端蓋落料拉深沖孔切邊復合模設計
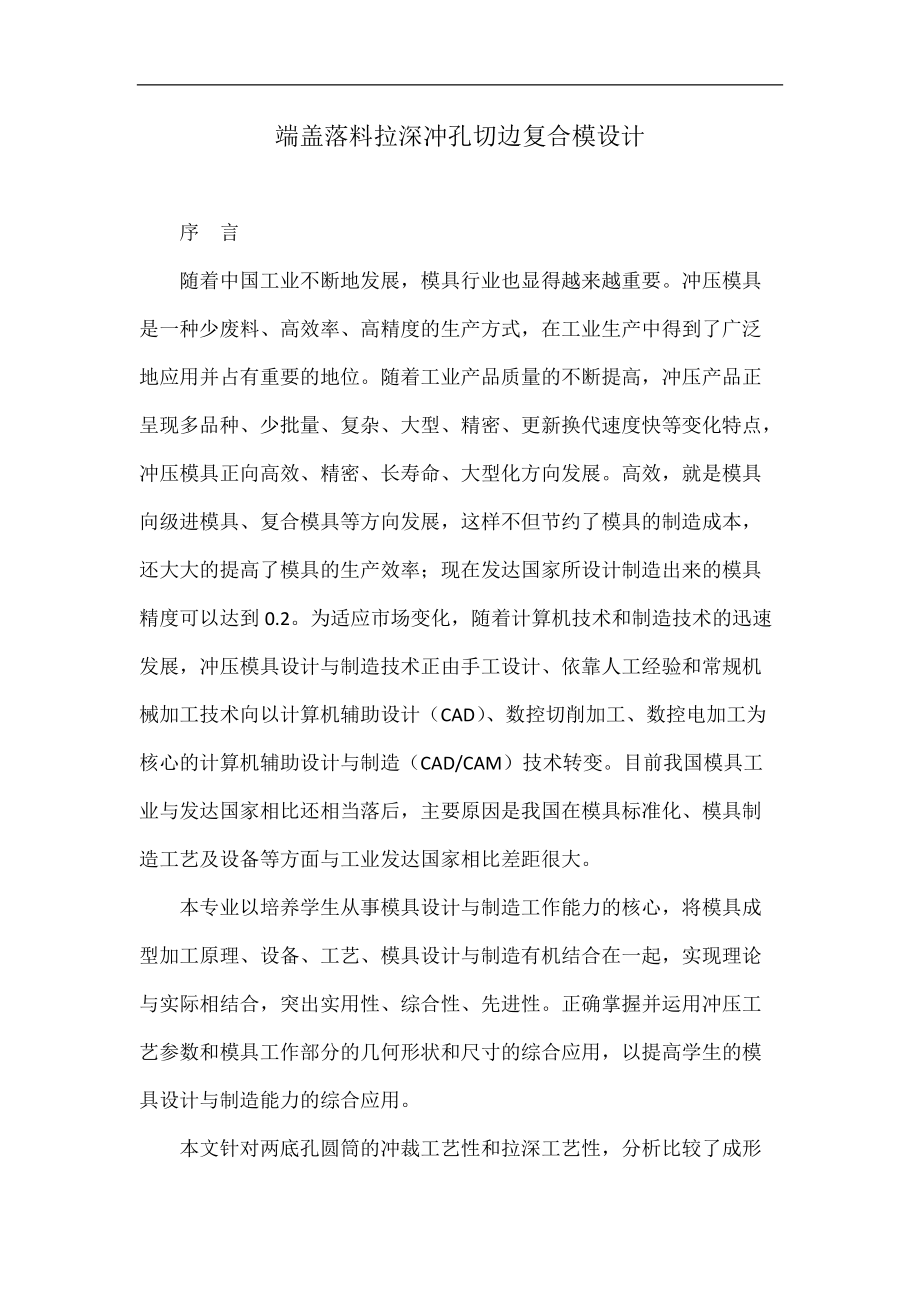


《端蓋落料拉深沖孔切邊復合模設計》由會員分享,可在線閱讀,更多相關(guān)《端蓋落料拉深沖孔切邊復合模設計(41頁珍藏版)》請在裝配圖網(wǎng)上搜索。
1、 端蓋落料拉深沖孔切邊復合模設計 序 言 隨著中國工業(yè)不斷地發(fā)展,模具行業(yè)也顯得越來越重要。沖壓模具是一種少廢料、高效率、高精度的生產(chǎn)方式,在工業(yè)生產(chǎn)中得到了廣泛地應用并占有重要的地位。隨著工業(yè)產(chǎn)品質(zhì)量的不斷提高,沖壓產(chǎn)品正呈現(xiàn)多品種、少批量、復雜、大型、精密、更新?lián)Q代速度快等變化特點,沖壓模具正向高效、精密、長壽命、大型化方向發(fā)展。高效,就是模具向級進模具、復合模具等方向發(fā)展,這樣不但節(jié)約了模具的制造成本,還大大的提高了模具的生產(chǎn)效率;現(xiàn)在發(fā)達國家所設計制造出來的模具精度可以達到0.2。為適應市場變化,隨著計算機技術(shù)和制造技術(shù)的迅速發(fā)展,沖壓模具設計與制造技術(shù)正由
2、手工設計、依靠人工經(jīng)驗和常規(guī)機械加工技術(shù)向以計算機輔助設計(CAD)、數(shù)控切削加工、數(shù)控電加工為核心的計算機輔助設計與制造(CAD/CAM)技術(shù)轉(zhuǎn)變。目前我國模具工業(yè)與發(fā)達國家相比還相當落后,主要原因是我國在模具標準化、模具制造工藝及設備等方面與工業(yè)發(fā)達國家相比差距很大。 本專業(yè)以培養(yǎng)學生從事模具設計與制造工作能力的核心,將模具成型加工原理、設備、工藝、模具設計與制造有機結(jié)合在一起,實現(xiàn)理論與實際相結(jié)合,突出實用性、綜合性、先進性。正確掌握并運用沖壓工藝參數(shù)和模具工作部分的幾何形狀和尺寸的綜合應用,以提高學生的模具設計與制造能力的綜合應用。 本文針對兩底孔圓筒的沖裁工藝性和
3、拉深工藝性,分析比較了成形過程的三種不同沖壓工藝(單工序、復合工序和連續(xù)工序),確定用一幅復合模完成落料、拉深、沖孔和切邊的工序過程。介紹了兩底孔圓筒冷沖壓成形過程,經(jīng)過對工件的批量生產(chǎn)、零件質(zhì)量、零件結(jié)構(gòu)以及使用要求的分析、研究,按照不降低使用性能為前提,將其確定為沖壓件,用沖壓方法完成零件的加工,且簡要分析了坯料形狀、尺寸,排樣、裁板方案,拉深次數(shù),沖壓工序性質(zhì)、數(shù)目和順序的確定。進行了工藝力、壓力中心、模具工作部分尺寸及公差的計算,并設計出模具。還具體分析了模具的主要零部件(如凸凹模、卸料裝置、拉深凸模、墊板、凸模固定板等)的設計與制造,沖壓設備的選用,凸凹模間隙調(diào)整和編制一個重要零件的
4、加工工藝過程。列出了模具所需零件的詳細清單,并給出了合理的裝配圖。通過充分利用現(xiàn)代模具制造技術(shù)對傳統(tǒng)機械零件進行結(jié)構(gòu)改進、優(yōu)化設計、優(yōu)化工藝方法能大幅度提高生產(chǎn)效率,這種方法對類似產(chǎn)品具有一定的借鑒作用。 I 目 錄 1 設計任務及零件的工藝性分析 ··························
5、183;······························· 1 1.1 設計任務 ···············
6、183;·················································
7、183;············································ 1 1.2 零件的工藝性分析 ··
8、··················································
9、·········································· 1 2 確定工藝方案 ·····
10、··················································
11、··································· 3 2.1 計算毛坯尺寸 ···········
12、3;·················································
13、3;········································ 3 2.2 確定是否要壓邊圈 ·······
14、;··················································
15、;···································· 4 2.3 計算拉深次數(shù) ···········
16、183;·················································
17、183;······································· 4 2.4 確定工藝方案 ········
18、;··················································
19、;··········································· 4 3 主要工藝參數(shù)的計算 ···
20、183;·················································
21、183;························ 5 3.1 確定排樣、裁板方案 ·····················
22、83;·················································
23、83;················· 5 3.2 計算工藝力、初選設備 ·····························
24、183;·················································
25、183;····· 7 3.2.1 計算工藝力 ·········································
26、3;·················································
