數(shù)控雕刻機外文翻譯
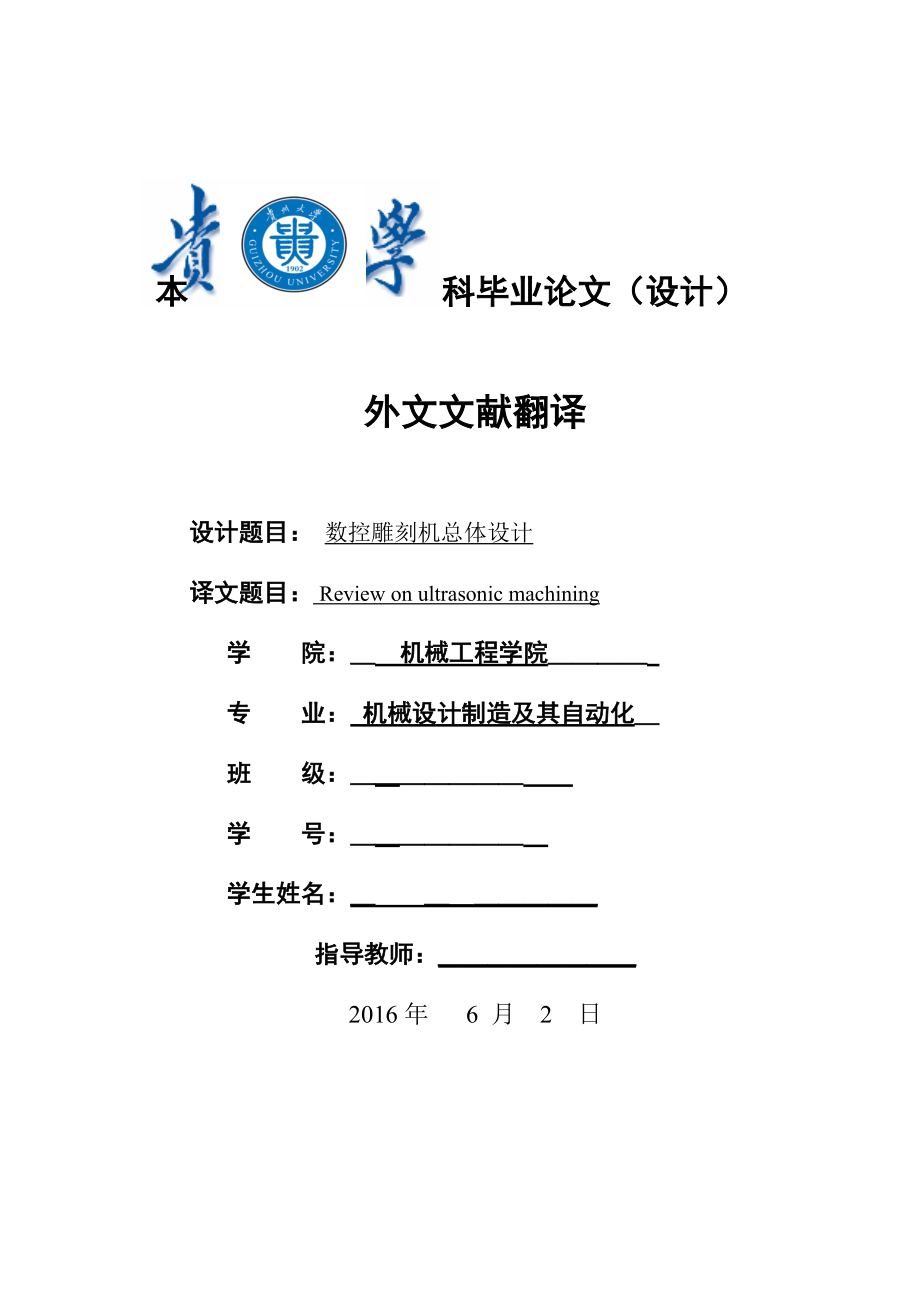


《數(shù)控雕刻機外文翻譯》由會員分享,可在線閱讀,更多相關《數(shù)控雕刻機外文翻譯(40頁珍藏版)》請在裝配圖網(wǎng)上搜索。
1、 貴州大學本科畢業(yè)論文(設計)外文文獻翻譯 本科畢業(yè)論文(設計) 外文文獻翻譯 設計題目: 數(shù)控雕刻機總體設計 譯文題目:?Review on ultrasonic machining 學 院:_ 機械工程學院____ 專 業(yè): 機械設計制造及其自動化_ 班 級:_______ 學 號:_______ 學生姓名:_ _______ 指導教師:________ 2016年 6 月 2 日 超聲波加工綜述 T. B. THOE, D.K.ASPINWALL and M. L. H. W
2、ISE 摘要 超聲波加工適合切削不導電、脆性材料,例如工程陶瓷。與其他非傳統(tǒng)加工,如激光束、電火花加工等不同,超聲波加工不會導致工件表面熱損傷或顯著的殘余應力,這對脆性材料尤其重要。超聲波加工的基本原理,包括材料去除原理,各類操作參數(shù)對材料切除率、刀具磨損、工件精確度要求都有敘述,并著重表述了在加工工程陶瓷上的應用,制造復雜的三維立體陶瓷的問題也在敘述當中。 1 概述超聲波加工及其應用 超聲波加工是一種非傳統(tǒng)機械切削技術,通常與低材料去除率有關,它并不被加工材料的導電率和化學特性所限制,它用于加工金屬和非金屬材料,非常適合于脆性大,硬度高于40HRC[6–12]的材料,比如無機
3、玻璃、硅片、鎳、鈦合金等等 [13–24],有了它,76um 的小孔也能加工,但是被加工的孔深度與直徑之比限制在 3 比 1 之內 [8, 12]。 超聲波加工的歷史可以追溯到 1927 年,R. W. Wood 和 A. L. Loomis 發(fā)表的論文,1945年。有關于超聲波的第一項專利給了 L. Balamuth,現(xiàn)在超聲波加工已經(jīng)分化很多領域,超聲波鉆削、超聲波切削、超聲波尺寸加工、超聲波研磨技術和懸浮液鉆孔法,然而,在 20世紀 50 年代初只普遍知道超聲波沖磨或 USM[8,25, 28, 30, 31]。 在超聲波加工中,高頻率的電能通過換能器/增幅器被轉變?yōu)闄C械振動,之后通
4、過一個能量集中裝置被傳送出去, 例如變幅桿/刀具組件[1, 17, 18, 30, 32]。這導致刀具沿著其縱向軸線以振幅 0-50μm 高頻率振動(通?!?0KHz)[16, 33, 34],典型額定功率范圍從50~3000W[35]不等,在某些機器上可以達到 4kw。一個受控靜負載被施加于刀具和磨料懸浮液(由研磨材料的混合物組成、例如碳化硅,碳化硼等等,懸浮在水或油中)被泵傳送到切削區(qū)域,刀具的振動導致磨料顆粒懸浮在刀具和工件表面間,通過微型片沖擊工件表面從而去除材料[19]。圖 1 展示了設置 USM 使用磁致伸縮或壓電換能器釬焊和螺紋加工。 基本的結構變更包括: ·旋轉超聲波加工。
5、刀具啟動同時開始旋轉,這樣可以將圓柱度降低至傳統(tǒng)超聲波加工所達到的值的 1/3[41],典型回轉速度約為 300rpm,但若使用金剛石鑲嵌刀具,回轉速度可高達 5000rpm。 ·超聲波加工結合電火花加工[16, 18, 20, 26, 34, 36]。 ·超聲波輔助常規(guī)/非常規(guī)加工 [16, 18, 20, 26, 34, 36]。相對于傳統(tǒng)的車削加工,超聲輔助車學加工聲稱可減少加工時間、工件的殘余應力和加工硬化,提高工件表面質量和刀具壽命[12, 36, 42, 45]。 ·非加工超聲波應用,例如清潔、塑料/金屬焊接、化學制品加工、涂層和金屬成形。 1.1 超聲波加工技術應用于仿形
6、加工 很多超聲波加工涉及一些用簡單或者復合的工具軸向穿透橫截面進入工件的鉆削,用于得到合乎要求的通孔和盲孔,三維的孔也需要(就是一個面上有不同深度的孔),一個類同于開模的加工過程通常包括[7, 10, 27, 37, 43, 46–48],如圖 2 ,使用這種石墨電極技術的放電機能夠在 30 分鐘內成型零件,而不是用仿形銑削花 20 小時完成它[2, 4,49, 50],使用復合刀具的問題在于它受加工面上相同加工效率和磨耗率,這些都會影響產(chǎn)品的成型,另外有一個更大問題,就是怎樣跟傳統(tǒng)刀具相比最大幅度地發(fā)揮復合刀具的性能。 圖 1 USM 上端基本組成部分 圖 2 利用 USM 進
7、行氮化硅渦輪葉片鉆孔 一種替代的方法是使用一種簡單的“筆狀”刀具和使用數(shù)控程序仿形,見圖 3。最近,使用這種技術的可行性已經(jīng)引起關注并且已被一些國家研究,包括英國、法國、瑞士、日本等等[26, 52],一些 CNC 控制回路的旋轉超聲加工系統(tǒng)已在市面上有售,比如來自 ExtrudeHone Limited (法國)的 SoneX 300,來自 Erosonic AG (瑞士)的 he Erosonic US400/US800。 圖 3 利用 USM 加工碳纖維復合材料的加速桿、孔和外輪廓 1.2 超聲波加工陶瓷材料 高性能陶瓷越來越多地被用于航空航天,工業(yè)和汽車
8、電子行業(yè)的應用。它們?yōu)槠囬y和氣缸套提供了許多比金屬的更優(yōu)越的性能[14,15],并且其良好的化學穩(wěn)定性和高耐熱性提高了燃氣渦輪機應用中獲得更大的熱效率的可能性[30,53,54]。燒結氧化鋁,碳化硅和氮化硅產(chǎn)品一般有大于 1500 HV 的硬度,因此通常金剛石磨削是唯一可行/經(jīng)濟的加工零件至最終成形的方法,雖然這在加工包括圓柱形元件,平板和彎曲表面零件時是理想可行且易于接受的,但是當被加工表面具有更復雜的形狀或者其工作特性要求有特定的工件表面完整性時就會出現(xiàn)問題。 大多數(shù)工程陶瓷是電絕緣體,盡管這可能是其功能上的優(yōu)點,但在加工部分零件如陶瓷或陶瓷涂層渦輪機葉片時就成了一個顯著的缺點。相當多
