,把各種資料進行整理分類,確定出最 合理的方案。 (2)切管機主要零部件的設計 根據(jù)各種資料,對切管機主要零部件的形狀進行設計并選用合適的材料,如渦輪軸、蝸桿軸、 帶輪等。設計要求符合實際,選擇材料要符合強度。 (3)對切管機進行校核 對切管機的各個軸的剛度情況進行計算和校核,使其結果符合國家規(guī)定。 通過本次畢業(yè)設計,我從中學到了以前沒有在書本上學到的專業(yè)知識,深刻掌握了切管機的機 械結構及其工作原理。通過本次畢業(yè)設計的學習,我加深了解了設計的整個過程,從中了解到設計 是一個負責的過程,要有耐心和毅力。在設計過程中,指導老師幫我發(fā)現(xiàn)了設計中的很多缺陷,對 我后來不斷完善設計提供了極大的幫助。我從畢業(yè)設計中學到了很多的實際經(jīng)驗,這對我以后在工 作中打下扎實的基礎。 附錄圖紙列表
- 溫馨提示:
1: 本站所有資源如無特殊說明,都需要本地電腦安裝OFFICE2007和PDF閱讀器。圖紙軟件為CAD,CAXA,PROE,UG,SolidWorks等.壓縮文件請下載最新的WinRAR軟件解壓。
2: 本站的文檔不包含任何第三方提供的附件圖紙等,如果需要附件,請聯(lián)系上傳者。文件的所有權益歸上傳用戶所有。
3.本站RAR壓縮包中若帶圖紙,網(wǎng)頁內(nèi)容里面會有圖紙預覽,若沒有圖紙預覽就沒有圖紙。
4. 未經(jīng)權益所有人同意不得將文件中的內(nèi)容挪作商業(yè)或盈利用途。
5. 裝配圖網(wǎng)僅提供信息存儲空間,僅對用戶上傳內(nèi)容的表現(xiàn)方式做保護處理,對用戶上傳分享的文檔內(nèi)容本身不做任何修改或編輯,并不能對任何下載內(nèi)容負責。
6. 下載文件中如有侵權或不適當內(nèi)容,請與我們聯(lián)系,我們立即糾正。
7. 本站不保證下載資源的準確性、安全性和完整性, 同時也不承擔用戶因使用這些下載資源對自己和他人造成任何形式的傷害或損失。
最新文檔
copyright@ 2023-2025 zhuangpeitu.com 裝配圖網(wǎng)版權所有 聯(lián)系電話:18123376007
備案號:蜀ICP備2024067431號-1 川公網(wǎng)安備51140202000466號
本站為文檔C2C交易模式,即用戶上傳的文檔直接被用戶下載,本站只是中間服務平臺,本站所有文檔下載所得的收益歸上傳人(含作者)所有。裝配圖網(wǎng)僅提供信息存儲空間,僅對用戶上傳內(nèi)容的表現(xiàn)方式做保護處理,對上載內(nèi)容本身不做任何修改或編輯。若文檔所含內(nèi)容侵犯了您的版權或隱私,請立即通知裝配圖網(wǎng),我們立即給予刪除!