27、3;······ 7 (1)落料力 ··········································
28、··················································
29、·············· 7 (2)卸料力 ··································
30、183;·················································
31、183;····················· 7 (3)拉深力 ··························
32、3;·················································
33、3;····························· 7 (4)壓邊力 ···················
34、··················································
35、····································· 8 (5)沖孔力 ···········
36、183;·················································
37、183;············································ 9 (6)推件力 ···
38、3;·················································
39、3;·················································
40、3;·· 9 3.2.2 拉深功的計算 ·············································
41、;················································· 9 3.
42、2.3 初選壓力機 ················································&
43、#183;··············································· 10 3.2.4 計算
44、壓力中心 ·················································&
45、#183;·········································· 10 3.2.5 計算凸、凹模刃口尺寸及公差 ···
46、··················································
47、··········· 10 4 模具的結(jié)構(gòu)設計 ···································
48、3;················································ 13 4
49、.1 模具結(jié)構(gòu)形式的選擇 ···············································
50、3;······································· 13 4.1.1 模架的選用 ········
51、;··················································
52、;······································ 13 4.1.2 模具的閉合高度 ········
53、3;·················································
54、3;····························· 14 4.2 模具工作部分尺寸計算 ·················
55、183;·················································
56、183;··············· 14 4.2.1 落料凹模 ·······························
57、3;·················································
58、3;·················· 14 4.2.2 拉深凸模 ·····························
59、··················································
60、····················· 14 4.2.3 凸凹模 ··························
61、83;·················································
62、83;··························· 15 II 4.2.4 彈壓御料板 ·················
63、83;·················································
64、83;···························· 16 4.2.5 彈性頂料橡膠的確定 ·················&
65、#183;·················································&
66、#183;············ 17 4.2.6 上墊板 ··································
67、;··················································
68、;···················· 18 4.2.7 壓邊圈 ··························
69、83;·················································
70、83;··························· 18 5 模具的整體安裝 ····················
71、··················································
72、·············· 19 5.1 模具的總裝配 ································