9、數(shù)量的金屬依靠于大量使用非傳統(tǒng)加工,例如電化學加工(ECM)和 EDM,前者被廣泛用于生產(chǎn)翼型型材,后者則用于葉片冷卻孔的加工。不幸的是,這兩個加工過程都依賴于工件材料是導電的。在 EDM 中,工件需要具有小于 100 的Ωcm 的電阻率[16, 26, 33, 55]。 對于加工過程中高應力集中的安全規(guī)定部件如渦輪葉片,其工件表面完整性是一個關鍵的特性,因此這類零件會特別使用陶瓷或陶瓷涂層。加工過程中應盡可能減少最終成型表面/亞表面的損傷。所有傳統(tǒng)的切削操作,如車削或磨削都或多或少的會導致某些類型的表面損傷[24, 48, 56]。非傳統(tǒng)加工過程也是如此,例如 EDM 或激光加工(LBM)
10、所依賴的熱切削機制。舉個例子,EDM 會導致熱表面區(qū)域產(chǎn)生最高達 50μm 深的微裂紋[55]。與此相反,超聲波加工(USM)是一種不依賴于導電工件并且適合于陶瓷材料加工的非熱過程。該方法可產(chǎn)生很少甚至沒有表面/亞表面損傷或施加特定的壓力機制。尺寸精度可達±5μm[36],最終表面的粗糙度 Ra 可實現(xiàn) 0.51-0.76μm[37]。對石墨,碳化硅和一系列陶瓷材料的 USM數(shù)據(jù)來由 Gilmore[6],Kremer[33]總結于表 1 中。 2 超聲加工刀具的基本原理 2.1 超聲發(fā)生器 generator)和超聲換能器(Transducers) 傳統(tǒng)的發(fā)生器系統(tǒng)中,裝配了變幅桿
11、(horn)和刀具,通過機械調整其規(guī)模達到共振調諧,然而,最近共振發(fā)生器已實現(xiàn)其功能,它可自動調整輸出高頻率去匹配變幅桿/刀具組件的精確諧振頻率[6]。它們可以也適應裝配和刀具磨損的任何微小錯誤,給出最小聲波能量損耗和非常小的發(fā)熱性[33]。供給的功率取決于換能器的大小[35]。有些超聲發(fā)生器的設計帶有安全特性,如在變幅桿斷裂,變幅桿/刀具接頭故障等[17,31,33]情況的自動開關。 換能器的振動在縱向或壓縮模式。在工業(yè)中的應用,不論磁致伸縮 [12, 26, 40, 57]或是壓電裝置 [35, 39]都會使用,是因為它的低 Q 值(Q 是一個能量峰值銳度的度量),磁致伸縮換能器允許
12、振動通過很寬的頻率傳輸帶傳輸(例如,20KHz 的發(fā)生器為 17-23KHz)[58].它也允許變幅桿有更大的設計靈活性并且可以適應刀具磨損。此外,變幅桿還可重復設計/加工幾次而不會有臨界振幅損失[4, 30, 46]。磁致伸縮換能器主要的缺點是其高電力損失(例如電渦流損失)和低能量效率(約等于 55%)[40],這些損失以熱的形式出現(xiàn),換能器必須空冷/水冷而且換能器的體積龐大笨重,而且,相比于壓電型,該換能器不適于產(chǎn)生高強度振動 [59, 60],典型的壓電換能器 [26, 42, 53, 61]由兩盤鋯鈦酸鉛或其他合成陶瓷組成[62],其厚度通常不到超聲波換能器總長的 10%[63]。壓電
13、傳感器有更高的能量效率(約等于90~96%),因此不需要任何冷卻[18,28, 59]。它不易產(chǎn)生熱損傷,并且更容易適應旋轉操作[61]并且更容易安裝。 2.2 超聲變幅桿和刀具組件 變幅桿被稱為聲耦合器,速率/機械轉換器,刀架,集中器,樁模塊或超聲波發(fā)生器,見圖 4。換能器表面的振幅過?。?.001-0.01μm)而無法達到合適的切削率,因此,變幅桿可作為放大設備。對每種變幅桿材料 [65]來說,其最佳調諧都是不同的,因此需要控制高機械 Q 值、良好的焊接和釬焊性、良好的聲傳輸特性、在高工作振幅下的高抗疲勞特性,并且也應耐腐蝕和有足夠高的強度來附加螺紋附件,蒙乃爾銅鎳合金,鈦 6-4(I
14、MI 318),AISI304 不銹鋼,鋁和鋁青銅合金是常用的材料[1, 4, 20, 40, 64–67]。 該刀具的設計應該能提供在給定頻率的波腹內的最大振幅[61],所使用的材料應具有高耐磨性、電阻性,較好的彈性,抗疲勞強度并且有該應用下最佳的強度和硬度 [16, 27, 64]。碳化鎢,銀器鋼鐵,蒙泰爾銅鎳合金,是較常用的刀具材料。多晶金剛石(PCD)近來被用于加工非常堅硬的工件材料,例如熱等靜壓氮化硅[68]。 刀具可以通過敢接或釬焊,螺紋/錐度配合連接到變幅桿,另外,實際刀具的結構可以被加工在變幅桿的末端[14, 27, 35, 66, 70, 71],螺紋接頭由于換刀的快速和
15、易用被照例使用,然而,還是存在些問題,例如自松動,聲功率損耗,疲勞失效等[72]。但使用開孔刀具進行深孔鉆時,通過變幅桿和刀具的中心進給磨料的能力是一個很大的優(yōu)勢,可以因此減少側向摩擦力[27]。 2.3 刀具進給的推進機制和磨料供給系統(tǒng) 刀具通常經(jīng)由配重/靜態(tài)重量,彈簧,氣/液或電磁進給系統(tǒng)施加靜態(tài)負載使之置于工件之上[16, 26,27, 40, 73],為獲得最佳效果,加工時系統(tǒng)應保持相同的工作力方向,并且保持對切削方向阻力的足夠的敏感性[16, 40]。施加的力必須仔細選擇,因為若設置太低就無法達到最大的切削速度,若設置太高則會導致刀具和磨料之間的干擾[3, 70]。比較有代表性的
16、靜負載值約為 0.1-30N,鉆直徑小于 0.5mm 的小孔時的力要特別注意,在太高的負載下有可能導致刀具彎曲。 圖 4.各類帶/不帶刀具頭的變幅桿[69] 懸浮液通常是在刀具表面由泵噴射出,吸出,或二者相結合,正如圖 5 中所示[13, 16, 28,40, 74]。它是變幅桿、刀具,工件的冷卻劑,為切割區(qū)域提供新的磨料,從切割區(qū)域清除碎屑 [2, 25, 27, 28],懸浮液同時也提供了刀具、磨料和工具間的聲結合,允許高效的能源轉換,橫向進給的管道是與變幅桿的波節(jié)面相連接(相鄰),以此來避免阻尼的影響[16,27]。最普通的磨料材料常用氧化鋁,碳化硅,碳化硼,等等[4, 12,
17、24, 27, 37, 75–78],磨料輸送媒介應控制低粘度并且接近磨料密度,良好的濕潤性,較好和較高的熱導率,高效的高溫冷卻性,親水性,盡量滿足這些要求[3, 26, 28]。 圖 5.懸浮液傳輸方法[13, 16, 28, 40, 74] 3 材料去除原理 Shaw[35],Miller [79], Cook [80], Rozenberget al.[7] and others [22, 23, 43, 60]已經(jīng)對材料去除原理做了大量的工作,這些原理在圖 6 中有詳細敘述,其包含了: ·直接錘擊工件表面的研磨顆粒所導致的機械磨損[10, 28, 34, 35, 3
18、7, 40, 50, 60, 70, 81]; ·沖擊自由移動研磨顆粒所產(chǎn)生的微小碎屑[28, 35, 37, 50, 70,81, 82]; ·來自研磨懸浮液的氣穴現(xiàn)象效果 ·與流體有關的化學作用 上述機理的單獨或聯(lián)合作用通過切變[13, 36, 70]或斷裂(對硬性材料或加工硬化材料)[13] 去除工件材料,材料的去除是在表面上,不需要移動,同時表面上有短暫的塑性變形[13,36]。 多孔材料如石墨與硬化鋼和陶瓷相反,對于材料去除來說,氣蝕具有重大的貢獻[10, 23,28, 35, 37, 81],Markov [21]等人[27, 35]認為氣蝕和化學效應是第二大重要性,多數(shù)
19、工件材料作用本質上是削弱工件表面,協(xié)助磨料循環(huán)利用和排除碎屑,在 RUM 中,Komaraiahetal.[83] 和 Enomoto [84] 發(fā)現(xiàn)在脆性材料中赫茲裂縫的形成所要求的靜負載要小于滑動縮進。 圖 6 USM 材料去除原理 [81]. 3.1 各種操作參數(shù)對材料去除率的影響 在加工前可以通過加速器 [10],電渦流探針[30, 85],激光多普勒測量儀(dopplermeter)[86],激光斑點干涉儀[58]測量超聲刀具振幅ξ,通過使用高轉化率刀具,如換能器直徑比率 [27, 39],獲得高頻振幅,理想情況下,為了優(yōu)化切割速度 [3, 4, 6, 10, 13, 24
20、, 49, 66],振幅應該與粗磨料平均直徑相等,Shaw [35] 認為了 MRR∝ξ3/4,其他研究者[77, 79,87]認為MRR∝ξ,也有部分人認為頻率和靜負載恒定時 MMR∝ξ2。通常的,當?shù)毒哒駝拥姆仍黾訒r MRR 增加(其他變量不變)[40, 77],盡管如此,還是存在一個使 MRR 降低的振幅水平,如圖 7 所示。 一些作者[6, 27, 75] 認為,MRR∝f2直到 f 為 400Hz。在更高的頻率(直到 5kHz),頻率和 MRR 被發(fā)現(xiàn)存在線性關系,超過一個上限值后,MRR 迅速下降,Rozenberg 等人[7]和 Kainth 等人[22]認為,在實際操作中,
21、其他參數(shù)不變,靜態(tài)負載從零增加,MRR 和靜態(tài)負載存在近似線性關系。超過一個最佳值后,由于到達變幅桿/工件相接面的磨料顆粒大小的減小和懸浮液循環(huán)不足[7, 16, 26, 43, 60, 75, 88, 90],MRR 也隨之減少,最大加工速度的最佳靜負載被發(fā)現(xiàn)是取決于刀具結構(例如橫截面積和形狀)和磨粒平均尺寸,如圖 8 所示,Kops [92]表明,采用一種小于最佳值(基與 MRR)的靜負載,可以更好地減少磨料磨損和提高刀具壽命。 圖 7 振幅和穿透速度的影響 磨料硬度應該比工件材料高,通常,更大的磨料尺寸[2, 5, 19, 27, 35, 70, 93]和更高的懸浮液濃度[3,
22、 13, 23, 28, 59,66, 81]可以達到更高的 MRR,增加磨粒尺寸或懸浮液濃度,可以達到最佳 MRR 值,其他方面的提高都難以使更大的磨粒到達切割區(qū)域 [5, 7, 10, 40, 60, 87]或使 MRR 下降,懸浮液濃度建議為 30% [1, 13, 27, 59, 77, 87, 94],Kazantsev [74]宣稱無需提高磨粒尺寸或機器功率,懸浮液的強制輸送提高了 USM 的輸出。與抽吸泵系統(tǒng)相比較,它產(chǎn)生了 2-3 次更高的 MRR。就 MRR 而言,水的性能通常優(yōu)于其他油類如苯和甘油水溶液,Pentland 等地和其他國家發(fā)現(xiàn)提高懸浮液循環(huán),氣穴現(xiàn)象,污染物和
23、堵塞效應能被減少甚至克服。 雖然超聲波加工允許工件材料可硬可軟,但是脆性材料更適合用這種加工方法,硬性材料通過脆性斷裂被切除而不是塑形斷裂,像低碳鋼這種塑形材料是通過塑形斷裂切除的,在這種情況下,磨粒會容易被嵌進工件[12, 13, 28, 36],降低工件材料斷裂韌度或者以楊氏模量的比率增加刀具的硬度講導致更高的 MMR[25, 41, 55, 84],如圖 9 和圖 10,工件材料的機械性能和它的斷裂形式對于它采用何種加工形式是很重要的。 根據(jù)已有的報告顯示,切削率跟刀具的形式和形狀系數(shù)(刀具的周長和面積之比)成正比[16, 60, 77, 79]。該刀具的形式是由耐懸浮液循壞定義,窄
24、的矩形截面的刀具于具有相同面積的正方形截面的刀具相比,前者能產(chǎn)生較高的加工速率[16, 40, 87],如圖 11 所示,Goetze[77]報告稱對于相同接觸區(qū)域的刀具,周長較長的刀具更具有滲透率的上升空間,產(chǎn)生這個影響的主要原因是磨料漿在加工區(qū)域充分發(fā)散由困難[3, 16, 40, 96]。 對于較小截面積的刀具而言,如何在靜載荷下調整出最佳加工狀態(tài)變得非常重要,這會使得在相同條件下,切削率會更好(見圖 8)。有一些學者[70, 71, 77, 90]研究出套料刀具最佳的條件是內部直徑與外部直徑之比大約為 0.45,刀具的厚度下限是不小于 5 倍的磨粒粒度[16, 27]。刀具材料的硬度
25、影響 MRR,刀具的磨損率,工件的精度等[41]。Komaraiah[97]和其他等人已經(jīng)研究出,各種刀具材料優(yōu)劣排名如下 1.Nimonic80A , 2.釷鎢, 3.銀器鋼,4.不銹鋼,5.馬氏體時效鋼, 6.鈦,7.低碳鋼,Neppiras[27]用了其他刀具材料給了如下排名 1.鎢碳化物,2.黃銅,3.低碳鋼,4.銀器鋼,5.不銹鋼,6.銅,用金剛石做刀具能表現(xiàn)出良好的材料去除特性和非常低的磨損率。 圖 8 在不同截面下靜負載和穿透速度的對比 圖9影響陶瓷斷裂韌度的USM MRR和相對磨損(55) 圖10 不同材料在USM & RUM 下,不同的H/E對MRR 的影響