73、83;·················································
74、83;················ 19 5.2 模具零件 ······························
75、183;·················································
76、183;·························· 19 6 選定沖壓設備 ·····················
77、··················································
78、················· 20 7 模具的裝配 ·······························
79、;··················································
80、;··········· 21 7.1 復合模的裝配 ···································
81、183;·················································
82、183;············· 21 7.2 凸、凹模間隙的調(diào)整 ································
83、183;·················································
84、183;···· 21 8 重要零件的加工工藝過程編制 ··········································
85、;·················· 22 小結(jié) ······························
86、3;·················································
87、3;···························· 25 參考文獻 ····················&
88、#183;·················································&
89、#183;······························ 26 III 1設計任務及零件的工藝性分析 1.1 設計任務 Ⅰ 初始條件: ?0.14?0.1材料:08鋼;料厚:1 mm ;中批量,外徑尺寸為700 mm,底孔尺寸為160
90、mm, Ⅱ 要求完成的主要任務: 1、兩底孔圓筒沖壓工藝分析; 2、工藝參數(shù)的計算與模具結(jié)構(gòu)的設計; 3、繪制模具裝配圖(A1)及主要模具零件圖(不少于2張A2),要求制圖符合國家標準,圖面整潔,繪圖工作量折合后不少于1張零號圖紙; 4、撰寫8000字左右的設計計算說明書。內(nèi)容包括緒論、任務書、目錄、正文、參 考文獻等。課程設計說明書要求簡捷明了、層次清晰、計算正確、步驟合理、圖文并茂,按統(tǒng)一規(guī)范格式書寫。 1.2 零件的工藝性分析 沖壓件工藝性是指沖壓零件對沖壓工藝的適應性,一般對沖壓工藝影響最大的是
91、 幾何形狀、尺寸和其精度的高低。雖然沖壓加工工藝過程包括備料—沖壓加工工序—必要的輔助工序—質(zhì)量檢驗—組合、包裝的全過程,但分析工藝性的重點要在沖壓加工工序這一過程里。而沖壓加工工序很多,各種工序中的工藝性又不盡相同。即使同一個零件,由于生產(chǎn)單位的生產(chǎn)條件、工藝裝備情況及生產(chǎn)的傳統(tǒng)習慣等不同,其工 藝性的涵義也不完全一樣。這里我們重點分析零件的結(jié)構(gòu)工藝性。 1 該零件是兩底孔圓孔,如圖1.1,該零件可看成無凸緣的筒形件,料厚t=1mm, ?0.14?0.1拉深后厚度不變;零件底部圓角半徑R=2mm;外徑尺寸
92、為700mm,底孔尺寸為160 mm,其余尺寸公差都為自由公差,滿足拉深工藝對精度等級的要求。 圖1.1 工件圖 工藝性對精度的要求是一般情況下,拉深件的尺寸精度應在IT13級以下,不宜高于IT11級;對于精度要求高的拉深件,應在拉深后增加整形工序,以提高其精度,由于材料各向異性的影響,拉深件的口部或凸緣外緣一般是不整齊的,出現(xiàn)“突耳”現(xiàn)象,需要增加切邊工序。 影響拉深件工藝性的因素主要有拉深件的結(jié)構(gòu)與尺寸、精度和材料。拉深工藝性對結(jié)構(gòu)與尺寸的要求是拉深件因盡量簡單、對稱,并能一次拉深成形;拉深件的壁厚公差或變薄量一般不應超出拉深工藝壁厚變化規(guī)律;當零件
93、一次拉深的變形程度過大時,為避免拉裂,需采用多次拉深,這時在保證必要的表面質(zhì)量前提下,應允許內(nèi)、外表面存在拉深過程中可能產(chǎn)生的痕跡;在保證裝配要求下,應允許拉深件側(cè)壁有一定的斜度;拉深件的徑向尺寸應只標注外形尺寸或內(nèi)形尺寸,而不能同時標注內(nèi)、外形尺寸。 工藝性要求材料具有良好的塑性,屈強比?s/?b值越小,一次拉深允許的極限變形程度越大,拉深的性能越好;板厚方向性系數(shù)r和板平面方向性系數(shù)?r反映了材料的各向異性性能,當r較大或?r較小時,材料寬度的變形比厚度方向的變形容易,板平面方向性能差異較小,拉深過程中材料不易變薄或拉裂,因而有利于拉深成形。 該零件結(jié)構(gòu)較簡單、形狀對稱
94、,完全由圓弧和直線組成,沒有長的懸臂和狹槽;拉深高度不大,且孔在底部拉深非變形區(qū)。零件尺寸除中心孔和外徑尺寸接近IT11級外,其余尺寸均為自由尺寸且無其他特殊要求,利用普通沖裁方法可以達到零件圖樣要求。零件材料為08鋼,為優(yōu)質(zhì)碳素結(jié)構(gòu)鋼,具有良好的結(jié)構(gòu)強度和塑性,其沖裁加工性較好。該零件的沖裁性較好,可以沖裁加工,可用于中批量生產(chǎn)。 2 2 確定工藝方案 2.1 計算毛坯尺寸 在拉深時,雖然拉深件的各部分厚度要求發(fā)生一些變化,但如果采用適當?shù)墓に嚧胧?,則其厚度的變化量還是并不太大。在設計工藝過程時,可以不考慮毛坯厚度的變化。同時由于金屬在塑性變形過程
95、中保持體積不變,因而,在計算拉深件的的毛坯展開尺寸時,可以認為在變形前后的毛坯和拉深間的表面積相等。 該工件為無凸緣圓筒形件,根據(jù)等面積原則采用解析法求毛坯直徑。如圖所示,將工件分為三個簡單的幾何體。 1 確定是否加修邊余量 由于板料在軋壓或退火時所產(chǎn)生的聚合組織而使材料引起殘存的方向性,反映到拉深過程中,就使桶形拉深件的口部形成明顯的突耳。此外,如果板料本身的金屬結(jié)構(gòu)組織不均勻、模具間隙不均勻、潤滑的不均勻等等,也都會引起沖件口高低不齊的現(xiàn)象,因此就必須在拉深厚的零件口部和外緣進行修邊處理。這樣在計算毛坯尺寸的時候就必須加上修邊余量然后再進行毛坯的展開尺寸計算。
96、 零件的相對高度h/d2=(22-0.5)/(70-1)=0.312,而高度h=21.9mm,根據(jù)《沖壓手冊(第二版)》查表4-4可知,修邊余量δ=2mm。 2 計算毛坯直徑 2 D= d1?4d2(h??)?6.28rgd1?8rg 2 d2=70-1=69mm, d1=70-(1+2) ×2=64㎜,h=22-1=21mm, rg=2+0.5=2.5mm。 D=104.63 mm, 3 取D=105mm。 2.2 確定是否需要壓邊圈 坯料相對厚度
97、 t?100%????????????????2.3 D 1??100%?0.952%?1.5% 105 根據(jù)《沖壓手冊(第三版)》表4-75知需要壓邊圈。 2.3 計算拉深次數(shù) 在考慮拉深的變形程度時,必需保證使毛坯在變形過程中的應力既不超過材料的變形極限,同時還能充分利用材料的塑性。也就是說,對于每道拉深工序,應在毛坯側(cè)壁強度允許的條件下,采用最大的變形程度,即極限變形程度。 極限拉深系數(shù)值可以用理論計算的方法確定。即使在傳力區(qū)的最大拉應力與在危險斷面上的抗拉強度相等,便可求出最小拉深系數(shù)的理論值,此值即為極限拉深系數(shù)。但在實際生
98、產(chǎn)過程中,極限拉深系數(shù)值一般是在一定的拉深條件下用實驗的方法得出的,我們可以通過查表來取值。 根據(jù)工件的相對高度 確定拉深次數(shù)。 d69??0.657,其工件的相對高度為0.312,根據(jù)《沖D105 壓手冊(第二版)》表4-18知小于一次拉深時的最大相對高度0.70~0.57,故可以一次th21.5??0.312和坯料的相對厚度?100?0.952的大小Dd269零件的總拉深系數(shù)為m總?拉深成形。根據(jù)th21.5》查得??0.312,?100?0.952,由《沖壓手冊(第二版)Dd269 筒形件(帶壓邊圈)的極限拉深系數(shù)m1?0.53~0.55,而工件的總拉深系數(shù)
99、為0.657>m1,故可一次拉深成形。 因材料為08鋼,具有良好的強度和塑性,其加工工藝性較好,可減小筒形件的首次拉深系數(shù)及增大最大相對高度。 使得m總?m1,hh1?,所以零件只需要一次拉深。 dd1 2.4 確定工藝方案 根據(jù)以上分析和計算,可以進一步明確該零件的沖壓加工需要包括以下基本工序: 4 落料、拉深、沖孔和切邊。 根據(jù)這些基本工序,可以擬出如下幾種工藝方案: 方案一 先進行落料,再拉深,切邊,最后沖孔,以上工序過程都采用單工序模加工。用此方案,模具的結(jié)構(gòu)都比較簡單,制造很容易,成本低廉,但由于結(jié)構(gòu)
100、簡單定位誤差 方案二 落料與拉深、切邊在復合模中加工成半成品,再在單工序模上進行沖孔。采用了落料與拉深、切邊的復合模,提高了生產(chǎn)率。對落料以及拉深的精度也有很大的提高。由于最后一道沖孔工序是在單工序模中完成,使得最后一步?jīng)_孔工序的精度降低,影響了整個零件的精度,而且中間過程序要取件,生產(chǎn)效率不高。 方案三 落料、拉深、沖孔和切邊全都在同一個復合模中一次加工成型。此方案把三個工序集中在一副復合模中完成,使得生產(chǎn)率有了很大的提升。沒有中間的取放件過程,一次沖壓成型,而且精度也比較高,能保證加工要求,在沖裁時材料處于受壓狀態(tài),零件表面平整。模具的結(jié)構(gòu)也非常的緊
101、湊,外廓尺寸比較小,但模具的結(jié)構(gòu)和裝配復雜。 方案四 采用帶料級進多工位自動壓力機沖壓,可以獲得較高的生產(chǎn)效率,而且操作安全,但這一方案需要專用的壓力機或自動的送料裝置。模具的結(jié)構(gòu)比較復雜,制造周期長,生產(chǎn)成本高。 根據(jù)設計需要和生產(chǎn)批量,綜合考慮以上方案,方案三最適合。即落料、拉深、沖孔和切邊在同一復合模中完成,這樣既能保證大批量生產(chǎn)的高效率又能保證加工精度,而且成本不高,經(jīng)濟合理。 很大,而且單工序模一般無導向裝置,安裝和調(diào)整不方便,費時間,生產(chǎn)效率低。 3
102、 主要工藝參數(shù)的計算 3.1 確定排樣、裁板方案 加工此零件為中批量生產(chǎn),沖壓件的材料費用約占總成本的60%~80%之多。因此,材料利用率每提高1%,則可以使沖件的成本降低0.4%~0.5%。在沖壓工作中,節(jié)約金屬和減少廢料具有非常重要的意義,特別是在大批量的生產(chǎn)中,較好的確定沖件的形狀尺寸和合理的排樣的降低成本的有效措施之一。 由于材料的經(jīng)濟利用直接決定于沖壓件的制造方法和排樣方式,所以在沖壓生產(chǎn)中,可以按工件在板料上排樣的合理程度即沖制某一工件的有用面積與所用板料的總 5 面積的百分比來作為衡量排樣合理性的指標。 同時屬于工藝廢料的搭邊對
103、沖壓工藝也有很大的作用。通常,搭邊的作用是為了補充送料的定位誤差,防止由于條料的寬度誤差、送料時的步距誤差以及送料歪斜誤差等原因而沖出殘缺的廢品,從而確保沖件的切口表面質(zhì)量,沖制出合格的工件。同時,搭邊還使條料保持有一定的剛度,保證條料的順利行進,提高了生產(chǎn)率。搭邊值得大小要合理選取。根據(jù)此零件的尺寸通過查表《沖壓工藝與模具設計》表2-5取: 搭邊值為 a?2mm 進距方向 a1?2mm 從視測方面來講,該零件的排樣應該采用直排最合理。 從圖可知:送料步距 S=105+2=107mm????????3.1
104、 條料寬度 b=105+2?2=109mm????????3.2 板料規(guī)格擬用1mm×1000mm×3000mm熱軋鋼板。查《沖壓模具設計》GB708-88,為了操作方便采用橫裁。 裁板條數(shù) n1? 每條個數(shù) n2? 每板總個數(shù) n?n1?n2?27?9?243 材料利用率 B?a11000?2??9個????????3.4 S107A3000??27條????????????3.3 b109 ??n?S面?100%?????