26、 圖11 相同截面積的刀具的不同形狀對MRR的影響 在旋轉超聲波加工中,刀具的旋轉能增強 MRR,工件的精度,在一些情況下還能減少切削力[12, 76],增加了刀具的壽命[27]. 在相同條件下旋轉超聲波加工中 MRR 是用金剛石進行磨削時的 6 倍左右,是傳統(tǒng)超聲波加工的 4 倍,Komaraiah et al. [83]等人表示旋轉超聲波加工比傳統(tǒng)超聲波加工性能優(yōu)越的原因可以用工件表面的壓痕,工件和刀具之間的游離磨粒,晶粒之間的滑動接觸來解釋,對于旋轉超聲波加工,Prabliakar [66] 和 Komaraiah [90]等人表示較高的轉速得到了較高的材料去除率,在一般情況下,
27、最佳的鉆孔深度應該是該刀具直徑的 2 到 5 倍之間,但是在懸浮液不斷供給的條件下得到的[16, 87]。 4 刀具磨損 刀具磨損是超聲波加工的一個重要變量,既影響材料去除率和孔的精度[38, 28, 87, 94,98],在超聲波加工中,復合刀具的磨損圖案可分為縱向磨損 WL [71, 87, 94], 橫向,側向,徑向磨損 WD [99], 有些會出現(xiàn)氣蝕和吸入磨損現(xiàn)象[38, 71, 75, 100]。 4.1 各個運行參數(shù)對刀具磨損的影響 Adithan [71] and Venkatesh [38]研究表明,刀具磨損在一個特定點時最大,這時 MRR 也是最大的,材料去除率
28、下降超出了這個最佳靜載荷點,當使用較硬較粗糙的磨粒時,刀具磨損趨于增大如圖 12 所示,因此,相同截面積的刀具[38, 99]。硬質磨粒如碳化硼和軟質材料如碳化硅相比,前者會導致更加嚴重的刀具磨損,刀具磨損也會受工件的硬度影響,也會被工件的韌性影響,那種性能變得堅韌的陶瓷不太合適用超聲波加工,它會導致很高的刀具磨損量,它比常規(guī)陶瓷需要更高的加工速率[6, 101]。 如果刀具硬度增加是由加工硬化引起的,那么磨粒會進入刀具,從而導致工件材料去除率降低,此外,工件的偏移會更加嚴重,這樣導致工件形成凸面,也會使刀具中心產(chǎn)生塑形變形,形成碟狀,此外,研究發(fā)現(xiàn)對于所有刀具材料而言刀具外緣的硬化程度最高
29、,中間最小[97].所以,例如黃銅和銅是不適合做道具材料,因為它們在大振蕩和大振幅下會產(chǎn)生很多毛刺[3, 30],他們降低聲波頻率衰減應力波,使用硬質金屬如碳化鎢來降低塑形變形和刀具磨損量[48]。 為了降低 WL,H,和沖擊力,像一些具有高價值的硬性材料如 Nimonic 80A),它的推薦參數(shù)如圖 13 所示,H 和 not Ki 顯著影響著 WD[97],要對所有刀具材料全面地評估 WD 和WL,建議使用 Nimonic 80A,釷鎢,銀鋼[3, 97]。伴隨的孔的深度[71]和切削時間[10, 11]的增加,刀具的磨損會成線性增加。 5 超聲波加工對工件表面光潔度和粗糙度的影響
30、 超聲波加工不會明顯的發(fā)熱,這樣可以避免局部發(fā)生熱損傷和殘余應力,磨粒粒度大小會顯著影響工件精度和工件表面粗糙度[4, 23, 26, 36, 40, 73, 82, 94],在超聲波加工中,降低粒度的大小能得到較低的表面粗糙度如圖 14 所示,加工孔的精度也會提高,孔的底部的精度會比孔內壁高[2, 5, 7, 60, 86, 102]。Dam 等人認為當切削速度和切削深度降低的時候能得到更高的表面光潔度。 提高表面光潔度的方法上面已介紹[16, 23, 27,86, 87],Koval’chenko[5]和 Kennedy[16]指出在孔底面加工一個平面是非常困難,因為在加工平面上懸浮液
31、分布不均勻,導致刀具中心的有效磨粒減少,尤其是工件是硬陶瓷,稍好的表面光潔度可以用硬度和粗糙度較低的材料獲得[2]。 圖 12.磨料粒度對刀具磨損的影響 圖 13.產(chǎn)品的硬度和沖擊強度對刀具縱向磨損的影響 圖 14.碳化硼的粒度大小對表面粗糙度的影響 用超聲波加工的孔的生產(chǎn)精度必須采取尺寸精度和形狀精度面(圓柱度和錐度),入口的精度值是最大的,隨著切削深度增加而增加,增加量相當于一個磨粒值的上線,直徑長度的比值的增加會導致橫向震動的增加從而造成更大的偏差,[40, 50]。Shaw [35]和其他研究者[3,23,40, 73, 83]研究表明通過降低磨粒大小,并抑制刀具的
32、橫向震動能增加靜態(tài)載荷,從而減少了表面粗糙度,因此也能提高圓柱度和錐度,如圖 15 所示,Adithan [73]等人發(fā)現(xiàn)得到的矩形孔的精度明顯比用鉆得到的高,如圖 16 表明具有高楊氏模量的材料更容易受非圓柱度影響。 圖 15 靜負載對圓柱度的影響 影響尺寸精度和形狀精度的因素還有聲學元件和超聲波刀具的精度[16, 27, 40, 73]??梢酝ㄟ^碳化鎢和不銹鋼[73],作為刀具材料,內部懸浮液循環(huán)[23, 73, 86],負前角,細磨料[16, 23,27, 40, 87]來減少錐度,增加刀具的震動幅度和使用粗磨粒能提高進入工件的穿透力,Kremer[23]等人發(fā)現(xiàn)超聲波產(chǎn)生的石墨
33、的原因是由于氣穴現(xiàn)象面,污染影響了表面光潔度引起的。 Markov [87]認為是表面粗糙度影響 MRR,然而 Komaraiah 表明各種材料的表面粗糙度在傳統(tǒng)超聲波和旋轉超聲波加工均有體現(xiàn),如圖 17 在精加工中用機油代替水的操作被認為能增加表面光潔度,但卻導致切削速率的降低[16, 23, 27, 40, 87],工件哪里需要高精度,在加工階段必須始終執(zhí)行,尺寸精度為±5 μm 可以在很多材料中獲得[36],如圖 16 所示,更細的磨粒能得到更低的表面粗糙度[40]。 圖 16.H/E 對圓柱度和 MRR 的影響 懸浮液:180 網(wǎng)狀 SiC,回轉速度 200rpm 6 變幅桿