105、????????3.5 A?B 243???1052 ???100% 4?1000?3000 ??70.14% 6 3.2 計算工藝力、初選設備 3.2.1 計算工藝力 (1)落料力 平刃凸模落料力的計算公式為 F?kLt?????????????????3.6 式中 F— 沖裁力(N) L— 沖件的周邊長度(mm) t— 板料厚度(mm) ?—材料的抗沖剪強度(MPa) K— 修正系數(shù)。它與沖裁間隙、沖件形狀、沖裁速度、板料厚度、
106、潤 滑情況等多種因素有關(guān)。其影響范圍的最小值和最大值在(1.0~ 1.3)P的范圍內(nèi),一般k取為1.25~1.3。 在實際應用中,08鋼的抗剪強度?的值是260~360 MPa,取?=320 MPa。 因此,該沖件的落料力的計算公式為 F落?1.3Lt?????????????????3.7 =1.3???105?1?320 =137225N (2)卸料力 一般情況下,沖裁件從板料切下以后受彈性變形及收縮影響。會使落料件梗塞在凹模內(nèi),而沖裁后剩下的板料則箍緊在凸模上。從凸模上將沖件或廢料卸下來所需的力稱卸
107、料力。影響這個力的因素較多,主要有材料力學性能、模具間隙、材料厚度、零件形狀尺寸以及潤滑情況等。所以要精確地計算這些力是困難的,一般用下列經(jīng)驗公式計算: 卸料力 F卸?K1F??????????????3.8 式中 F—— 沖裁力(N) K1——頂件力及卸料力系數(shù),其值可查教材表2-11。 這里取K1為0.04。 因此 F卸?0.04?137225?5489N (3)拉深力 一般情況下拉深力隨凸模行程變化而改變,其變化曲線如圖3.1。從圖中可以看出,在拉深開始時,由于凸緣變形區(qū)材料的
108、變形不大,冷作硬化也小,所以雖然變形區(qū)面積較大,但材料變形抗力與變形區(qū)面積相乘所得的拉深力并不大;從初期到中期, 7 材料冷作硬化的增長速度超過了變形區(qū)面積減少速度,拉深力逐漸增大,于前中期拉深力達到最高點位置;拉深到中期以后,變形區(qū)面積減少的速度超過了冷作硬化增加的速度,于是拉深力逐漸下降。零件拉深完以后,由于還要從凹模中推出,曲線出現(xiàn)延緩下降,這是摩擦力作用的結(jié)果,不是拉深變形力。 拉深力 凸模行程 圖3.1 拉深力變化曲線 由于影響拉深力的因素比較復雜,按實際受力和變形情況來準確計算拉深力是比較困難的。所以,實際生產(chǎn)中通常是以危險斷
109、面的拉應力不超過其材料抗拉強度為依據(jù),采用經(jīng)驗公式進行計算。對于無凸緣圓筒形零件的拉深力近似計算公式為: F拉?Kd2t??b????????????????3.9 式中 d2—圓筒形零件的凸模直徑(mm) K—系數(shù),這里取0.72 ?b—材料的抗拉強度(MPa) t —材料厚度 08鋼抗拉強度為330~450 MPa,取400 MPa。 ?6243N0 因此 F拉?0.72???69?1?400 (4)壓邊力 壓邊力的大小對拉深件的質(zhì)量是有一定影響的,如果過大,就要增加拉深力,因
110、 而會使制件拉裂,而壓邊圈的壓力過小就會使工件的邊壁或凸緣起皺,所以壓邊圈的壓力必須適當。合適的壓邊力范圍一般應以沖件既不起皺、又使得沖件的側(cè)壁和口部不致產(chǎn)生顯著的變薄為原則。壓邊力的大小和很多因素有關(guān),所以在實際生產(chǎn)中,可以根據(jù)近似的經(jīng)驗公式進行計算。 FQ?AFq(N)????????????????3.10 8 式中 A—初始有效壓邊面積(mm2),無凸緣拉深件A??[D2?(d2?2rd)2]/4; rd—凹模圓角半徑,查《沖壓手冊(第二版)》表4-78取5.5mm; Fq—單位壓邊力(MPa),這里經(jīng)查《
111、沖壓手冊(第二版)》得Fq=2.5 MPa 所以有 FQ?AFq??[1052?(69?2?5.5)2]/4?2.5?9081N (5)沖孔力 沖孔力可按下式計算: t??????????????3.11 F沖?kL? 式中 F沖—沖孔力(N) L—沖件的內(nèi)輪廓長度(mm) t—板料厚度(mm) ?—材料的抗剪強度(MPa) 因此,該零件的沖孔力為: F沖?kLt? =1.3???16?1?32
112、0?2 =41821N (6)推件力 將卡在凹模中的材料逆著沖裁力方向頂出所需要的力稱為推件力。 推件力計算公式為: F推?nK2F沖????????????????3.12 ?3?0.055?41821?6900N K2—推件力系數(shù),其值可查教材表2-11,取K2為0.055。 (7)切邊力 切邊力可以按照沖裁力的計算方法獲得,則該工件的切邊力為: F切?kLt??1.3??70?1?320=91483N 3.2.2 拉深功的計算 拉深所需的功可按下式計算