34、和刀具的設計 變幅桿的設計理論和結構,很多學者都研究過,但是卻還是不明了[7, 63, 67, 104–106],傳統(tǒng)變幅桿的設計是基于一個考慮彈性力和慣性力的無窮小的平衡微分方程,然后在其整合的情況下,元件和變幅桿能產(chǎn)生共振[56, 106, 107],變幅桿的長度取決于工作頻率,并且對能量放大器沒影響,典型的設計包括:圓柱形,階梯,錐形和指數(shù)型[11,88,107],調諧從換能器這里結束,其中 10-15 毫米應要進行調諧[16,25,40,65,107,108]。然而,在助力器變幅桿,任何降低的情況下在長度必須做到使兩端減小同樣維持其正確共振。不遵守此規(guī)則將導致結點,從轉變點換能器的前
35、身支持,這將導致不必要的壓力,最終導致變幅桿的故障。 圖 17 在 USM&RUM 下 H/E 對不同材料的表面粗糙度的影響 圖 18.根據(jù)音叉原理設計的變幅桿縱向和橫向作用 最近有限元分析應用到軸對稱變幅桿的設計,該方法可以考慮到刀具的重量和用于漿料運輸?shù)娜靠缀蛯⑵涔潭ㄔ趽Q能器所需的諧振頻率,有限元分析也評估工作應力是否在確定的安全范圍之內[67],Dam 等人表示可以設計出一個變幅桿能將縱向超聲波左右轉換成縱向和橫向作用,如圖 18,這種橫向作用有利于輪廓形成。 變幅桿的振動限制了直徑小于 100 的小形狀切削過程[53],通常長度超過 2–3 mm 的刀具會降低大約 0
36、.5–1 kHz 的諧振頻率,但是當鉆孔很深,這個孔的效率損失會被刀具自身產(chǎn)生的共鳴所克服,一般推薦的刀具長度與直徑之比應小于 20 比 1[12] ,但是如果刀具的長度超過 10mm,那么變幅桿的重量應與刀具重要相同[11],刀具設計的詳細指導由Rozenberg 等人完成。 7 總結 1.USM 的是一種不依賴于導電工件的非熱過程,并且很適合于低延展性和硬度高于40HRC 的工件加工。 2.USM 被認為是一個應力和損壞自由的過程。 3.對輪廓 USM 推薦使用共振發(fā)生器,自動調整輸出高頻率去匹配變幅桿/刀具組件的精確諧振頻率。它也可以適應裝配和刀具磨損的任何微小錯誤,給出最小
37、聲波能量損耗和非常小的發(fā)熱性。 4.形狀復雜的生產(chǎn)可以通過使用一個簡單的工具造型和 CNC 雕刻來實現(xiàn) 而非堅持用復雜的工具,然而,該工作區(qū)域只是在早期階段。 5.變幅桿材料應具有較高的機械 Q 值,良好的焊接和釬焊的特點,良好的聲學傳播特性和高工作幅度高耐疲勞性。他們也應該是耐腐蝕,具有足夠高的強度來附加螺絲附件。 6.刀具材料應具有高的耐磨性,良好的彈性和抗疲勞強度特性,并具有該應用下最佳的韌性和硬度。 7.它是變幅桿、刀具,工件的冷卻劑,為切割區(qū)域提供新的磨料,從切割區(qū)域清楚碎屑 ,懸浮液同時也提供刀具、磨料和工具間的聲結合,允許高效的能源轉換。 8.磨料輸送媒介應控制低粘度并
38、且接近磨料密度,良好的濕潤性,較好和較高的熱導率,高效的高溫冷卻性。 9.最大加工速度的最佳靜負載被發(fā)現(xiàn)是去取決于刀具結構(例如橫截面積和形狀),振幅和磨粒平均尺寸。10.研磨材料應比工件硬,并且通常較大的磨粒尺寸和更高的懸浮液濃度產(chǎn)生更高的MRR。 11.降低工件斷裂韌性或增加工具的硬度比至楊氏模量,將得到更高的 MRR。 12.RUM 超過標準 USM 鏡頭的優(yōu)異性能可以通過解釋工件表面的壓痕的聯(lián)合作用,之間的滑動接觸上的游離磨粒/工件之間的刀具/工件和滾動接觸嵌入式粒。 13.變幅桿和刀具的設計在提供諧振 USM 系統(tǒng)最大限度地去除材料中發(fā)揮了重要作用。 P
39、II: S0890–6955(97)00036-9 REVIEW ON ULTRASONIC MACHINING T. B. THOE,? D. K. ASPINWALL??§ and M. L. H. WISE? (Received 23 January 1996; in final form 30 April 1997) Abstract Ultrasonic machining is of particular interest for the cutting of non-conductive, brittle workpiece materials such as engi
40、neering ceramics. Unlike other non-traditional processes such as laser beam, and electrical discharge machining, etc., ultrasonic machining does not thermally damage the workpiece or appear to introduce significant levels of residual stress, which is important for the survival of brittle materials i
41、n service. The fundamental principles of ultrasonic machining, the material removal mechanisms involved and the effect of operating parameters on material removal rate, tool wear rate and workpiece accuracy are reviewed, with particular emphasis on the machining of engineering ceramics. The problems
42、 of producing complex 3-D shapes in ceramics are outlined. Keywords Ultrasonic machining;?contour machining;?ceramics 1. An overview of ultrasonic machining and applications Ultrasonic machining (USM) is a non-conventional mechanical material removal process generally associated with low mater
43、ial removal rates, however its application is not limited by the electrical or chemical characteristics of the workpiece materials. It is used for machining both conductive and non-metallic materials; preferably those with low ductility?1,2,?3,?4?and?5and a hardness above 40 HRC?6,?7,?8,?9,?10,?11?a
44、nd?12, e.g. inorganic glasses, silicon nitride, nickel/titanium alloys, etc.?13,?14,?15,?16,?17,?18,?19,?20,?21,?22,?23?and?24. Holes as small as 76?μm in diameter can be machined?[25], however, the depth to diameter ratio is limited to about 3:1?8?and?12. The history of ultrasonic machining (USM)
45、began with a paper by R. W. Wood and A. L. Loomis in 1927?26?and?27and the first patent was granted to L. Balamuth in 1945?7,28?and?29. USM has been variously termed ultrasonic drilling; ultrasonic cutting, ultrasonic dimensional machining; ultrasonic abrasive machining and slurry drilling. however,
46、 from the early 1950s it was commonly known either as ultrasonic impact grinding or USM?8,?25,?28,30?and?31. In USM, high frequency electrical energy is converted into mechanical vibrations via a transducer/booster combination which are then transmitted through an energy focusing device, i.e. horn/
47、tool assembly?1,?17,?18,?30?and?32. This causes the tool to vibrate along its longitudinal axis at high frequency (usually ≥20?kHz) with an amplitude of 5–50?μm?16,33?and?34. Typical power ratings range from 50–3000?W?[35]and can reach 4?kW in some machines. A controlled static load is applied to th
48、e tool and an abrasive slurry (comprising a mixture of abrasive material; e.g. silicon carbide, boron carbide, etc. suspended in water or oil) is pumped around the cutting zone. The vibration of the tool causes the abrasive particles held in the slurry between the tool and the workpiece, to impact t
49、he workpiece surface causing material removal by microchipping?[19].?Fig. 1?shows the basic elements of an USM set up using either a magnetostrictive or piezoelectric transducer with brazed and screwed tooling. Fig. 1.?Basic elements of USM head?28,?36,?37,?38,?39?and?40. Variations on this basi
50、c configuration include:– ?Rotary ultrasonic machining (RUM). Here the tool is excited and simultaneously rotated so reducing out-of-roundness to about 1/3 the values obtained in conventional USM[41]. Typical rotational speeds are ≈300?rpm, but with diamond impregnated tools, rotational speeds can