113、 W?CPmaxh????????????????3.13 1000 式中 Pmax—最大拉深力(N) h —拉深深度(mm) 9 W—拉深功(N·m) C—修正系數(shù),一般取為C=0.6~0.8。 所以 W?0.8?62430?21.5?1074N·m??????????3.14 1000 3.2.3 初選壓力機 壓力機噸位的大小的選擇,首先要以沖壓工藝所需的變形力為前提。要求設備的 名義壓力要大于所需的變形力,而且還要有一定
114、的力量儲備,以防萬一。從提高設備的工作剛度、沖壓零件的精度及延長設備的壽命的觀點出發(fā),要求設備容量有較大的剩余。 因F落?F拉,故總沖壓力 F??F落?F卸?F沖?F推?F拉?FQ?F切?????????3.15 =?137225? ?5489?41821?6900?62430?9081?91483 =354.429KN 應選的壓力機公稱壓力P0??1.3~1.6?F?取為1.5,則公稱壓力為: P0?1.5F??532KN???????????????3.16 因此初選閉式單點壓力機JC 23—630開式可傾壓力機。
115、 3.2.4 計算壓力中心 本零件為對稱幾何體,其壓力中心就在它的圓心處,不必計算它的壓力中心。 3.2.5 計算凸、凹模刃口尺寸及公差 沖裁件的尺寸精度取決于凸、凹模刃口部分的尺寸,沖裁間隙的合理也要靠凸、 凹模刃口部分的尺寸來實現(xiàn)和保證,所以正確確定刃口部分的尺寸是相當重要的。在決定模具刃口尺寸及制造公差時,需考慮以下原則:①落料件的尺寸取決于凹模的磨損,沖裁件的尺寸取決于凸模尺寸。②考慮到?jīng)_裁時凸、凹模的磨損,在設計凸、凹模刃口尺寸時,對基準件刃口尺寸在磨損后變大的,其刃口公稱尺寸應取工件尺寸范圍內(nèi)較小的數(shù)值;對基準件刃口尺寸在磨損
116、后減少的,其刃口公稱尺寸應取工件尺寸范圍內(nèi)較大的數(shù)值。這樣,在凸模磨損到一定程度的情況下,任能沖出合格的零件。③在確定模具刃口制造公差時,要既能保證工件的精度要求,又要保證合理的間隙數(shù)值。 10 凸凹模加工有兩種方法: (一) 采用凸凹模分別加工,凸凹模分別加工是指在凸模與凹模分別按各自圖樣上標注的尺寸及公差進行加工,沖裁間隙由凸凹模刃口尺寸及公差保證,這樣就需要分別計算出凸模和凹模的刃口尺寸及公差,并標注在凸凹模設計圖樣上,這樣加工方法具有互換性,便于成批制造,主要用于簡單,規(guī)范形狀(圖形,方法或矩形)的沖件。 (二)凸凹模配合加工,對于形狀復雜或薄料
117、沖裁剪的沖裁,為了保證凸、凹模之間有一定的間隙值,一般采用配合加工。凸凹模工作部分尺寸計算:其落料件按凹模磨損后尺寸增大(A類尺寸)、減?。˙類尺寸)和不變(C類尺寸)的規(guī)律分三種。 ①落料時,因為落料件表面尺寸與凹模刃口尺寸相等或基本一致,應該先確定凹模刃口尺寸,即以凹模刃口尺寸為基準,又因為落料件尺寸會隨凹模刃口的磨損而增大,為了保證凹模磨損到一定程度仍能沖出合格零件,故凹?;境叽鐟撊÷淞霞叽绻罘秶鷥?nèi)的較小尺寸,落料凸模的基本尺寸則是凹?;境叽缟蠝p去最小合理間隙。 如按分別加工的方法計算,則: ??d????????????3.17 Dd?(D?X?
118、)0 Dp?(Dd?Zmin)0 ??p???????????3.18 式中 Dp—落料凸模刃口尺寸(mm); Dd—落料凹模刃口尺寸(mm); D —落料件外徑公稱尺寸(mm); ?— 沖裁工件要求的公差; ?p、?d—凸、凹模制造公差; X —磨損系數(shù)。 對于未標注公差可按IT14級計算,得落料件尺寸為?1050 ?0.87mm,根據(jù)教材上表 2-1查得,沖裁模刃口雙面間隙: Zmin?0.10mm,Zmax?0.13mm ?d、?p—凹、凸模制造
119、偏差,查教材表2-3得?d=0.035mm,?p=0.025mm。 ?d+?p=0.035+0.025=0.06mm;Zmax?Zmin?0.13?0.10?0.03mm。 校核間隙:?d+?p>Zmax?Zmin,相差較大,不符合|?p|+|?d|?Zmax?Zmin條件,故采用配合加工的方法。磨損系數(shù)根據(jù)教材表2-4得X=0.5。 ??d(?d=?/4) ???????????3.19 Dd?(D?X?)0 11 ?0.22?0.22 =(105?0.5?0.8)0=104.5650 Dp?(Dd?Zm
120、in)0 ??p???????????3.20 =(104.565?0.10)0.4650 ?0.22=104?0.22 ?0.1②沖孔時,對于沖孔160mm孔,根據(jù)教材表2-3得,?p??d?0.020mm,校核 間隙:|?p|+|?d|=0.04mm,|?p|+|?d|>Zmax?Zmin,但相差不大,可作如下調(diào)整。 ?p?0.4(Zmax?Zmin)???????????3.21 =0.4?0.03 ?0.012mm ?d?0.6(Zmax?Zmi)n???????????3.22
121、 ?0.6?0.03 ?0.018mm 磨損系數(shù)根據(jù)教材表2-4得X=0.75。 則 dp?(d?X?)0???????????3.23 ??p =(16?0.75?0.1)0 ?0.012 =16.0750 ?0.012 d dd?(dp?Zmi)???????????3.24 n0?? ?0。018 =(16.075?0.1)0 ?0。018