51、be as high as 5000?rpm. ?USM combined with electrical discharge machining (EDM)?16,?18,?20,?26,?34?and?36. ?Ultrasonic assisted conventional/non-conventional machining. USM assisted turning is claimed to reduce machining time, workpiece residual stresses and strain hardening, and improve workpiece
52、 surface quality and tool life compared to conventional turning12,?36,?42,?43,?44?and?45. ?There are also non-machining ultrasonic applications such as cleaning, plastic/metal welding, chemical processing, coating and metal forming. 1.1. Contour machining using ultrasonic techniques Many USM appl
53、ications are involved in drilling where a tool of either simple or complex cross section penetrates axially into the workpiece, to produce either a through or blind hole of the required dimensions. Where a three dimensional cavity is required (i.e. one in which the depth varies), a process analogous
54、 to die sinking is generally employed?7,?10,?27,?37,?43,46,?47?and?48, see?Fig. 2. Using this technique graphite electrodes for EDM have been shaped in 30 minutes instead of the 20 hours required by copy milling?2,?4,?49?and?50. The problem with using tools of complex form, however, is that they are
55、 not subject to the same machining rate over the whole of their working surface and experience differential wear rates, both of which affect the product shape?[51]. In addition, there are also greater problems in tuning a complex tool to achieve maximum performance compared to more basic tools. F
56、ig. 2.?Silicon nitride turbine blade counter-sunk using USM?[7]. An alternative approach is to use a simple “pencil” tool and contour machine the complex shape with a CNC programme, see?Fig. 3. Recently, the feasibility of using this technique has become of interest and has been investigated in a n
57、umber of countries including the UK, France, Switzerland, Japan, etc.?26?and?52. A few CNC controlled path rotary USM systems are available commercially such as the SoneX 300 from Extrude Hone Limited (France); and the Erosonic US400/US800 from Erosonic AG (Switzerland). Fig. 3.?Carbon fibre comp
58、osite acceleration lever, holes and outline pro by USM?[7]. 1.2. Ultrasonic machining of ceramic materials Advanced ceramics are increasingly being used for applications in the aerospace, automotive and electronics sectors of industry. They offer a number of advantages over metals for automotive v
59、alves and cylinder sleeves?14?and?15and their good chemical stability and high temperature performance offers the possibility of greater thermodynamic efficiency in gas turbine applications?30,?53?and?54. Sintered alumina, silicon carbide and silicon nitride products generally have a hardness >1500?