122、 =16.1750 ③拉深時,因一次拉深成形,按最后一次拉深工序計算,拉深凹模和凸模的尺寸和公差應按零件的要求來確定。當工件的外形尺寸及公差有要求時,以凹模為基準,先確定凹模尺寸,因凹模尺寸在拉深中隨磨損的增加而逐漸變大,故凹模的尺寸開始時應取小些,為 ?? Dd?(D?0.75?)0d???????????3.25 凸模尺寸為 Dp?(D?0.75?-2C)??p?????? ?3.26 拉深凸模和凹模的單邊間隙C=1.1t=1.1mm,凸凹模制造公差查
123、《沖壓手冊(第二版)》表4-76得,對于拉深尺寸?70mm,?d?0.08mm,?p?0.05mm。 12 0 則,凹模尺寸為:Dd?(D?0.75?)0d ?0.08 =(70?0.75?0.14)0 ?0.08 =69.8950mm ?? 式中 D—拉深件外形尺寸; Dd—凹模尺寸; ?—拉深件公差。 0D?(D?0.75?-2C)凸模尺寸為:p??p 00(70?0.75?0.14-2.2)=?0.05=67.6
124、95?0.05mm ④切邊刃口尺寸可按落料凸凹模的尺寸計算方法計算,切邊凹模尺寸與拉深凹模尺寸一樣,切邊凸模尺寸為凹模尺寸減去最小雙邊間隙,公差與拉深凸模取相同值即可。 則: Dp?(Dd?Zmin)0 ??p???????????3.27 =(69.895?0.1)0 ?0.05mm =69.7950 ?0.05 4 模具的結(jié)構(gòu)設計 4.1 模具結(jié)構(gòu)形式的選擇 4.1.1 模架的選用 采用落料、拉深、沖孔、切邊復合模,首先要考慮落料凸模(兼拉深
125、凹模)的壁厚是否過薄。本次設計中凸凹模的最小壁厚為7.2mm,滿足鋼材最小壁厚a?1.2t?1.2?1?1.2mm的要求,能夠保證足夠的強度,故采用復合模。 模具采用倒裝式。模座下的橡膠緩沖器兼作壓邊與頂件,另外還設有彈性卸料裝置和彈性頂件裝置。這種結(jié)構(gòu)的優(yōu)點是操作方便,出件暢通無阻,生產(chǎn)效率高,缺點是彈性卸料板使模具的結(jié)構(gòu)變復雜,要簡化可以采用剛性卸料板,其缺點是拉深件留在剛性卸料板中不易取出,帶來操作上的不便,結(jié)合本次設計綜合考慮,采用彈性卸料板。 從生產(chǎn)量和方便操作以及具體規(guī)格方面考慮,選擇后則導柱模架,由凹模外形尺寸?180mm,(GB/T2851.3—81)在按其
126、標準選擇具體結(jié)構(gòu)尺寸如下 上模座 315?200?50 HT200 13 下模座 315?200?65 HT200 導 柱 35?230 20Cr 導 套 35?125?48 20Cr 凸緣模柄 ?50?68 45鋼 模具閉合高度 MAX 240mm MIN 285mm
127、4.1.2 模具的閉合高度 所謂的模具的閉合高度H是指模具在最低工作位置時,上下模座之間的距離,它應與壓力機的裝模高度相適應。 模具的實際閉合高度,一般為: H模?上模座厚度?墊板厚度?沖頭長度?凹模厚度? 下模座厚度?沖頭進入凹模深度?????4.1 該副模具使用上墊板厚度為42mm,凸模固定板厚度為16mm。如果沖頭(凸凹模)的長度設計為46mm,凹模(落料凹模)設計為60mm,則閉合高度為: H模?50?42?46?60?65-2?261mm 4.2 模具工作部分尺寸計算 4.2.1 落料
128、凹模 落料凹模采用圓形板結(jié)構(gòu)和直接通過螺釘、銷釘與下模座固定的固定方式。因中批量生產(chǎn),考慮凹模的磨損和保證零件的質(zhì)量,凹模刃口采用直刃壁結(jié)構(gòu),刃壁高度h?12mm,漏料部分沿刃口輪廓適當擴大(為便于加工,落料凹模漏料孔可設計成近似于刃口輪廓的形狀,如凹模圖)。凹模輪廓尺寸確定如下: 凹模厚度60mm,凹模壁厚30mm, 凹模的材料選用Cr12,工作部分熱處理淬硬58~62HRC。 4.2.2 沖孔凸模 沖孔凸模刃口部分為圓形,為便于凸模和固定板的加工,可設計成階梯形結(jié)構(gòu),并將安裝部分設計成便于加工的長圓形,通過螺釘緊固在固定板上,用銷釘定
129、位。凸模的尺寸根據(jù)刃口尺寸、卸料裝置和安裝固定要求確定。凸模的材料選用Cr12,工作部分熱處理淬硬58~62HRC。 對于沖孔凸模,依據(jù)《沖壓手冊(第三版)》表14-76確定為圓柱頭縮桿圓凸模,工作長度為14mm,總長為46mm。 14 4.2.3 凸凹模 該復合模中有上凸凹模和下凸凹模兩個凸凹模,是主要工作零件。 ①上凸凹模(如圖4.1所示),其外形作為落料凸模內(nèi)形又作為拉深凹模,并且內(nèi)、外形刃口部分都為圓形,為便于凸凹模與凸模固定板的配合,凸凹模的安裝部分設計成便于加工的長圓形,通過螺釘緊固在凸模固定板上,并用銷釘定位。 凸