60、Hv and therefore diamond grinding is usually the only feasible/economic method of machining components to final shape. While this may be acceptable and perfectly feasible with components that comprise cylindrical, flat and curved surfaces, problems can arise where the surface to be machined has a mo
61、re complex topography or where in-service operating characteristics dictate a particular workpiece surface integrity. The majority of engineering ceramics are electrical insulators and although this can be an advantage in terms of function, it is a significant disadvantage in relation to the machin
62、ing of components such as ceramic or ceramic coated turbine blades. Equivalent metal products rely a great deal on the use of non-conventional processes, such as electro-chemical machining (ECM) and EDM. The former is used extensively for the production of aerofoil sections while the latter is used
63、for the machining of blade cooling holes. Unfortunately, both processes rely on the fact that the workpiece material is conductive. In the case of EDM, the workpiece needs to have an electrical resistivity of less than 100?Ωcm?16,?26,?33?and?55. With any safety critical component such as a turbine
64、blade, which is highly stressed during operation, workpiece surface integrity is a key feature and particularly so where the component is made of ceramic or employs a ceramic coating. The machining process used should impart as little damage as possible to the finished surface/sub-surface. All conve
65、ntional cutting operations such as turning or grinding will to a lesser or greater degree cause some type of surface damage?24,?48?and?56. This is also true of non-conventional processes, such as EDM or laser beam machining (LBM) which rely on a thermal cutting mechanism. For example, EDM can cause
66、a thermally altered surface zone up to 50?μm deep with microcracking?[55]. In contrast, ultrasonic machining (USM) is a non-thermal process which does not rely on a conductive workpiece and is suited to the machining of ceramic materials. The process produces little or no surface/sub-surface damage or impose particular stress regimes. Quoted dimensional accuracy is ±5?μm?[36]and surface finishes of Ra 0.51–0.76?μm can be achieved?[37]. USM data on graphite, silicon carbide and a range of cerami
- 溫馨提示:
1: 本站所有資源如無特殊說明,都需要本地電腦安裝OFFICE2007和PDF閱讀器。圖紙軟件為CAD,CAXA,PROE,UG,SolidWorks等.壓縮文件請下載最新的WinRAR軟件解壓。
2: 本站的文檔不包含任何第三方提供的附件圖紙等,如果需要附件,請聯(lián)系上傳者。文件的所有權益歸上傳用戶所有。
3.本站RAR壓縮包中若帶圖紙,網(wǎng)頁內容里面會有圖紙預覽,若沒有圖紙預覽就沒有圖紙。
4. 未經(jīng)權益所有人同意不得將文件中的內容挪作商業(yè)或盈利用途。
5. 裝配圖網(wǎng)僅提供信息存儲空間,僅對用戶上傳內容的表現(xiàn)方式做保護處理,對用戶上傳分享的文檔內容本身不做任何修改或編輯,并不能對任何下載內容負責。
6. 下載文件中如有侵權或不適當內容,請與我們聯(lián)系,我們立即糾正。
7. 本站不保證下載資源的準確性、安全性和完整性, 同時也不承擔用戶因使用這些下載資源對自己和他人造成任何形式的傷害或損失。