130、凹模的自由長度為: L=推料板厚度+拉深件外形高度=22+29=51mm。????????4.2 圖4.1 上凸凹模 ②下凸凹模(如圖4.2所示),其外形作為拉深凸模內(nèi)形又作為沖孔凹模,并且內(nèi)、外形刃口部分都為圓形,為便于凸凹模與下模座和落料凹模的配合,凸凹模的安裝部分設計成便于加工的長圓形,通過螺釘緊固在凸模固定板上,并用銷釘定位。 凸凹模的自由長度為: 15 L=落料凹模高度+凸凹模固定板高度-沖頭進入沖孔的深度=60+16-1=75mm。????????4.3 圖4.1 下凸凹模 4.2.4 彈壓式卸料板
131、 ①彈性元件的設計 為了得到較平整的工件,此模具采用彈壓式卸料結(jié)構(gòu)。彈簧和橡膠是模具中廣泛應用的彈性元件。主要為彈性卸料、壓料及出件裝置供彈壓力。彈壓卸料裝置是由卸料板、彈性元件(彈簧或橡膠)、卸料螺釘?shù)攘慵M成。 根據(jù)模具安裝位置擬選4個彈簧,每個彈簧的預壓力為: F0?Fx/n 式中:Fx為沖裁卸料力; n為彈簧個數(shù)。 所以 F0?Fx/n =5489/4 =1372.25N 查《沖壓手冊(第二版)》表10-1,初選彈簧規(guī)格為8mm×60mm× 170mm
132、 16 其余件參數(shù)是D=60mm,d=8mm,h0=170mm,t=18.3mm,hj=78.4mm, Fj=1370N,n=8.5 D——彈簧中徑;d——材料直徑;t——節(jié)距;Fj——工作極限負荷;h0——自由高度;n——有效圈數(shù);hj——工作極限負荷下變形量。 ?H0?F0hj=61.6mm Fj 如滿足下列條件,則彈簧選的合適。 hj??H0?h工?h修模 ?H??H0?h工?h修模 (△H為彈簧實際總壓縮量) 式中h工工為卸料板工作行程,一般取料厚加l mm,所以h工=1
133、.8mm,h修模為凸凹模修 磨量,一般取4—1Omm,h修模取=4mm,所以, hj??H0?h工?h修模 =61.6+2+6mm =69.6mm<78.4mm,故滿足條件。 卸料板的外形尺寸確定為280mm?140mm?8mm。 4.2.5 彈性頂料橡膠的確定 因為沖孔廢料如果設計稱凹模通孔自由落下的形式會與下模座下方的彈性頂料裝置沖突,故由彈性橡膠將沖孔廢料頂出。由于受到橡膠允許承受的載荷較大,安裝,調(diào)整,靈活,方便,因而是沖裁模中常用的彈性元件,沖裁模中用于卸料的橡膠有合成橡膠和聚氨脂橡膠,其中聚氨脂的性
134、能比合成橡膠優(yōu)異,是常用的卸料彈性元件。 為了保證卸料正常工作,應該使橡膠的預緊的預壓力: Fy?FX ??????????????4.4 橡膠的壓力與壓縮量之間不是線形關(guān)系,橡膠的壓縮時產(chǎn)生的壓力按下式計算: F?AP???????????????4.5 式中 A——橡膠的橫截面積 P——橡膠與單位壓邊力(MPa),其值與橡膠的壓縮量,形狀及 尺寸有關(guān) 計算橡膠的自由高度,由下式 H自?(3.5~4)S工作 ????????????????
135、4.5 ??1mm 17 H自?3.5?(1?1?4) ?21mm 計算橡膠的裝配高度,由下式 HL?H自?H預??????????????????4.6 H預?(0.1~0.15)H自 ?????????????? 4.7 按公式計算得: H預?0.13?21?2.73mm HL?21?2.73?18.27mm 4.2.6 上墊板 墊板的作用是直接承受和擴散凸模傳遞的壓力,以降低模座所受的單位壓力,防止模座被壓出陷痕而損壞。在設計中我們把墊板的外形尺寸與凸凹模的外形尺寸相匹配,其上梁厚度我們設計為10mm。在上墊板上設計了一個推桿孔,以便安裝推桿,還有四個螺釘孔以及兩個銷孔,這些都是為了與凸凹模和拉深凸模上的各種固定零件的安裝相匹配的。 4.2.7 壓邊圈 在這個設計中,壓邊圈借助頂桿所施的頂件力,既起到壓邊的效果,又起來把拉深 件頂出拉深凸模,設計高度為23mm。 18 5 模具的整體安裝 5.1 模具的總裝配 由以上
- 溫馨提示:
1: 本站所有資源如無特殊說明,都需要本地電腦安裝OFFICE2007和PDF閱讀器。圖紙軟件為CAD,CAXA,PROE,UG,SolidWorks等.壓縮文件請下載最新的WinRAR軟件解壓。
2: 本站的文檔不包含任何第三方提供的附件圖紙等,如果需要附件,請聯(lián)系上傳者。文件的所有權(quán)益歸上傳用戶所有。
3.本站RAR壓縮包中若帶圖紙,網(wǎng)頁內(nèi)容里面會有圖紙預覽,若沒有圖紙預覽就沒有圖紙。
4. 未經(jīng)權(quán)益所有人同意不得將文件中的內(nèi)容挪作商業(yè)或盈利用途。
5. 裝配圖網(wǎng)僅提供信息存儲空間,僅對用戶上傳內(nèi)容的表現(xiàn)方式做保護處理,對用戶上傳分享的文檔內(nèi)容本身不做任何修改或編輯,并不能對任何下載內(nèi)容負責。
6. 下載文件中如有侵權(quán)或不適當內(nèi)容,請與我們聯(lián)系,我們立即糾正。
7. 本站不保證下載資源的準確性、安全性和完整性, 同時也不承擔用戶因使用這些下載資源對自己和他人造成任何形式的傷害或損失。